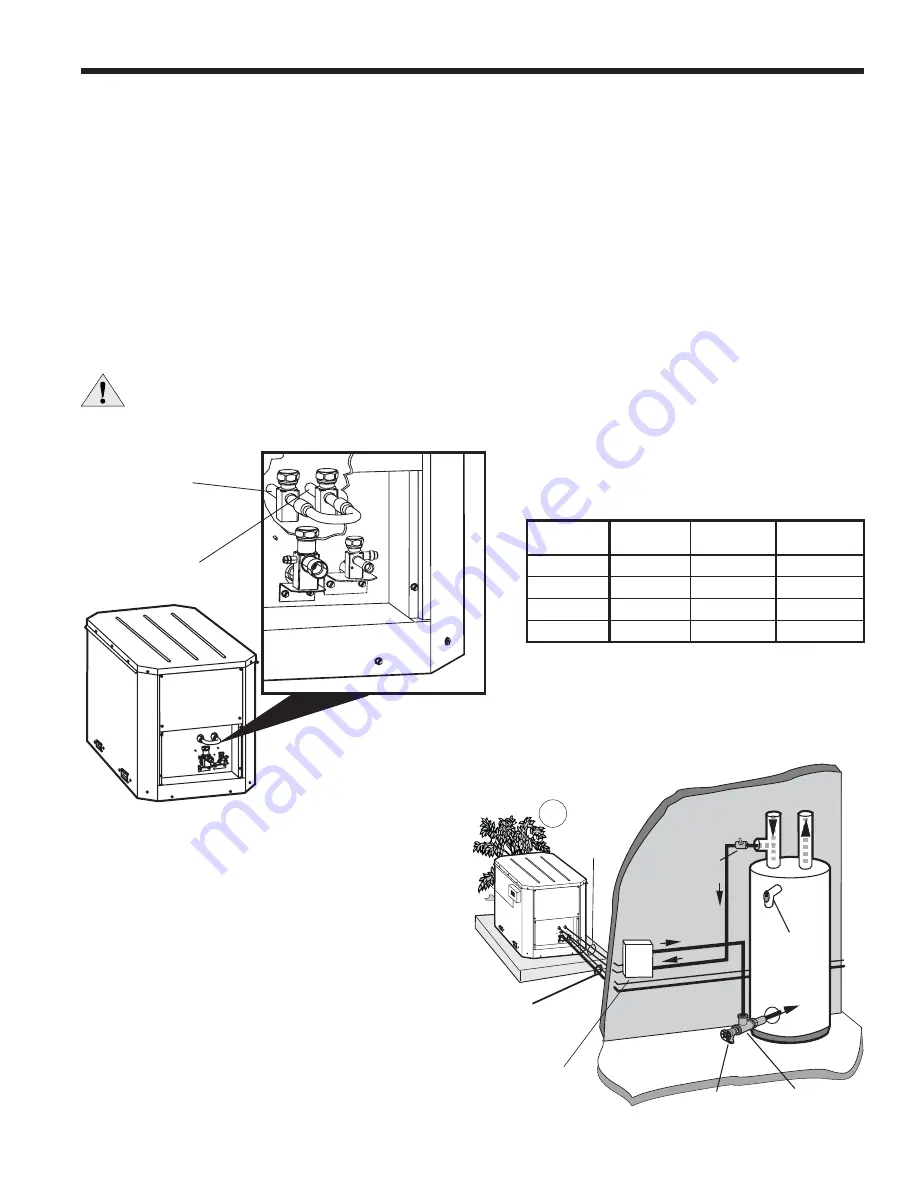
9
ES SPLIT INSTALLATION MANUAL
Service valves have been provided inside the unit for connecting the discharge gas line to a water heating heat recov-
ery unit (see fi gure 5). To make the connections, close the service valves inside the unit by turning clockwise. Using a
recovery canister connect to either of the schrader ports on the DSH service valves and recover the small amount of refrig-
erant trapped inside of the U-tube.
Prior to brazing ensure that all refrigerant has been removed from U-tube
. Once
the refrigerant is removed, it is recommended that the tube be cut at the “U” to remove any excess oil that may be trapped.
(This will also allow for easier removal of the tubing with a torch, since each section can be removed independently).
Ser-
vice valves must be protected to prevent overheating
. Unbraze the 1/2-inch O.D. U-tube and run tubing from the left
hand service valve to the inlet of the heat recovery unit and from the outlet of the heat recovery unit to the right hand of the
service valve. Typically the one way discharge line length should be limited to 25-30 feet and line size must be increased
depending on unit size and length of run. Follow the instructions supplied with the heat recovery unit for mounting location,
water piping, and start up. A typical installation is shown below.
IMPORTANT - Reopen discharge line service valves before starting up unit, but only after leak checking,
purging, and evacuating new discharge line.
To
Compressor
Heat Recovery
Unit “In”
From
Heat Recovery
Unit “Out” to
Reversing
Valve
Insulated Line set
With UV Paint
To Air handler
Add-on
Hot Water
Generator with
Internal Pump
Cold
Drain Valve
Pipe Tee
Hot
Venting
Waste Valve or
Vent Coupling
Line set
To Hot Water
Generator
P/T Relief
Valve
Figure 5: Service Valves for Heat Recovery Unit Connections
Figure 6: Typical Hot Water Piping Layout
SIZE
1/2” OD
5/8” OD
3/4” OD
024 - 036
Up to 9 ft.
Up to 25 ft.
Up to 30 ft.
048
Up to 5 ft.
Up to 13 ft.
Up to 30 ft.
060
N/A
Up to 9 ft.
Up to 25 ft.
072
N/A
Up to 6 ft.
Up to 20 ft.
Maximum One-Way Line Length
Heat Recovery Unit for Domestic Hot Water