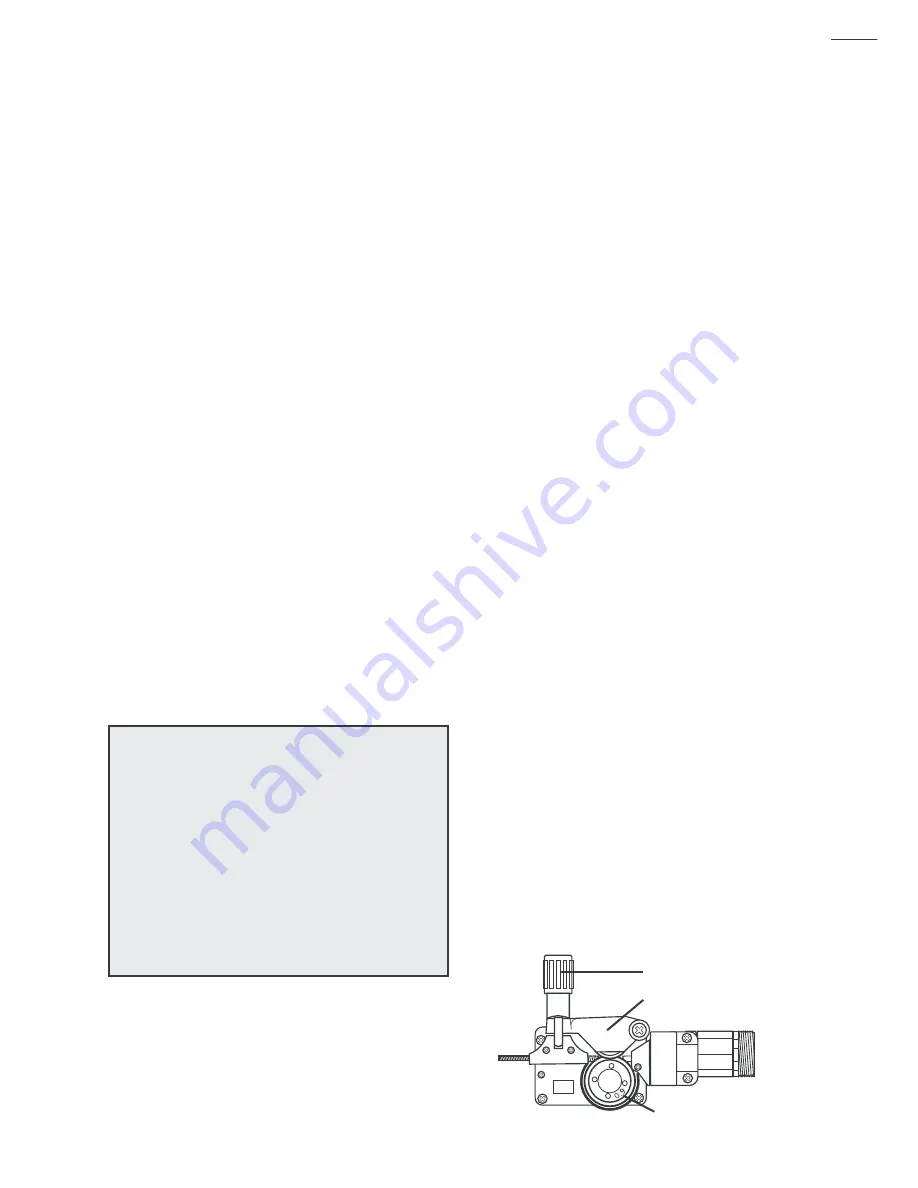
Quality
•
Reliability
•
Performance
Weldmatic 150
Model No CP121, Iss B 07/08
9
Quality
•
Reliability
•
Performance
The quality of the consumable wire
greatly affects how reliably a gas
metal arc welder will operate. For best
results when welding mild steel, we
recommend quality WIA AUSTMIG ES6.
Dirty, rusty or kinked wire will not feed
smoothly through the gun cable and
will cause erratic welding. Deposits from
the wire will clog the gun cable liner
requiring it to be replaced prematurely.
Fitting the gas cylinder
Place the gas cylinder on the tray at the
rear of the optional welder trolley (if using).
Retain the cylinder with the chain provided.
Fit the gas regulator to the cylinder. DO NOT
apply grease or oil to these joints.
Fit the end of the gas inlet hose from the
back of the power source to the connector
supplied with the gas regulator, and secure
with the clamp also supplied.
Fitting The Gun and Cable Assembly
The supplied gun/cable assembly is equipped
with a ‘Euro’ wirefeeder connector which
incorporates all required connection points
for welding current, shielding gas and gun
switch control.
To attach the gun/cable assembly to
the wirefeeder mechanism, engage the
mating parts of the male and female Euro
connectors, then rotate the locking ring
clockwise to firmly secure the connection.
Fitting the Consumable Wire
the adjustment of the spool adjuster, which
should be set to prevent over run of the wire
spool at the end of a weld, without unduly
loading the wirefeed motor.
1 kg Spools
Remove the adjustor knob, spring, washer
and 5 kg spool holder. Leave the 5 kg spool
holder in a safe place (ie inside the welder).
Fit the 1kg wire spool directly onto the spool
axle. Fit the washer, spring and adjustor knob
and tighten the adjustor knob fully.
Compression screw
Top roller arm
Groove size
Feeding the Consumable Wire
At the wirefeed assembly, release the
compression screw by swivelling it outwards.
This allows the top roller arm to spring to the
open position. The end of the welding wire
can now be passed through the inlet guide,
over the bottom driven roller, and into the
output wire guide tube. Check that the drive
roll groove is correct for the wire in use. The
appropriate size is stamped on the visible
side of the installed roller. Check also that
the correct size contact tip is fitted at the gun
end. Feed roller and tip details are shown in
Section 11 of this manual.
Return the top roller arm to the closed
position and adjust the compression screw to
provide sufficient clamping of the drive roll
to achieve constant wirefeed. Do not over
tighten.
With the equipment energised, operate the
gun switch to feed wire through the gun
cable.
5 kg Spools
Place the spool of welding wire onto the
spool holder. The location pin should mate
with a hole provided on the wire spool body.
Fit the spool retaining ‘R’ clip supplied. Check