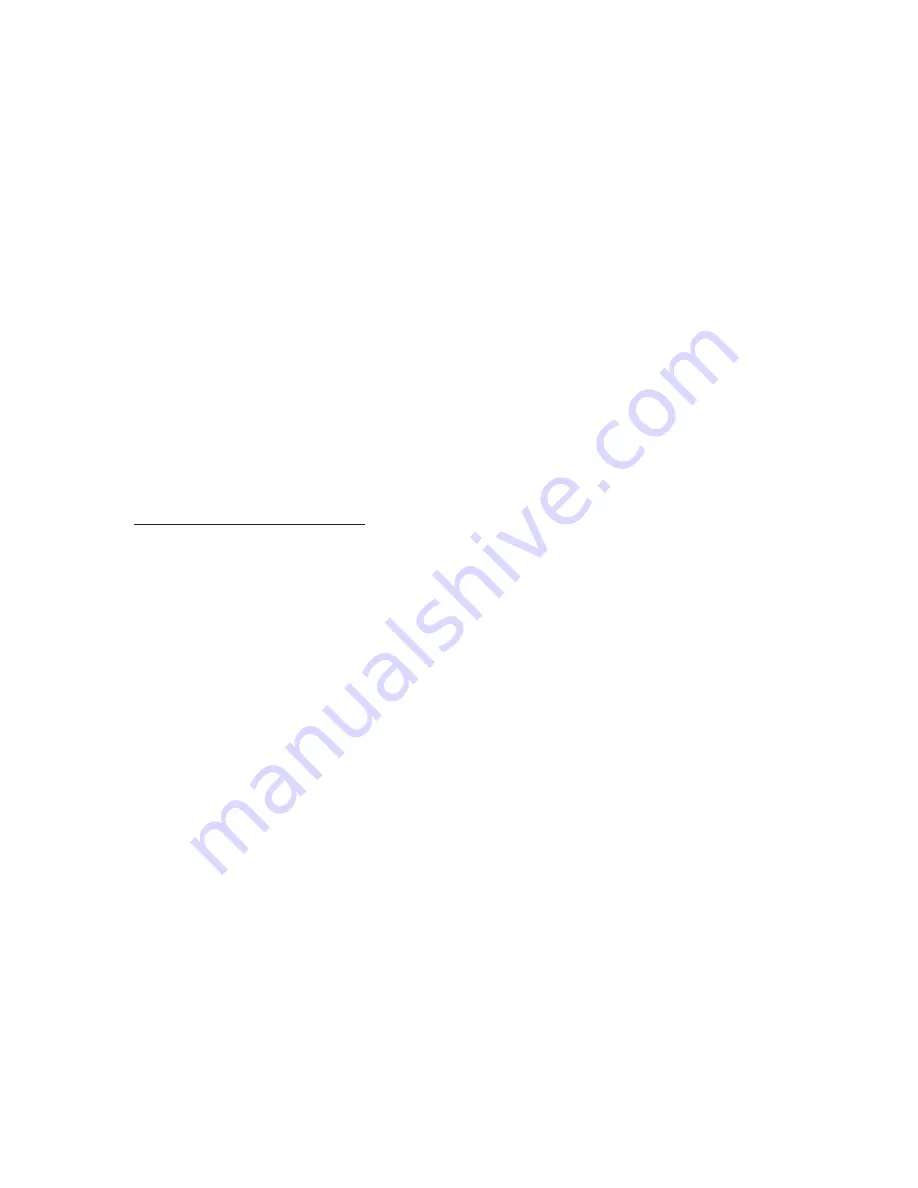
9
BLADES
Blades for this machine are furnished in 2/3, 4/6, and 8/12 teeth
per inch. 2/3 or 6/8 teeth per inch blades should be used when
solid stock are being cut. 8/12 blade should be used for cutting
tube bundles.
Special purpose blades are also available.
SPEED SELECTION
Saws are equipped with step pulleys, which provide a selection 80
FPM, 135 FPM and 210 FPM speeds.
Use the fast speed to cut thin-walled metal, tubing, thin channels,
aluminum, thin brass, or any metal that will not burn the teeth. Use
the medium speeds on general cutting, such as cold rolled, ma-
chine steels, heavy channels, etc. Use the slow speed for cutting
nickel steels or any metals which require a slow speed on a lathe.
Brass should always be cut with a blade which has not previously
cut other metal.
If teeth wear off unusually fast, use slower speed.
ALWAYS KEEP
THE BLADE TIGHT AND FLUSH AGAINST THE FLANGE OF
THE BAND WHEELS
(
See wheel pitch adjustment instruc-
tions, page XX
)
BELT
Proper adjustment of the “V” belt is important to prevent overheat-
ing of the motor. Be sure the belt guard is closed after changing
blade speeds.
PREVENTIVE MAINTENANCE
The proper performance and service life of every machine de-
pends on how well it is maintained. The following should become
a regular routine of operations.
Clean & Lubricate Exposed Surfaces
1. Wipe exposed surfaces free of dirty oil, chips and dirt.
2. Apply a thin coat of oil,
Symbol 2190TEP
, or equivalent to
machined surfaces.
Inspect Gear Case Lubricant Every 6,000 hours
1. De-energize circuit. Tag “OUT OF SERVICE”.
2. Remove gearcase cover.
3. Use
Texico Marfax ‘0’
on the gears.
4. Remove excess lubricant.
5. Reinstall
gearcase.
6. Remove safety tag. Energize circuit.
Inspect Hydraulic Oil Level
1. De-energize circuit. Tag “OUT OF SERVICE”.
WARNING: CUTTING HEAD SHALL BE AT LOWEST ETREM-
ITY WHEN INSPECTING OIL LEVEL
2. Locate site gauge on the hydraulic tank.
3. Inspect oil level. Proper oil level is 1” from top of tank.
4. Remove safety tag. Energize circuit.
Clean Coolant Reservoir
1. De-energize circuit. Tag “OUT OF SERVICE”.
2. Remove and clean chip pan.
3. Remove
coolant.
4. .Remove residue, sediment, and sludge from reservoir.
5. Clean coolant pump.
6. Reinstall chip pan.
7. Fill coolant reservoir to operating level.
8. Remove safety tag and energize circuit.
9. Return cooling systems to normal operation.
Inspect Flexible Hoses & Fittings
1. Inspect hoses for cracks, breaks and deterioration.
2. Inspect hoses for chafi ng or evidence of unusual wear
3. Inspect
fi ttings for tightness.
Inspect Drive Belt For Wear
1. De-energize circuit. Tag “OUT OF SERVICE”.
2. Remove covers for access to belt.
3. Inspect belt for deterioration.
4. Depress belt half-way between pulleys. Belt should depress
1/2” to 3/4”.
CAUTION: A BELT THAT IS TOO TIGHT WILL DAMAGE
BEARINGS
5. Remove safety tag. Energize circuit.
Provide Hydraulic Oil Sample For Analysis
1. De-energize circuit. Tag “OUT OF SERVICE”.
NOTE: CLEANLINESS OF TOOLS AND EQUIPMENT IS ES-
SENTIAL FOR PROVIDING TRUE SAMPLE
2. Operate machine 5-8 minutes to allow a true sample to be
drawn after liquid is mixed; stop machine.
3. Fill sample bottle from hydraulic reservoir.
4. Tag sample bottle to identify equipment, and location.
5. Deliver to oil/water laboratory.
6. Renew hydraulic oil when one or more of the following limits
is exceeded:
WATER: 0.001 %
SEDIMENT: 0.1 %
ACID TEST: Indicates Positive
Clean Oil Line Screen (
Part #100237-002
)
To clean hydraulic line oil screen, which is located at the base of
the machine between the lifting cylinders. Lower frame to remove
all pressure from hydraulic lines. The screen can then be removed
and cleaned by unscrewing the hex nut.
Clean, Inspect & Lubricate Wheel Ball Bearing
1. De-energize circuit. Tag “OUT OF SERVICE”.
2. Remove wheel covers.
3. Remove cutting blade.
4. Remove jamnut and hexnut.
5. Remove band Idler Wheel and Drive Wheel.
6. Remove ball bearing.
7. Clean ball bearing.
8. Clean Idler wheel and drive wheel hub.
9. Inspect ball bearing for rough turning and head discoloration.
10. Pack ball bearing with grease,
VV-G-632, Type B, Grade 2
.
11. Reinstall ball bearing.
12. Reinstall band idler wheel and drive wheel.
13. Reinstall hexnut and jamnut.
14. Repeat steps 4 through 13 for other wheel bearings.
15. Reinstall blade.
16. Reinstall wheel covers.
17. Remove safety tag. Energize circuit.
Содержание 1220G-72D
Страница 2: ...2 ...
Страница 3: ...3 ...
Страница 4: ...4 ...
Страница 6: ...6 ...
Страница 7: ...7 ...
Страница 12: ...12 1 2 3 4 5 7 8 9 6 10 11 12 13 14 15 14 16 17 8 6 5 19 Base Assembly Base Assembly ...
Страница 16: ...16 1 2 3 4 4 5 6 7 9 3 12 13 14 16 15 7 10 11 8 Frame Guards Frame Guards ...
Страница 18: ...18 ...
Страница 19: ...19 ...
Страница 30: ...30 ...
Страница 31: ...31 ...