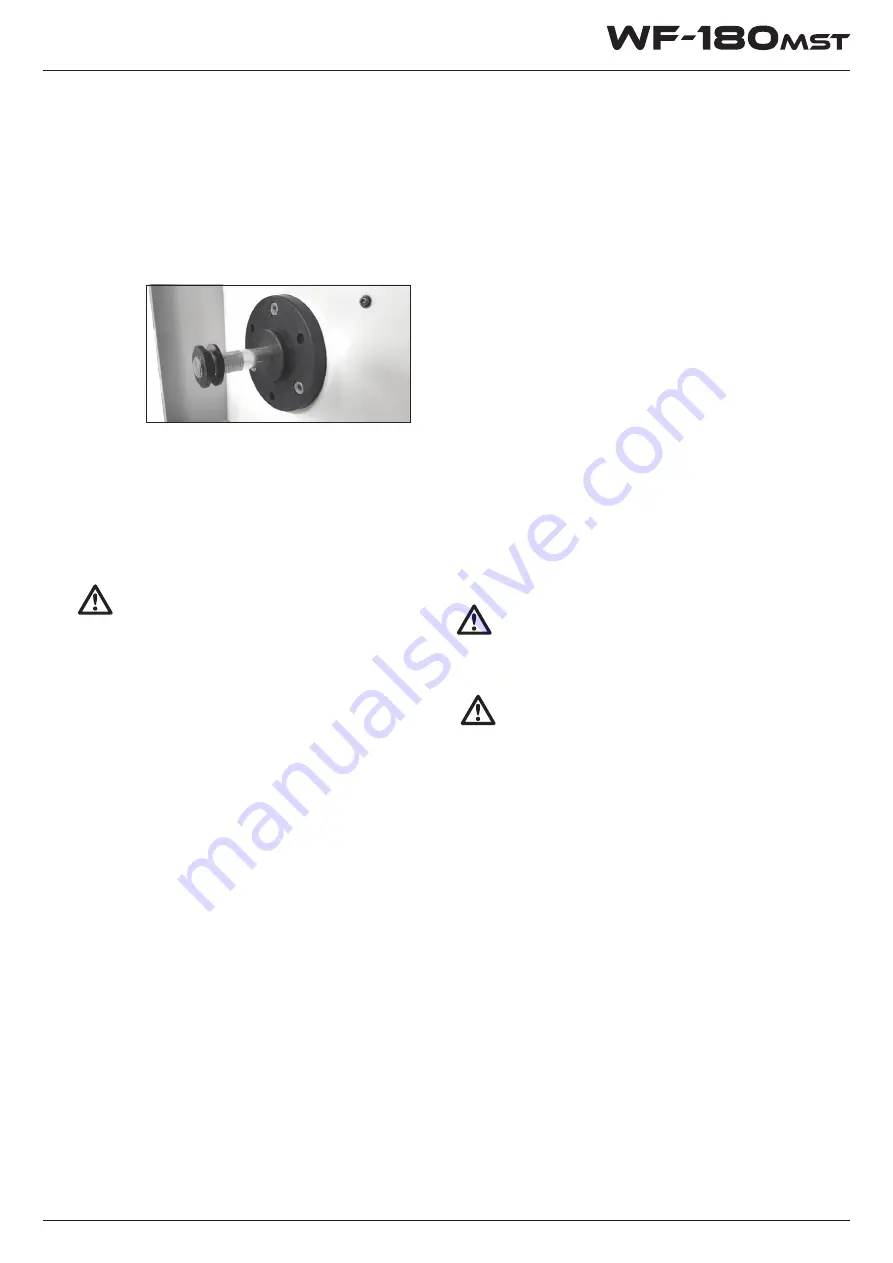
7
1. Fitting Wire Spool
1.1 Open wire feeder compartment door. Fit wire
spool to spool holder post. Ensure that
wire exits from the bottom of the spool.
100mm/1kg Spool Set Up:
Use plastic slotted washed/spacer and
threaded nut as shown here;
1.2 200mm/5kg spools only: Before replacing
spool retaining nut, set spool brake tension
by adjusting the smaller nut inside the spool
hub. Spool should be able to rotate freely,
but not continue to rotate when drive stops.
Tension may need to be adjusted as spool
weight decreases.
WARNING!
Excessive spool brake tension will cause wire
feeding issues and affect welding performance
as well as premature failure/ wear of wire feed
components.
1.3 Feed the wire from the spool through the wire
drive inlet guide (18) into the wire feeder.
2. Loading Wire Feeder
2.1 Release the wire feed tension arm (20) by
pivoting the wire feed tension adjustment
lever (19) towards you from the vertical
‘locked’ position.
2.2 Check the wire drive roller (22) groove
matches the selected MIG wire type and
size. The drive roller will have two different
sized grooves; the size of the groove in use
is stamped on the side of the drive roller. For
flux cored ‘soft’ wire, such as that used in
gasless MIG welding, the drive roller groove
has a serrated profile (known as knurled). For
solid core ‘hard’ MIG wire, the drive roller
groove used has a ‘v’ shaped profile. If
necessary, remove and change the drive roller
by rotating anti clockwise and removing the
drive roller retainer (21).
2.3 Once the correct drive roller (22) is selected
and fitted and the drive roller retainer (21) is
secured in place, manually feed the wire
through the wire drive inlet guide (18),
through the drive roller groove and into the
outlet wire guide tube. Ensuring that the wire
is correctly seated in the drive roller groove,
replace the wire feed tension arm (20) and
lock it into place by pivoting the wire feed
tension adjustment lever (19) back to the
vertical position.
3. Adjusting Wire Feed Tension
This is accomplished by winding the knob on the
tension adjustment lever (19). Clockwise will
increase tension, anti-clockwise will decrease drive
tension. Ideal tension is as little as possible, while
maintaining a consistent wire feed with no drive
roller slippage. Check all other causes of excess
wire feeding friction causing slippage first, such as;
incorrect/ worn drive roller, worn/ damaged torch
consumables, blocked/ damaged torch wire guide
liner, before increasing wire feed tension. There is a
number scale on the tension adjustment lever (19)
to indicate the adjustment position. The higher
the number indicated, the higher the tension that
is set.
WARNING!
Before changing the feed roller or wire spool,
ensure that the mains power is switched off.
WARNING!
The use of excessive feed tension will cause
rapid and premature wear of the drive roller, the
support bearing and the drive motor/gearbox.
3.4 Check that the correct matching MIG wire,
drive roller (22) and MIG torch tip are fitted.
3.5 Connect the machine to suitable mains power
using the mains input power lead (13). Switch
the mains power switch (14) to ‘on’ to power
up the machine. Set the welding mode switch
(7) to ‘MIG’ position.
3.6 You are now ready to feed the wire through
the torch. With the wire feeder cover open,
pull the trigger of the MIG torch to check that
the wire is feeding smoothly through the
feeder and into the torch.
3.7 Set the wire feeding speed knob (5) to
maximum. With the torch tip removed
from the torch and the torch laid out as
straight as possible, depress MIG torch trigger
until the wire feeds out through the end of
the MIG torch. Replace the tip on the MIG
torch and trim off any excess wire.
MIG Welding Operation
Содержание WeldForce WF-180MST
Страница 16: ...by 16 Other weld problems can be reduced by checking the following points...
Страница 23: ...23 MMA Stick Troubleshooting...
Страница 26: ...by 26 TIG Welding Troubleshooting...
Страница 32: ...by 32...
Страница 34: ...by 34...
Страница 35: ...35...
Страница 36: ...by www Weldclass com au WF 180MST...