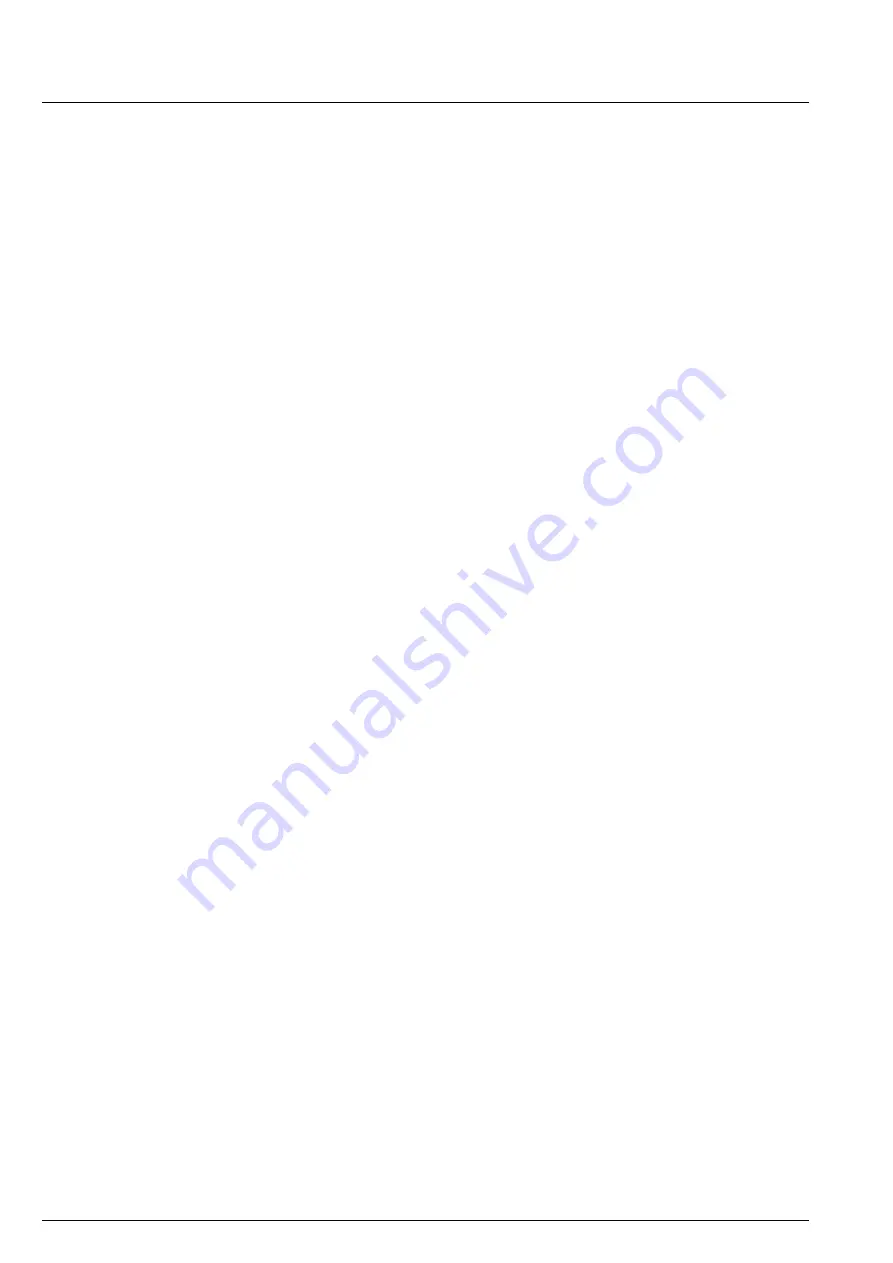
Maintenance
7-4
WILO EMU 3.0
- Visual inspection of accessories, e.g. the suspension device and hoisting gears
8,000 operating hours or after
two years
- Checking the insulation resistance
- Changing the lubricant in the cooling system and sealing chamber
- Emptying the leak chamber
- Functional inspection of all safety and control devices
- Coating check and touch-up as required
15,000 operating hours or af-
ter five years
- General overhaul
If it is used in highly abrasive or corrosive material, the maintenance
intervals should be reduced by 50%!
Maintenance tasks
Overview of the individual maintenance intervals:
Monitoring the current con-
sumption and voltage
The current consumption and voltage is to be monitored periodically during all 3 phases. This
remains constant during normal operation. Slight fluctuations are a result of the composition of the
pumped fluid. The current consumption can assist in early detection and correction of damage and/
or faulty operation in the impeller/propeller, bearings and/or the motor. More extensive resulting
damage can thus be largely prevented and the risk of a total failure can be reduced.
Checking the used relays for
posistors, sealing room moni-
tor, etc.
Check the relays used are functioning fault-free. Defective devices must be immediately replaced,
because these cannot ensure safe operation of the machine. The test procedure details should be
followed closely (in the operating instructions for each relay).
Checking the insulation resis-
tance
To check the insulation resistance, the power supply cable must be disconnected. The resistance
can then be measured with an insulation tester (measuring voltage = 1000V DC). The following val-
ues may not be exceeded:
The insulation resistance may not be below 20mega-ohms during initial operation. For all further
measurements the value must be greater than 2mega-ohms.
Insulation resistance too low: Moisture may have penetrated the cable and/or the motor.
Do not connect the machine, consult manufacturer.
Visual inspection of the power
supply cable
The power supply line must be examined for bubbles, cracks, scratches, chafed areas and/or
crushed sections. If damage is found, the power cable must be exchanged immediately.
The cables may only be changed by the manufacturer or an authorized/
certified service workshop. The machine may not be used again until the
damage has been adequately rectified.
Visual examination of the ca-
ble holders (carabiners) and
the cable bracing
When the machine is used in basins or pits, the lifting cables/cable holders (carabiners) and the
cable bracing are subject to constant wear. Regular inspections are necessary in order to prevent
the lifting cables/cable holders (carabiners) and/or cable bracing from wearing out and to prevent
the electricity cable from being damaged.
The lifting cables/cable holders (carabiners) and the cable bracing are to
be immediately replaced if any signs of wear appear.
Visual inspection of accesso-
ries
Inspect accessories such as suspension units and hoisting gear to check whether they are secured
in a stable manner. Loose and/or defective accessories should be repaired immediately or replaced.
Functional inspection of safe-
ty and control devices
Monitoring devices are temperature sensors in the motor, sealing room monitors, motor protection
relays, overvoltage relays, etc.
Motor protection and overvoltage relays and other trip elements can generally be triggered manu-
ally for test purposes.