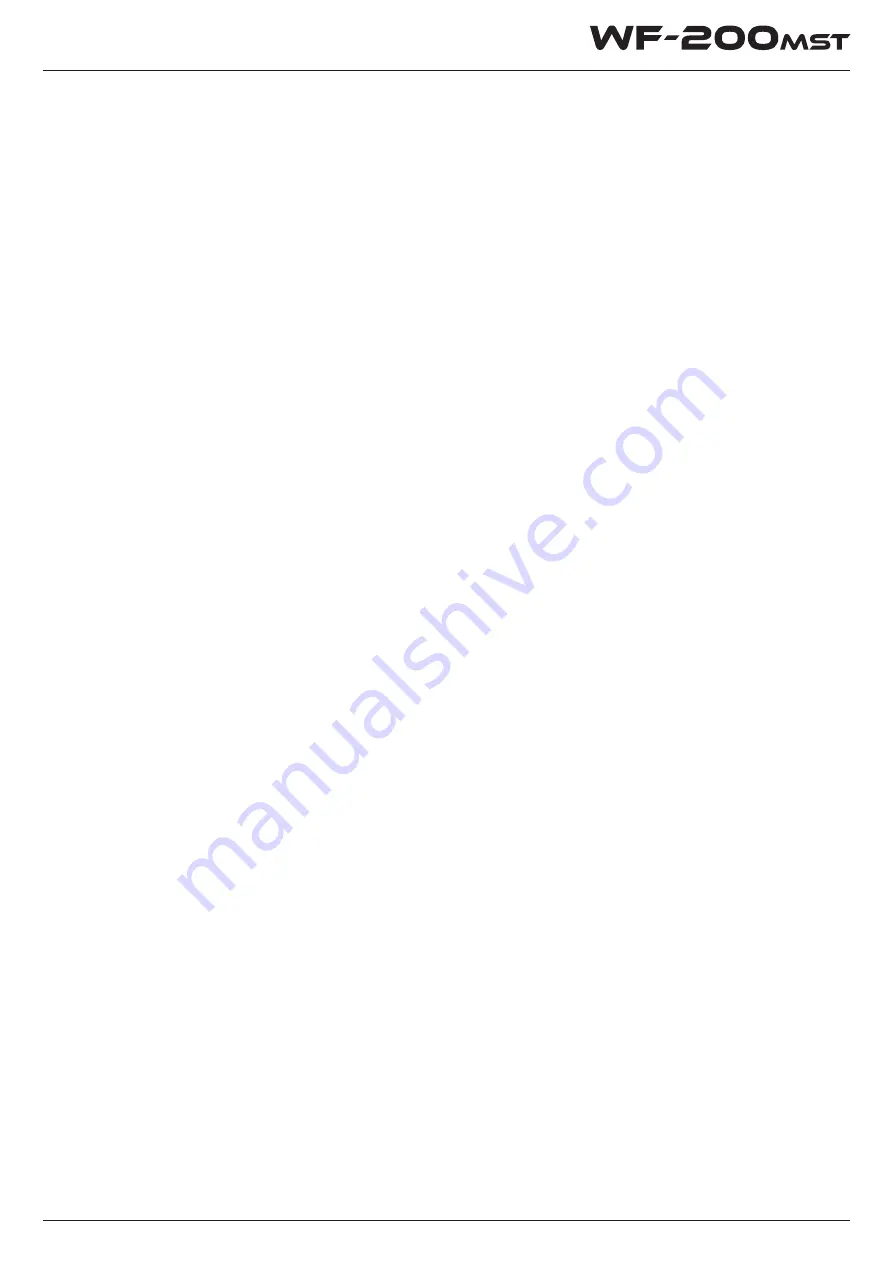
9
reduces the wire feeding friction and improves
the wire feed speed smoothness and consistency,
thus the welding quality is greatly improved. This
is especially so with ‘soft’ wires such as Aluminium.
It is difficult to get Aluminium to feed smoothly in
welding machines equipped with standard design
wire feeders, even with special torch liners and
short torch lengths.
The second advantage is that the gun can allow
the use of the small D100 wire spools at a distance
from the power source (This distance is only
limited by the length of the spool gun lead). This
is advantageous for high cost wire, that is not used
commonly such as Stainless Steel or MIG brazing
wire. It saves the outlay cost for a much more
expensive, larger D200 spool.
5.1 Connect the earth cable quick connector to
the negative welding power output socket
(13). Connect the earth clamp to the work
piece. Contact with the work piece must be
firm contact with clean, bare metal, with no
corrosion, paint or scale at the contact point.
5.2 Connect the MIG power connection lead (14)
to the positive welding power output socket
(12). Note if this connection is not made,
there will be no electrical connection to the
welding torch!
5.3 Connect the spool gun Euro Connector to
the MIG torch Euro connection socket (1) on
the front of the machine. Secure by firmly
hand tightening the threaded collar on the
MIG Torch connector clockwise. Connect
the spool gun interface plug to the spool
gun connection socket (2). Set the spool gun
switch (3) to ‘on’ position.
5.4 Connect the gas regulator to a gas cylinder
(not included with machine) and connect the
gas hose from the regulator to the gas inlet on
the rear of the machine (15). Ensure all hose
connections are tight. Open gas cylinder valve
and adjust regulator, flow should be between
10-25 l/min depending on application. Re-
check regulator flow pressure with torch
triggered as static gas flow setting may drop
once gas is flowing.
5.5 Set the welding voltage adjustment knob (8),
wire speed control knob (9) and inductance
control knob (10) to the desired positions.
You are now ready to weld!.
6. ARC/ MMA Welding Operation
6.1 Connect the earth cable quick connector to
the negative welding power output socket
(13) Connect the earth clamp to the work
piece. Contact with the work piece must be
firm contact with clean, bare metal, with no
corrosion, paint or scale at the contact point.
6.2 Insert an electrode into the electrode holder
and connect the electrode holder and work
lead to the positive welding power output
socket (12).
NOTE
:
This polarity connection configuration is valid
for most GP (General Purpose) MMA electrodes. There
are variances to this. If in doubt, check the electrode
specifications or consult the electrode manufacturer.
6.3 Connect the machine to suitable mains power
using the mains input power lead (16). Switch
the mains power switch (17) to ‘on’ to power
up the machine. Set the welding mode switch
(6) to ‘ARC’.
6.4 Select the required output current using the
current control knob (9). You are now ready to
weld!
7. Lift TIG Operation
NOTE
:
Lift TIG operation requires an optional valve
control TIG torch, argon gas cylinder & regulator
.
7.1 Connect the earth cable quick connector to
the positive welding power output socket
(12). Connect the earth clamp to the work
piece. Contact with the work piece must be
firm contact with clean, bare metal, with no
corrosion, paint or scale at the contact point.
7.2 Insert TIG torch power connection into the
negative welding power output socket
(13). Connect valve TIG torch gas line to the
regulator, ensuring all connections are tight.
7.3 Open gas cylinder valve and adjust regulator,
flow should be between 5-10 l/min depending
on application. Re-check regulator flow
pressure with torch valve open as static gas
flow setting may drop once gas is flowing.
7.4 Connect the machine to suitable mains power
using the mains input power lead (16). Switch
the mains power switch (17) to ‘on’ to power
Содержание WeldForce WF-200MST
Страница 24: ...by 24 MMA Stick Troubleshooting...
Страница 27: ...27 TIG Welding Troubleshooting...
Страница 34: ...by 34...
Страница 35: ...35...
Страница 36: ...by www Weldclass com au WF 200MST...