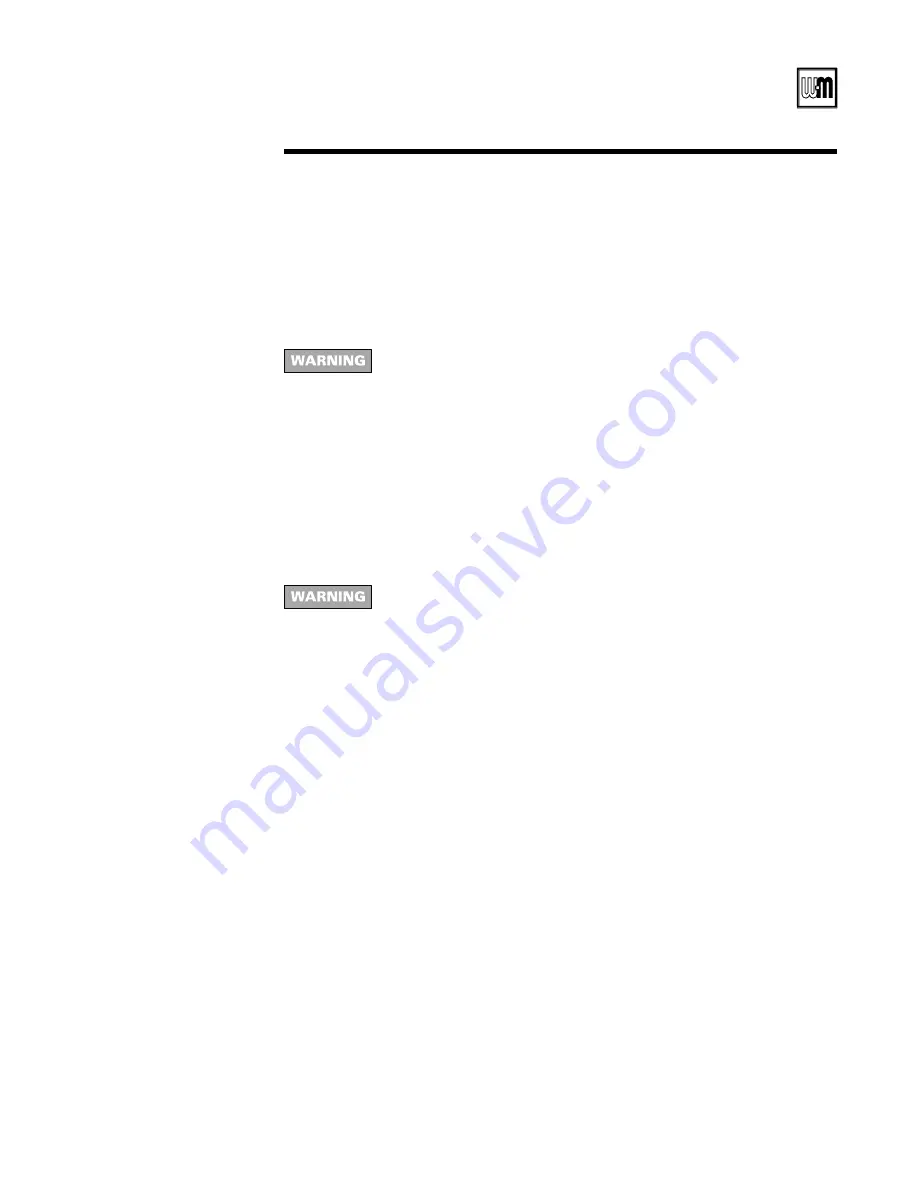
LGB
Gas-Fired Boiler — Boiler Manual
Part Number 550-141-186/0100
6
Chimney or Vent
When removing
boiler from common
venting system
Venting must be installed according to Part 7, Venting of Equipment, of National Fuel Gas
Code, ANSI Z223.1–latest edition and applicable building codes. Canadian installations must
comply with CAN/CGA B149.1 or B149.2 Installation Code.
Breeching must not be connected to any portion of mechanical draft system that can operate
under positive pressure.
At the time of removal of an existing boiler, the following steps shall be followed with each
appliance remaining connected to the common venting system placed in operation, while
the other appliances remaining connected to the common venting system are not in operation.
a. Seal any unused openings in the common venting system.
b. Visually inspect the venting system for proper size and horizontal pitch and determine
there is no blockage or restriction, leakage, corrosion and other deficiencies which could
cause an unsafe condition.
c. Insofar as is practical, close all building doors and windows and all doors between the
space in which the appliances remaining connected to the common venting system are
located and other spaces of the building. Turn on clothes dryers and any appliance not
connected to the common venting system. Turn on any exhaust fans, such as range hoods
and bathroom exhausts, so they will operate at maximum speed. Do not operate a summer
exhaust fan. Close fireplace dampers.
d. Place in operation the appliance being inspected. Follow the lighting instructions. Adjust
thermostat so appliance will operate continuously.
e. Test for spillage at the draft hood relief opening after 5 minutes of main burner operation.
Use the flame of a match or candle.
f.
After it has been determined that each appliance remaining connected to the common
venting system properly vents when tested as outlined above, return doors, windows,
exhaust fans, fireplace dampers, and any other gas-burning appliance to their previous
conditions of use.
g. Any improper operation of the common venting system should be corrected so the
installation conforms to the National Fuel Gas Code, ANSI Z223.1–latest edition. When
resizing any portion of the common venting system, the common venting system should
be resized to approach the minimum size as determined using the appropriate tables in
Appendix G in the National Fuel Gas Code ANSI Z223.1–latest edition.
Canadian installations must comply to CAN/CGA B149.1 or B149.2 Installation Codes.
Flue gas spillage
1b
Pre-installation
venting
See
Figures 3, 4 and 5
on page 7 for typical venting configurations. Ensure that your installation
complies with the requirements given in these illustrations and with all local codes and
standards.
See the
Ratings table
on page 36, for minimum breeching diameter. Use heavy gauge steel
breeching (Type B vent material or single wall metal pipe). Where horizontal breeching is
used, slope upward at least ¼" per foot toward chimney or vent and support with hangers to
prevent sagging.
Long horizontal breechings, excessive numbers of elbows or tees, or other
obstructions restricting flow of combustion gases can result in possibility
of flue gas spillage and carbon monoxide emissions, causing severe
personal injury or death.
Failure to follow all instructions listed below can cause flue spillage and
carbon monoxide emissions, resulting in severe personal injury, death or
substantial property damage.