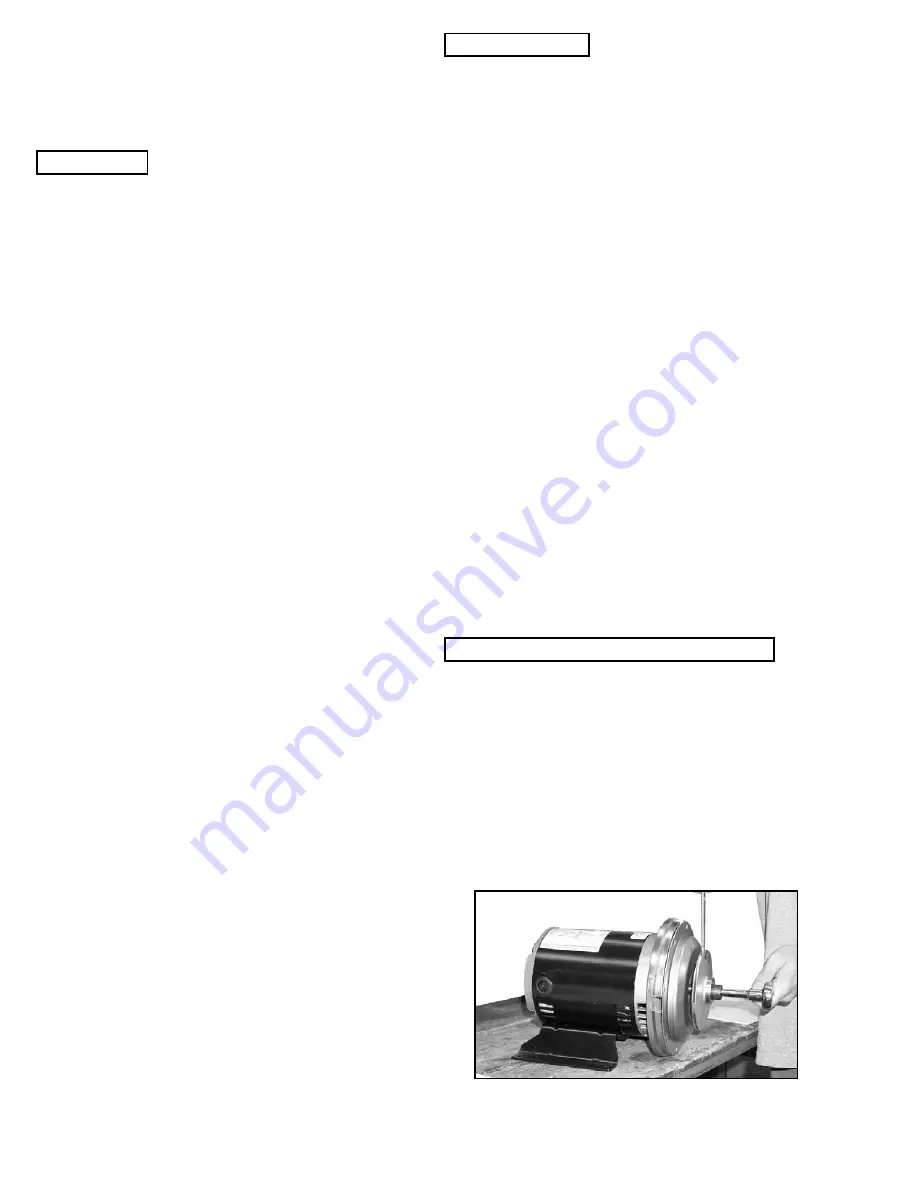
the discharge port.
2.
Long horizontal runs require a grade as even as pos-
sible. Avoid high spots and loops. Trapped air will
throttle flow and may result in erratic pumping.
3.
Install check and gate valves in discharge line; check
valve (if used) between pump and gate valve.
Pre-Start
— Before initial start of the pump, check as
follows:
1.
The rotation must be checked upon installation.
Close, then break the contacts quickly and observe
the rotation of the exposed portion of the rotating
parts. Rotation must agree with the rotation arrow on
the motor. For all pumps, the standard rotation is
counterclockwise when viewed from the suction
end. Motor wiring is easily changed in the field.
Observe the wiring diagram on the inside of the ter-
minal box cover, or on the motor nameplate.
2.
Check voltage, phase and frequency of line circuit
with motor nameplate.
3.
Check suction and discharge piping and pressure
gauges for proper operation.
4.
Assure that pump is full of liquid (primed).
Priming —
If pump is installed with a positive head on
the suction, prime by opening suction valve and allowing
liquid to enter the casing, at the same time venting all air
out of the top of the casing.
If pump is installed with a suction lift, priming must be
done by other methods, such as foot valves, ejectors, or
by manually filling casing and suction line.
CAUTION - DO NOT RUN PUMP DRY. Serious damage
may result if started dry.
Starting
— Proceed as follows to start pump:
1.
Close drain valves and valve in discharge line.
2.
Open fully all valves in the suction line.
3.
Prime the pump. If pump does not prime properly, or
loses prime during start-up, shut down and correct
condition before repeating procedure.
4.
For pumps moving high temperature liquids, open
warm-up valve to circulate liquid for preheating.
Close valve after pump has warmed up.
5.
Start the motor (pump).
6.
When pump is operating at full speed, open dis-
charge valve slowly.
Running
— Periodically inspect pump while running,
but especially after first start and following repair.
1.
Check pump and piping for leaks. Repair immediately.
2.
Record pressure gauge readings for future reference.
3.
Record voltage, amperage per phase, and kW (if an
indicating wattmeter is available).
4.
Adjust pump output capacity with discharge valve.
DO NOT throttle suction line.
Freezing Protection —
Protect pumps shut down
during freezing conditions by one of the following meth-
ods:
1.
Drain pump; remove all liquid from the casing.
2.
Keep fluid moving in pump and insulate or heat the
pump to prevent freezing. If heated, do not let tem-
perature go above 100 to 150 degrees F.
3.
Fill pump completely with antifreeze solution.
Cleaning —
Remove oil , dust, dirt, water, chemicals
from exterior or motor and pump. Keep motor air inlet
and outlet open. Blow out interior of open motors with
clean compressed air at low pressure. Regularly drain
moisture from TEFC motors.
Temperature —
Total temperature, not the rise, is the
measure of safe operation for a motor. If temperature by
thermometer exceeds limits for insulation class, investi-
gate and change operating conditions.
Labeled Motors —
It is imperative for repair of a
motor with Underwriters’ Laboratories label that original
clearances be held; that all plugs, screws, other hard-
ware be fastened securely, and that parts replacements
be exact duplicates or approved equals. Violation of any
of the above invalidates Underwriters’ label.
Lubrication —
Pumps should require no mainte-
nance, other than the motor bearings, according to the
following instructions:
DOUBLE SHIELDED. When double shielded prelubricat-
ed bearings are furnished, no lubrication is required for
the life of the bearings. Inspect bearings periodically to
determine the condition of the grease and replace the
bearings if necessary.
SINGLE SHIELDED W/GREASE FITTING PROVISIONS.
When single shield bearings are furnished, periodic
inspection, cleaning and relubrication is required. See
motor manufacturer’s specific instructions for
lubrication.
J56 FRAME MOTOR, PUMP NO. 230, 231, 232
A.)
Disassembly:
1.
Turn off power.
2.
Close suction and discharge valves.
3.
Drain pump.
4.
Remove bolts holding base to foundation
5.
Remove pipe connections from suction and dis-
charge.
6.
Remove pump from system.
7.
Remove case.
8.
Insert a screwdriver in one of the impeller water-
way passages and back off the impeller nut as
shown in Figure 1.
9.
Remove motor shaft end cap. Insert a screw-
driver in slot of motor shaft. While holding shaft
against rotation, unscrew impeller from shaft by
MECHANICAL SEAL REPLACEMENT
MAINTENANCE
OPERATION
Figure 1