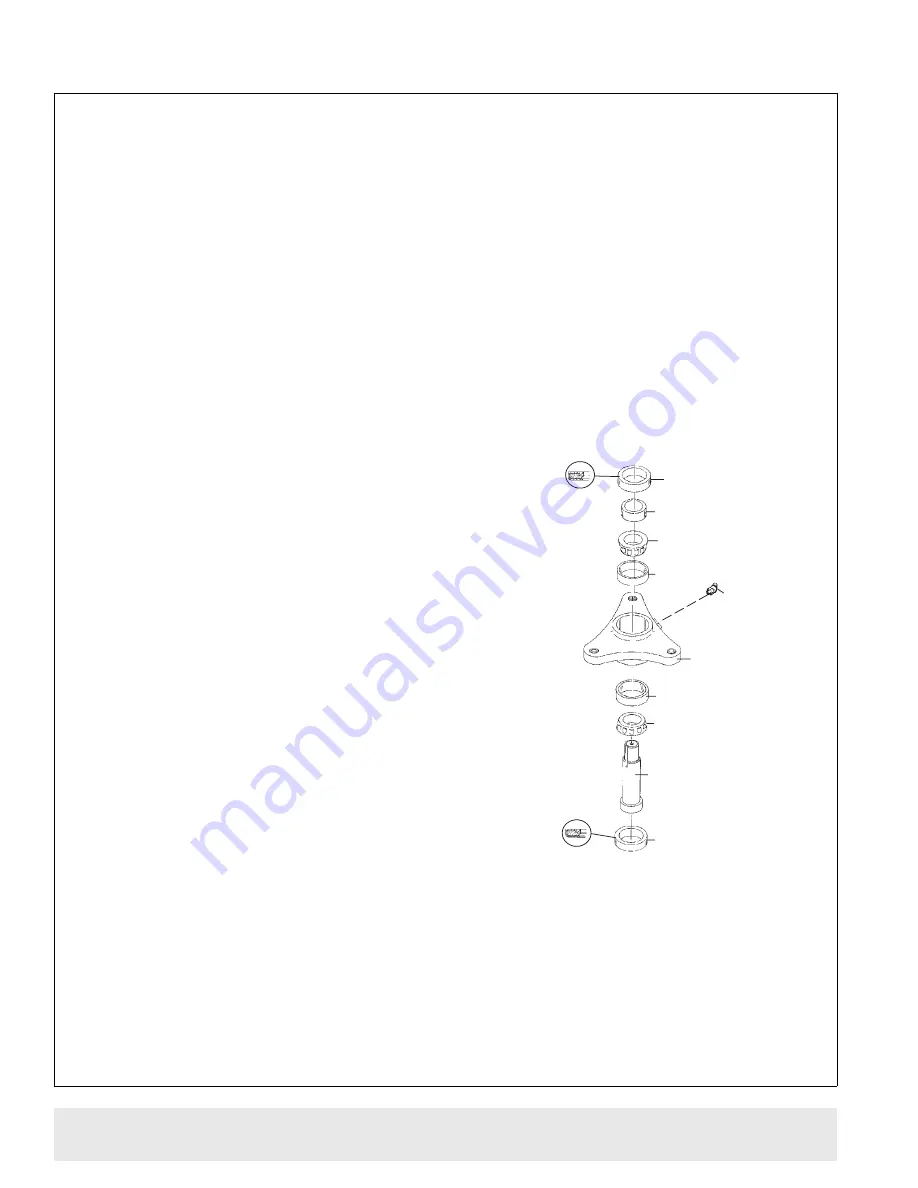
20 Dealer Service
MAN0137 (9/14/01)
DEALER SERVICE
Cont’d
Assemble Blade Spindle
IMPORTANT
■
Bearing adjustment is set by pressing sleeve
against bearing cone until proper adjustment is
attained.
■
Improper positioning of seals can cause seal
failure.
1.
Bearing cups and cones are designed to work
together. It is important to position them so the bear-
ing cone taper mates with bearing cup taper.
2.
Lubricate new cups (6) with a light oil. Place them
in spindle housing (5) so they will mate with cones (4).
Seat cups (6) against machined shoulder of housing
with a press or by placing a large drift on the flat lip
and driving them into housing.
3.
Place bottom bearing cone (4) onto spindle shaft
(8) with taper up. Seat on bottom shoulder of shaft
with a press.
4.
Insert shaft and bearing cone assembly through
bottom of housing (5). Fill housing cavity with a lithium
grease of #2 consistency with a MOLY (molybdenum
disulfide) additive.
5.
Place top bearing cone (4) on shaft (8) to mate
with top bearing cup. Install sleeve (3) on shaft and
press sleeve and bearing cone onto shaft until all
bearing free play is removed and there is a slight
drag. Check by spinning spindle. It should turn freely.
NOTE:
Be careful not to over-tighten bearings. Proper
bearing adjustment is essential to good bearing life.
Should you over-tighten bearings, hold spindle hous-
ing and rap spindle shaft with a hammer and wood
block to loosen bearings. Readjust bearings until
proper setting is obtained.
6.
Proper seal installation is important. An improp-
erly installed seal will leak and could cause bearing
failure.
7.
Pull the rubber portion of seal back and locate
spring.
8.
Apply a thin coat of lubricant to bottom seal (2)
and install with spring up toward center of housing.
9.
Place bottom seal squarely onto housing. Select
a piece of pipe or tubing with an OD that will sit onto
outside edge of seal. A tube that is too small will bow
seal cage.
10.
To prevent distortion to metal seal cage, carefully
press seal into housing. Seal should seat firmly and
squarely against machined shoulder in housing.
11.
Make sure seal lip did not roll under. Distortion to
seal cage or damage to seal lip will cause seal to
leak. Damaged seals must be replaced.
12.
Apply a thin coat of lubricant to top seal (2) and
install with spring facing up away from center of hous-
ing. Top seal should be flush with top of housing.
13.
Lubricate spindle with a lithium grease of #2 con-
sistency with a MOLY (molybdenum disulfide) addi-
tive. Vent bottom seal with a blunt edged tool such as
a letter opener while filling with grease. Rotate hous-
ing on spindle shaft, checking for free movement.
Figure 10
Spindle Repair
1.
Spindle Assembly
2.
Seal
3.
Sleeve
4.
Bearing cone
5.
Housing
6.
Cup
7.
Grease fitting
8.
Shaft
2
8
4
6
5
7
6
4
3
2
DB3403