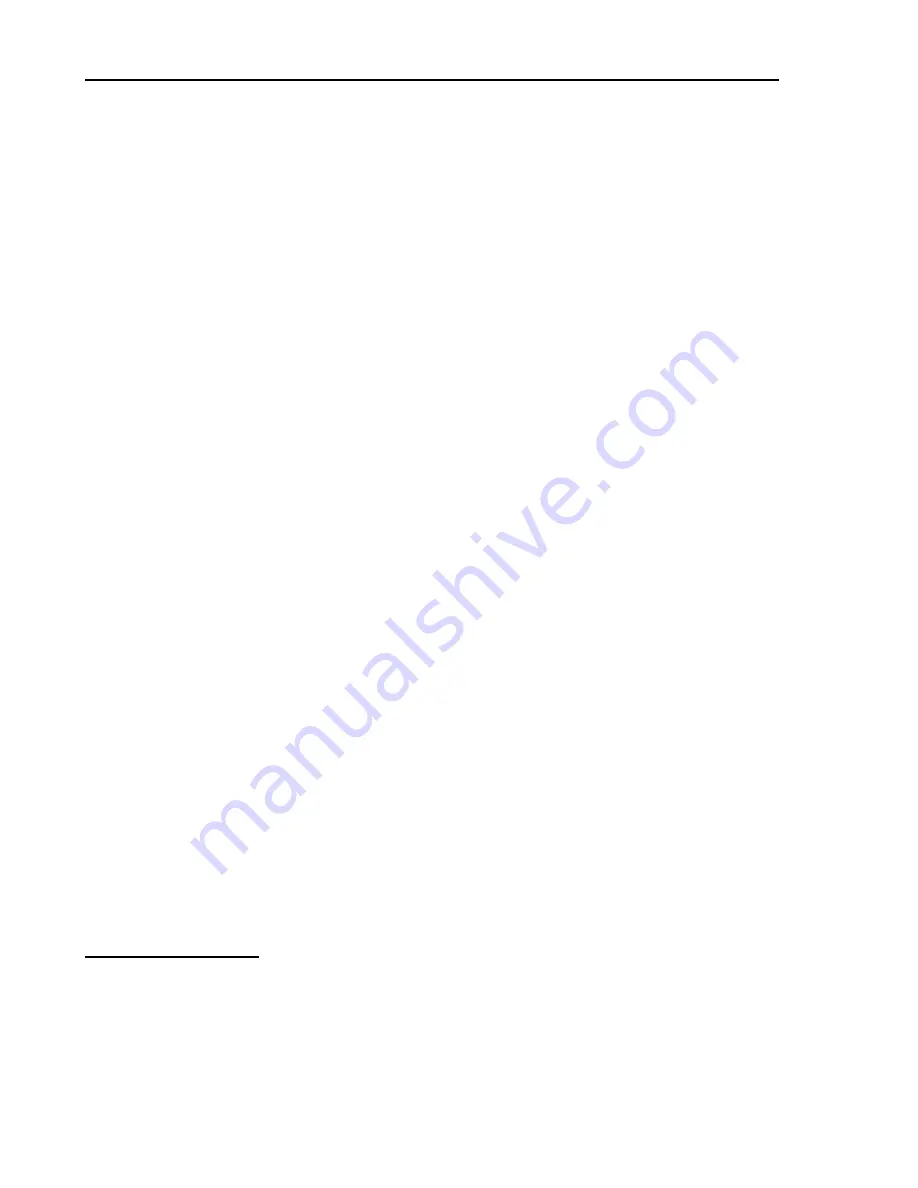
CUSTOMER ADVICE – BEFORE CALLING FOR ASSISTANCE
If the clothes are not dry after normal drying time:
–Check that you used the correct heat setting.
–Check that you have not set the timer within a cool down period.
–Check that the lint filter has been cleaned. A blocked filter will restrict the airflow.
–Check that your dryer is heating - below the door to the left side, should feel warm to the touch after the
first 10-15 minutes of its programme.
Failure to heat may indicate the safety cut-out has operated. To reset, simply press the red button at the
rear of the machine. If it has operated then a sharp “click” will be heard.
This cut-out only operates if the airflow is severely restricted so make sure the filter is clean, the air inlets
and outlets at the side and back are not blocked, and that all other restrictions are removed before re-
starting.
If the cut-out continues to operate after checking the above points, you should contact your service agent.
Check that the machine has the correct weight load in the drum before starting the appliance.
If your machine does not work check the following before calling a service engineer:-
- Check that there is a supply of electricity.
- Check that the door has been properly closed and the machine is switched on.
- Check the fuse in the moulded plug.
A call out charge will be applied for a service visit, if the call could have
been avoided by following these instructions.
If problems continue after checking the above points you should
contact our service agent
.
Please ensure that you have your serial number to hand when you make the call. To locate the
serial number on your dryer, open the door and look for a white label inside the door opening.
This will indicate the appliance identification code along with the serial number.
WHIRLPOOL 0800 988 1323
(calls are
FREE
from landlines however calls from
mobiles may be charged at your network provider’s rates )
or Service Network 2000
(Northern Ireland only)
028 90365222
(Daytime calls
cost up to 14p plus 8p per minute from BT lines Monday-Friday. Mobile and other providers’ charges
may vary).
Alternatively call
REPAIRCARE 08448797422
(Daytime calls cost up to 8p plus 6p per minute from BT lines Monday to Friday. Mobile and other
providers’ charges may vary).
OPTIONAL EXTRAS
Front to Extendible Rear Venting Kit
To convert your dryer from front venting to extendible rear venting.
Vent Hose
Only available for fixed rear dryers. Leads the warm, damp air to outside.
Wall/Window Vent Kit
- To make a permanent connection through a wall or window. Front venting
dryers need converting to rear venting before installing this kit (see ‘Front to Extendible Rear Venting
Kit’ above). This kit is not suitable for double glazed windows.
Содержание HX3 8DE
Страница 7: ......
Страница 8: ...Manufactured by Crosslee plc Hipperholme Halifax West Yorkshire HX3 8DE 4213 194 12652 ...