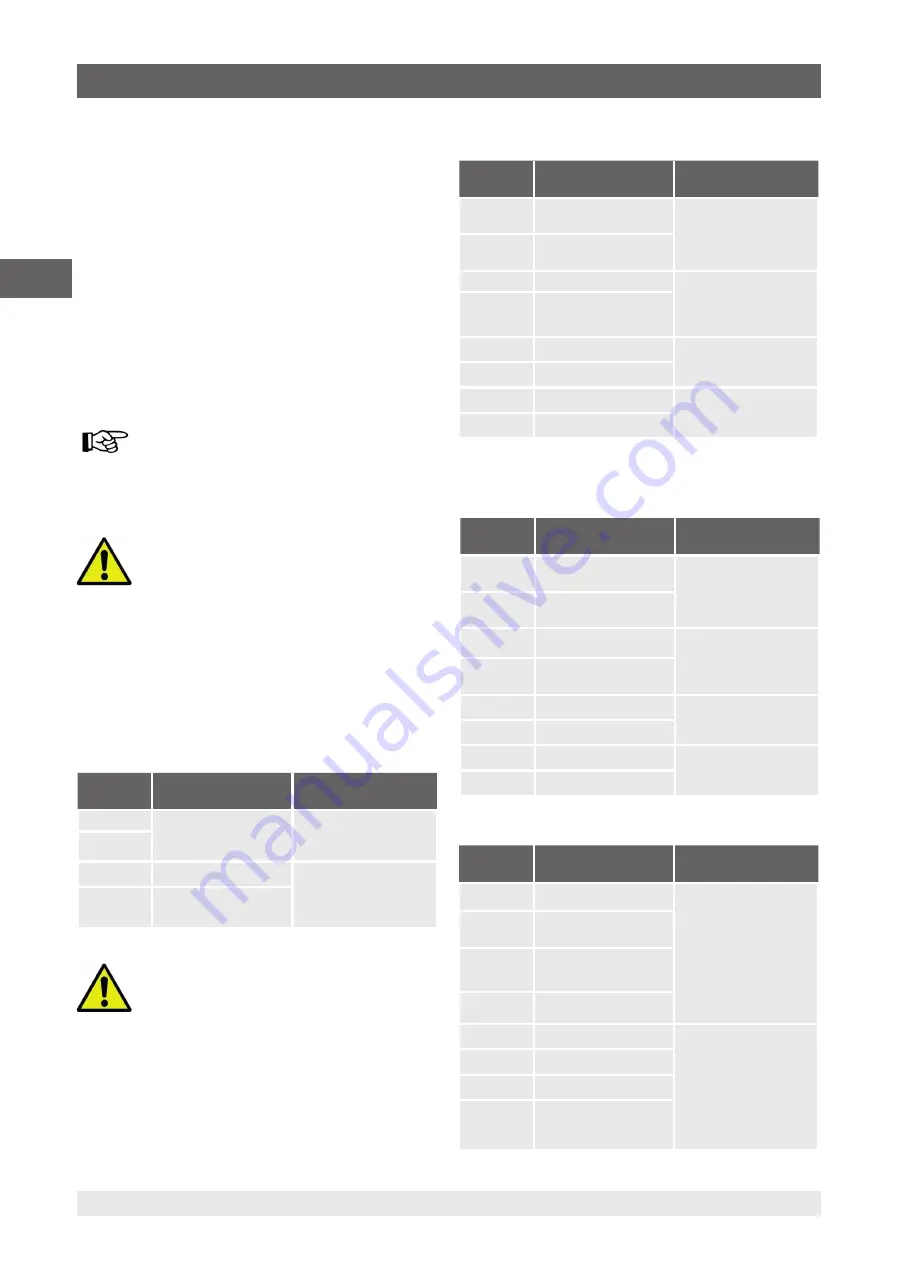
12
WIKA Operating Instructions - Ultrasonic Flowmeter FLC-UFL
81500908.01 08/2020 EN
EN
5. Installation
5.3 Wiring of the FLC-UFL series
This chapter provides information for correct wiring of the
FLC-UFL series flowmeter. The electronics enclosure is
provided with up to four cable gland entries with metric
(M20x1.5) or imperial (1/2” NPT) thread. Suitable shielded
cables must be used (for signal and communication cables
the use of twisted pair cables is recommended) whereby
the cables are protected from mechanical damages as
well as electrical interference. In addition, ensure length,
diameter, core are suitable for the length required in the field.
As a minimum 0.75 mm² core cross sectional area should
be used. All terminal connections use the Phoenix contact
MK3DSH series terminal blocks, suitable for wires with a
core cross sectional area up to 2.5 mm².
ATTENTION!
For a reliable connection always use insulated
wire end terminals compatible with the cable
core cross sectional area.
WARNING!
REFER TO CONTROL DRAWING 81500909
FOR THE INTRINSIC SAFETY PARAMETERS.
5.3.1 Determining installed option boards
In order to determine which option boards are installed
in your FLC-UFL series flowmeter, locate the FLC-UFL
Electronics model number on the nameplate of the SPU.
Using the table on the control drawing (drawing 81500909)
determine which option boards are installed.
5.3.2 Main board terminals
Signal
Function
Operating
parameters
PWR -
Power supply
Rated input voltage
12...29 VDC (After safety
barrier)
PWR +
D0_B
Frequency output -
0...5 kHz Passive open
drain, not electrically
isolated from system
ground
D0_A
Frequency
WARNING!
The power supply interfaces of the FLC-UFL
series flowmeter are reverse polarity protected
up to 250 mA max. Always connect via a suited
intrinsically safe isolator or barrier.
Refer to Control drawing 81500909 for detailed
information.
5.3.3 Slot 1, RS485 Option board terminals (01-0020)
5.3.4 Slot 1, RS485 IO 4..20 mA Option board terminals
(01-0202)
5.3.5 Slot 2, P/T Option board terminals (01-0022)
Signal
Function
Operating
parameters
PWR1 +
Option board power
supply
Power supply for the
I/O option board (10-29
VDC) (After safety
barrier)
PWR1 -
Option board power
supply
D1_B
RS485 B
Differential RS485 two
wire communications
port, galvanically
isolated
D1_A
RS485 A
D2_B
Digital output -
Passive, optically
isolated open collector
D2_A
Digital
D3_B
Digital output -
Passive, optically
isolated open collector
D3_A
Digital
Signal
Function
Operating
parameters
PWR1 +
4..20 mA Loop / power
supply
Power supply for the I/O
option board and the
4..20 mA loop. (10-29
VDC, after safety barrier)
PWR1 -
4..20 mA Loop / Loop
power supply
D1_B
RS485 B
Differential RS485 two
wire communications
port, galvanically
isolated
D1_A
RS485 A
D2_B
Digital output -
Passive, optically
isolated open collector
D2_A
Digital
D3_B
Digital output -
Passive, optically
isolated open collector
D3_A
Digital
Signal
Function
Operating
parameters
PRESS1
Connections to the
resistive bridge type
pressure sensor (factory
default = voltage mode
sensor). Refer to Safety
instructions for approved
pressure sensors, or
contact Euromisure for
more information
PRESS2
PRESS3
Signal -
PRESS4
Bridge -
TEMP1
Connections to the RTD
sensor (factory default
= 4 wire PT100). Refer
to Safety instructions
for approved pressure
sensors, or contact
Euromisure for more
information
TEMP2
TEMP3
Signal -
TEMP4
Supply -