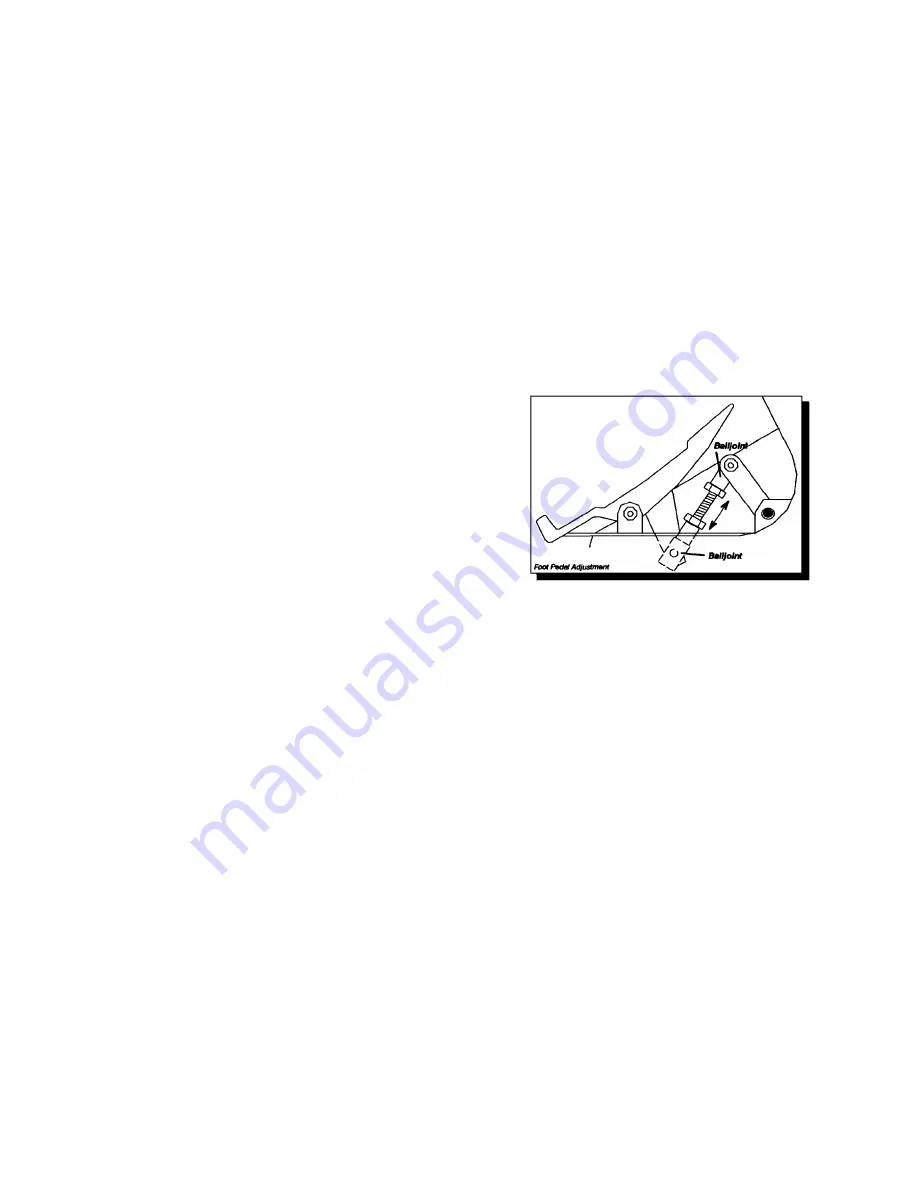
MAINTENANCE
QTFSG/QTFSD 98349 05/15/03
4-2
HYDRAULIC FILTER
The hydraulic filter keeps the machines hydraulic
system clean to a level of 10 microns. The hydraulic
fluid filter is located just inside the left rear frame.
The filter should be changed every 500 hours.
TO REPLACE FILTER ELEMENT:
1.
Stop the engine and set the parking brake.
2.
Open the seat support.
3.
Unthread and discard the hydraulic fluid filter
element.
4.
Apply a thin coat of hydraulic fluid to the seal of
the new hydraulic fluid filter element.
5.
Thread and hand tighten the new hydraulic fluid
filter element on the filter head.
6.
Close the seat support.
7.
Operate the machine and check for leaks.
Correct any leaks found.
8.
Check the hydraulic fluid reservoir level and fill
as required.
DIRECTIONAL CONTROL SYSTEM
(Refer to the Electrical Control Group
in the
Parts section)
The directional control system controls the direction
and speed of the machine. The system is made up
of the directional pedal, the throttle box, the
transistorized controller and contactors. The
controller, located in the electrical drive
compartment, is sealed and can only be serviced by
trained service personnel.
Do not use a pressure washer to clean the inside
of the electrical drive compartment.
When servicing machine, disconnect battery
connections before working on machine.
DIRECTIONAL CONTROL PEDAL ADJUSTMENT
(Refer to the Console Group in the Parts section)
The directional control pedal is designed to prevent
driver fatigue. However if a different pedal angle is
preferred, these directions should be followed.
1.
Raise rear cover.
2.
Disconnect batteries from machine.
3.
Locate and remove the directional control pedal
stop bolt.
4.
Locate the linkage rod beneath the directional
control pedal.
5.
Adjusting the length of the linkage rod controls
the pedal angle. Shortening the linkage rod
causes the pedal to have a flatter angle with the
floor. Lengthening the linkage rod causes the
pedal to have a steeper angle.
6.
To change the length of the linkage rod,
disconnect the upper end of the linkage rod from
the forward/reverse arm.
7.
Loosen the locking nuts on both ends of the
threaded portion of the linkage rod.
8.
Turning the balljoint changes the length of the
linkage rod, be sure that there is a minimum of
5/16” of threaded rod engaged in each of the
balljoints.
9.
When the new length is established, reconnect
the upper balljoint to the forward/reverse arm.
10.
Tighten the two locking nuts on the threaded
portion of the linkage rod.
11.
Reposition the directional foot pedal stop bolt.
12.
The stop bolt must be adjusted so that the
directional foot pedal comes in contact with the
stop while there is still a small amount of travel
remaining in the throttle arm. This is done to
prevent heavy foot pressure from damaging the
throttle unit.
THROTTLE “NEUTRAL POSITION”
ADJUSTMENT (Refer to the Console Group in
the Parts section)
The throttle is automatically returned to its neutral
position by a spring centering system. If the
machine tends to creep forward or reverse when the
operators foot is removed from the directional foot
pedal, the throttle “neutral position” may require
adjustment as described below:
1.
Turn off machine and set parking brake.
2.
Raise the rear cover.
3.
Disconnect the batteries from the machine.
4.
Remove the drive motor dust cover.
5.
Locate the throttle and spring centering
assembly.
6.
Disconnect the linkage rod from the throttle arm.
7.
With the throttle arm free, the throttle will return
to its neutral position using its internal centering
spring.
8.
Position the linkage rod balljoint over the hole in
the throttle arm. The balljoint should slide into
the hole without repositioning the throttle arm.
9.
If required, shorten or lengthen the linkage rod
until proper engagement occurs.
10.
Reattach linkage rod to the throttle arm.
11.
Install the drive motor dust cover.
12.
Connect batteries.
13.
Lower hopper.