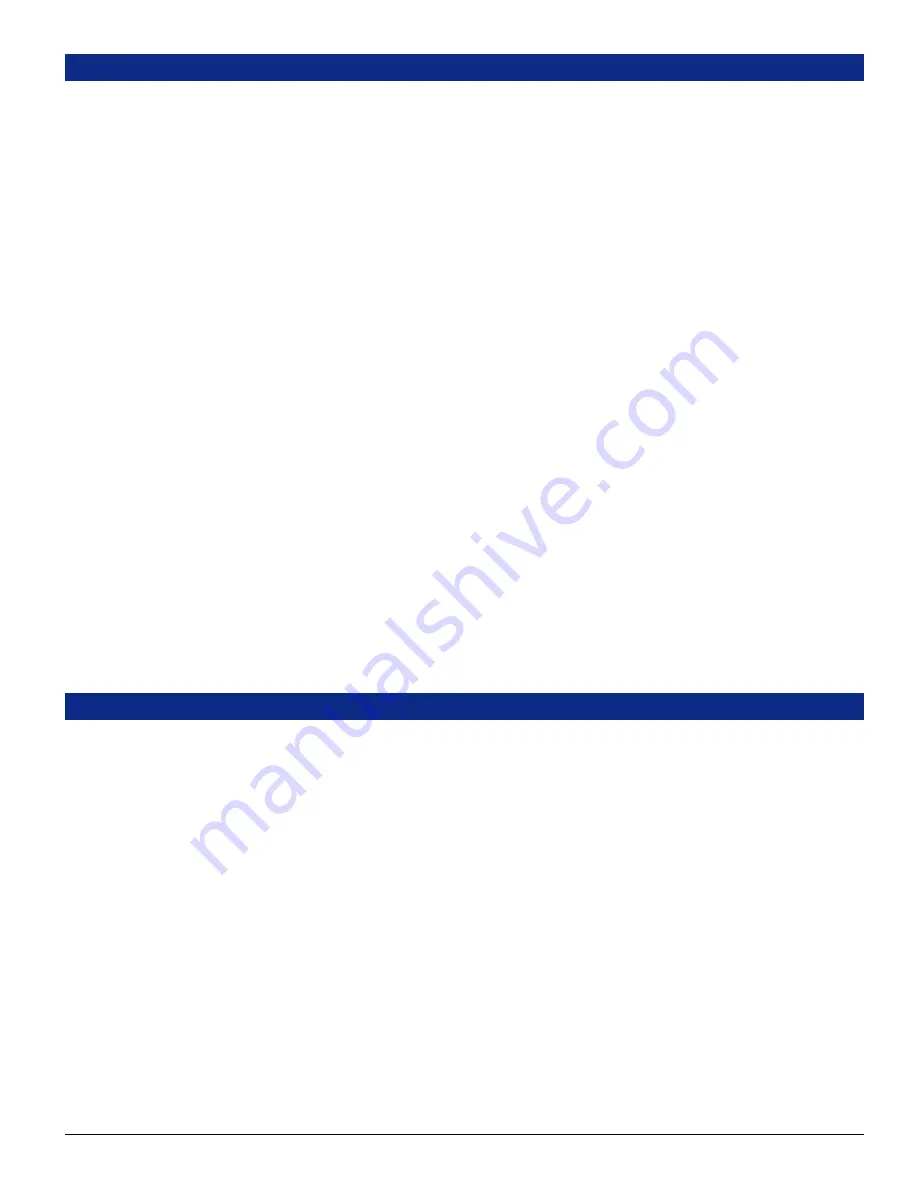
AMP1-DA
User Manual P/N
821530
Rev-
C
© 2006 Wohler Technologies Inc. ALL rights reserved
17
AES/EBU to Analog Converter Module PCB Circuit Description
There are four primary and three ancillary sections comprising the 919117 AES/EBU digital to analog converter:
1) Input source selection.
2) Audio data extraction.
3) Digital to analog conversion.
4) Analog buffer/output amplifiers.
5) Power suppy, Reset, and Error indication.
Input Source Selection (IC13)
Each of the two selectable signal inputs are transformer-coupled to the inputs of a one-of-two active buffer/switch (IC13). The
output of this switch is applied to the receiver stage of the AES receiver/unframer.
Audio Data Extraction (IC11)
"Header" and ancillary data are removed from the recovered input datastream, yielding a datastream having only alternating left/right
channel audio data which is output on pin 26 of IC11.
Digital to Analog Conversion (IC10)
The "pure" audio datastream, along with a data clock and a channel ID (left/right) clock, are applied to a 20 bit two channel D to A
converter (IC10), where the datastream is converted into left and right analog outputs.
Analog buffer (IC4) / Output Amplifiers (IC8, IC9)
Buffer/amps provide balanced left and right channel outputs as well as single ended outputs. Gain calibration, the analog level which
corresponds to a given digital value, is settable via a DIP switch. The default factory setting is 20 dB below "full code" (digital zero)
to equal +4 dbu (0.775V). The other three settings possible are for -18 dBfs = 0 dBu, -9 dBfs = +6 dBu, and -20 dBfs = +8 dBu.
See page
18
for DIP switch location and settings.
Power Supply
The 24V rail internal to the rest of the unit is converted to +5V for digital portions of the 919117 PCB by switching regulator IC12.
Error Indication
The AES status LED is a bicolor LED (Red/Green). It is green as long as a valid digital data strean is being received. The 8412
receiver is capable of distinguishing two types of error conditions: 1) Faulty data; data identified by the sending device (possibly
invalid), or 2) Faulty reception; errors in reception of data or no data stream at all. The red LED indication may be set to occur for
only faulty reception (section 1 closed) or with either faulty data OR faulty reception (section 1 open). See
Item B
, page
10
for
more information regarding this setting.
An additional feature of the AES signal error detection is the ability to mute the audio when errors are detected in the AES signal. To
enable this feature, a jumper is placed at H12 of the 919117 PCB. See page
21
for location of H12 on the 919117 PCB.
Power Characteristics
A +5 voltage (DC) is fed directly to a 4-channel
Input Level Meter Engine
PCB (
919174
). Bargraph brightness is regulated from
the
Bargraph Driver
PCB (
919173
).
4-Channel Input Level Meter Engine Boards (919174)
The analog input signals or digital input signals (after conversion from digital to analog) are inputted to the discrete
Input Level
Meter Engine
PCB. This PC boards responsibility is to process tasks such as digital signal processing (
DSP
), frequency
response, integration time, and display mode. The
ADSP-2184
chip on each input board handles the entire processing function.
A 6-section DIP switch module is located at the rear of these boards, which can be accessed from the rear panel. A combination of
DIP switch settings can be use to auto- calibrate the line level input to "
0
", set the
Reference Level
, or select the
Display Mode
.
See page
18
for for information regarding these DIP switch settings. A 10-section DIP switch module is located at the front of these
boards, which can only be accessed by removing the top cover of the unit (see page
20
for DIP switch locations). A combination of
DIP switch settings can be use to select the level meter
Peak Hold
, select
PPM Ballistics
, or select any of the
Alternative Level
Meter Scales
. See page
19
for information regarding these DIP switch settings.
Bargraph Driver (919173) and Bargraph Display Boards (919172)
All the signal information processed from the
Input Level Meter Engine
PC boards is transfered to the
Bargraph Driver
PCB
(
919173
) through a 10-pin color coded cable. The
Bargraph Driver
PCB is in turn connected by a cable to the
Bargraph
Display
PCB (
919172
), which holds the actual
LED Bargraph Module
at the front panel. The
Bargraph Driver
PCBs accept
fixed-length word serially, and latch the outputs for the bargraph segments corresponding to those bits in the received word, which
are set high.
Brightness of the bargraph displays can be adjusted to a desired setting by adjusting the trimpot located on the front panel. All
bargraph displays are simultaneously adjusted with this one trimpot.
General Level Meter PCB Descriptions