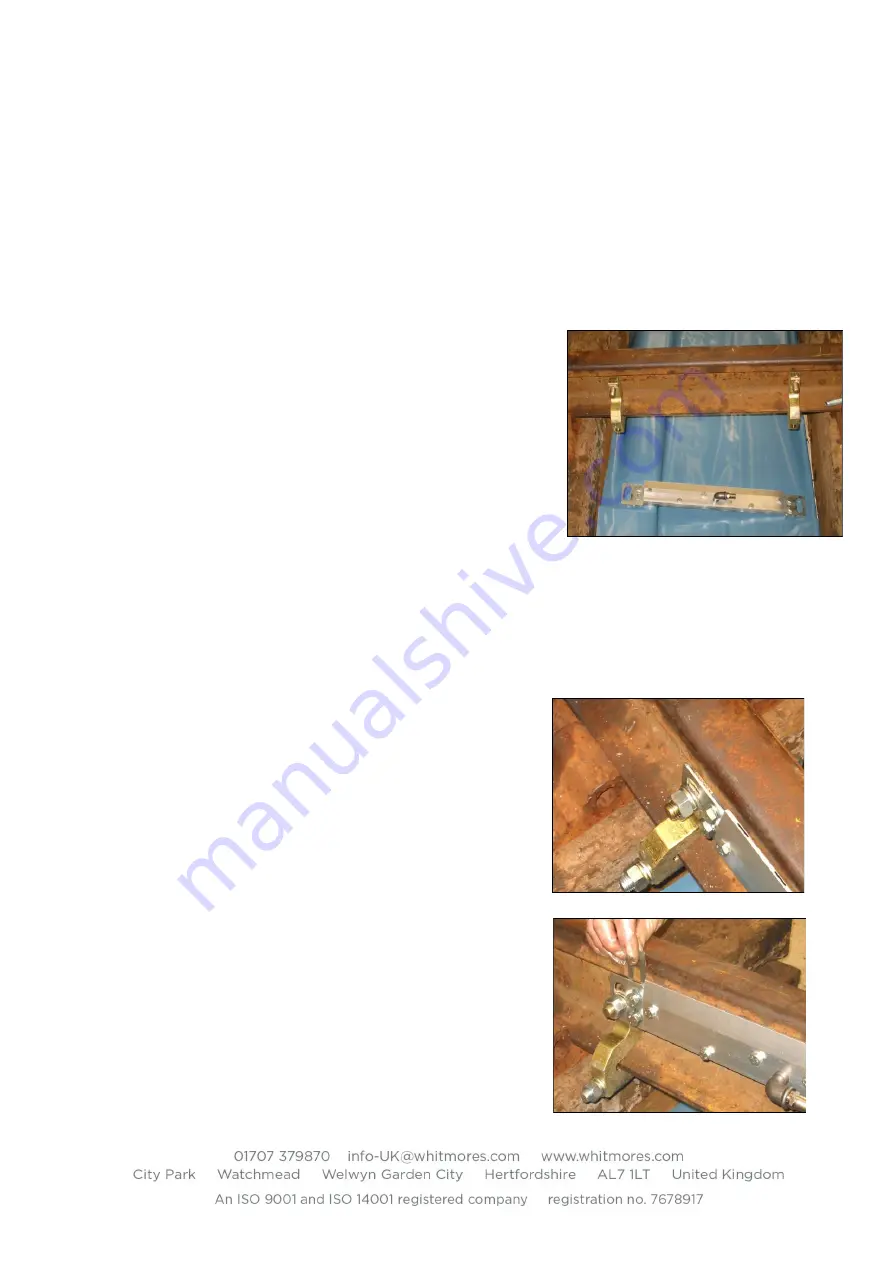
29
10.3
Blade System
The system allows use of a range of grease distribution units (blades):
Running Rail Blades
o
2 blades on high rail.
o
4 blades on the high rail and 4 blades on the low rail.
There are two styles of Blade available; standard (reference Section 10.4, 10.5 below) and EasiBlade.
Each is available in 40 or 60cm lengths.
10.4
Installing the Blade Rail Clamps (Standard Style)
10.4.1
Once the position of the Blade to be fitted has
been identified, lay the Blade unit adjacent to the
rail (on the “4 foot” side) in order to locate where
the Blade clamps need to be fitted.
10.4.2
Both Blade clamps can now be fitted (image on the
right).
10.4.3
The main part of the clamp is fitted on the “4 foot”
side of the rail with the threaded stud at the top
and facing away from the rail.
10.4.4
The hook bolt is then fitted under the rail with the hook clasping the foot of the rail on the
field side with the threaded part inserted through the hole at the base of the clamp.
10.4.5
The washers and nyloc nut are then to be fitted to the hook bolt and fastened tight.
10.4.6
Repeat for the second clamp.
10.5
Installing the Blades (Standard Style)
10.5.1
Fit the Blade onto the clamps using the M16 flat
washer, spring washer and nut onto each clamp
and secure. Hold the blade against the gauge
face of the rail, if there is a gap between the back
plate and the gauge face of the rail spacing shims
will need to be fitted.
10.5.2
To fit the spacing shims loosen the two M10
bolts that fit the Blade plates to the brackets.
Slip the number of shims needed behind the
plate and over the threads of the M10 bolts
between the bracket and the blade backplane.
10.5.3
Repeat for the other end of the blade if
necessary.
10.5.4
Once again fit the blade onto the clamps and
hold the blade against the gauge face of the rail.
10.5.5
If there is no gap, fit the M16 flat washer and
nyloc nut onto each clamp and tighten lightly so
the blade can still be moved.