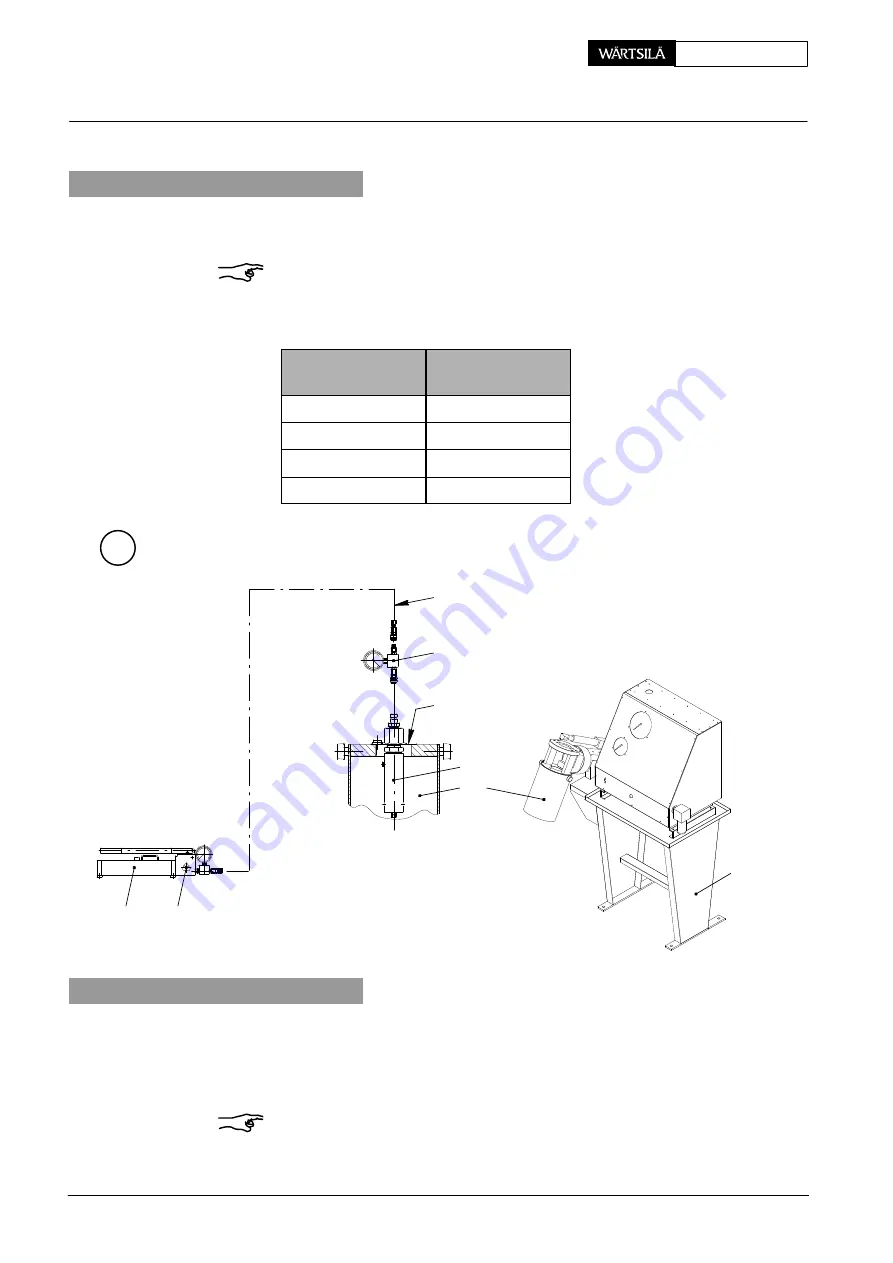
Maintenance
2745
−
1/A1
RT-flex58T-D
Winterthur Gas & Diesel Ltd.
2.
Checking blow-off pressure
For checking relief valve 2 use test bench 94272 and test & calibration fluid (see
specification in
) or a thin-bodied oil as test medium.
Remark:
Pay attention to the manufacturer’s detailed instructions and working
specifications of the test bench.
If necessary, a relief valve must be replaced completely and set according to the
following table:
Firing pressure
[bar]
Blow-off pressure
[bar]
156
−
160
225
166
−
169
235
174
−
175
245
176
−
180
250
B
013.484/05
013.486/05
94935
94934A
94272
94931
EV
017.670/08
10
94272C
2
3.
Fitting the relief valve
⇒
Apply Never-Seez NSBT-8 to the thread of relief valve 2 and fit it with new gas-
ket 7.
⇒
Always properly close indicator valve 3 so that no gas escapes and then
screw on its cap.
Remark:
If indicator valves leak for a long period the seats will become damaged.
Early replacement of a leaking indicator valve will allow easy repair. All threads and
internal parts must also be smeared with Never-Seez NSBT-8.
Relief Valve: Checking Blow-off Pressure
2013
Содержание WARTSILA RT-flex58T-D
Страница 8: ...Intentionally blank ...
Страница 10: ...Intentionally blank ...
Страница 12: ...Intentionally blank ...
Страница 14: ...Intentionally blank ...
Страница 20: ...Intentionally blank ...
Страница 32: ...Intentionally blank ...
Страница 58: ...Intentionally blank ...
Страница 66: ...Intentionally blank ...
Страница 72: ...Intentionally blank ...
Страница 84: ...Intentionally blank ...
Страница 88: ...Intentionally blank ...
Страница 92: ...Intentionally blank ...
Страница 120: ...Intentionally blank ...
Страница 122: ...Intentionally blank ...
Страница 124: ...Intentionally blank ...
Страница 132: ...Intentionally blank ...
Страница 136: ...Intentionally blank ...
Страница 148: ...Intentionally blank ...
Страница 152: ...Intentionally blank ...
Страница 156: ...Intentionally blank ...
Страница 168: ...Intentionally blank ...
Страница 176: ...Intentionally blank ...
Страница 186: ...Intentionally blank ...
Страница 192: ...Intentionally blank ...
Страница 196: ...Intentionally blank ...
Страница 200: ...Intentionally blank ...
Страница 214: ...Intentionally blank ...
Страница 234: ...Intentionally blank ...
Страница 238: ...Intentionally blank ...
Страница 242: ...Intentionally blank ...
Страница 256: ...Intentionally blank ...
Страница 264: ...Intentionally blank ...
Страница 272: ...Intentionally blank ...
Страница 280: ...Intentionally blank ...
Страница 282: ...Intentionally blank ...
Страница 290: ...Intentionally blank ...
Страница 296: ...Intentionally blank ...
Страница 300: ...Intentionally blank ...
Страница 312: ...Intentionally blank ...
Страница 314: ...Intentionally blank ...
Страница 318: ...Intentionally blank ...
Страница 334: ...Intentionally blank ...
Страница 340: ...Intentionally blank ...
Страница 348: ...Intentionally blank ...
Страница 352: ...Intentionally blank ...
Страница 356: ...Intentionally blank ...
Страница 358: ...Intentionally blank ...
Страница 362: ...Intentionally blank ...
Страница 366: ...Intentionally blank ...
Страница 370: ...Intentionally blank ...
Страница 380: ...Intentionally blank ...
Страница 384: ...Intentionally blank ...
Страница 386: ...Intentionally blank ...
Страница 392: ...Intentionally blank ...
Страница 402: ...Intentionally blank ...
Страница 412: ...Intentionally blank ...
Страница 414: ...Intentionally blank ...
Страница 438: ...Intentionally blank ...
Страница 440: ...Intentionally blank ...
Страница 444: ...Intentionally blank ...
Страница 454: ...Intentionally blank ...
Страница 498: ...Intentionally blank ...