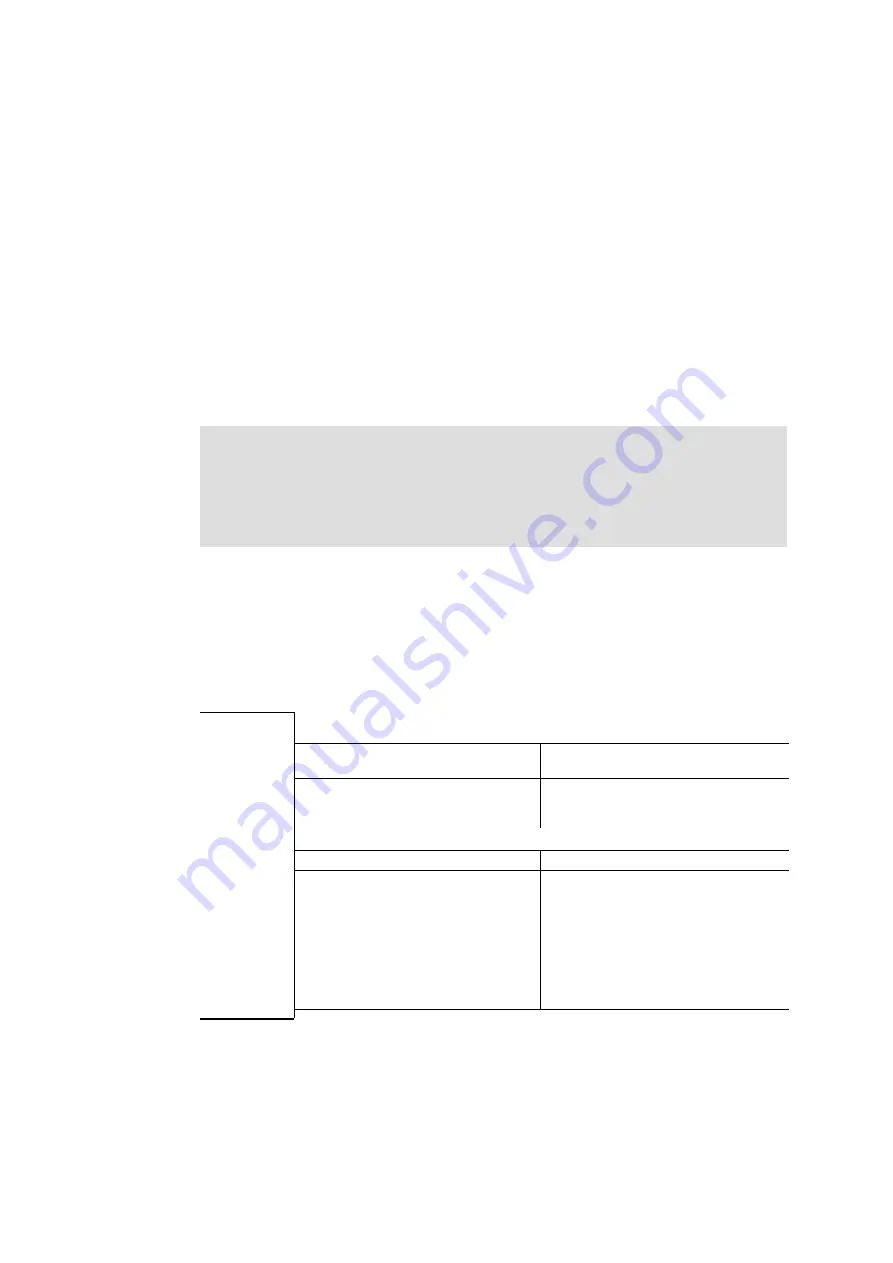
Maintenance/repair
j
| BA 14.0197 | 11/2010
40
7.2
Inspections
To ensure safe and trouble−free operation, spring−applied brakes must be checked and
maintained at regular intervals. Servicing can be made easier if good accessability of the
brakes is provided in the plant. This must be considered when installing the drives in the plant.
Primarily, the necessary maintenance intervals for industrial brakes result from the load during
operation. When calculating the maintenance interval, all causes for wear must be taken into
account (see chapter 7.1). For brakes with low loads such as holding brakes with emergency
stop, we recommend a regular inspection at a fixed time interval. To reduce the cost, the
inspection can be carried out along with other regular maintenance work in the plant if
necessary.
Stop!
Stable properties of the organic friction lining are only achieved in the case of
continuous use. The readiness for operation of the brake has to be ensured with
a braking energy that is equivalent to one emergency stop per week. Unplanned
emergency stops occurring at a sufficient frequency have the same effect.
If the brakes are not maintained, failures, production losses or damage to the system may
occur. Therefore, a maintenance concept adapted to the particular operating conditions and
brake loads must be defined for every application. For the INTORQ spring−applied brakes, the
maintenance intervals and maintenance operations listed in the below table must be provided.
The maintenance operations must be carried out as described in the detailed descriptions.
Type
Time interval
BFK464
−S/S
.1
for service brakes:
for holding brakes with emergency stop:
|
according to service life calculation
|
otherwise every six months
|
after 4000 operating hours at the latest
|
at least every two years
|
after 1 million cycles at the latest
Maintenance
Inspections with assembled brake:
Inspections after removing the brake:
|
Check release function and control (
|
Measure air gap (adjust, if necessary,
|
Measure rotor thickness (replace rotor, if
necessary,
|
Thermal damage of armature plate or flange
(dark−blue tarnishing)
|
Check clearance of the rotor gearing
(replace worn−out rotors,
|
Play of torque plate at sleeve bolts and
armature plate
|
Check springs for damage
|
Check armature plate and flange/end shield
– Evenness < 0.1 mm
– Max. run−in depth = rated air gap of brake
size