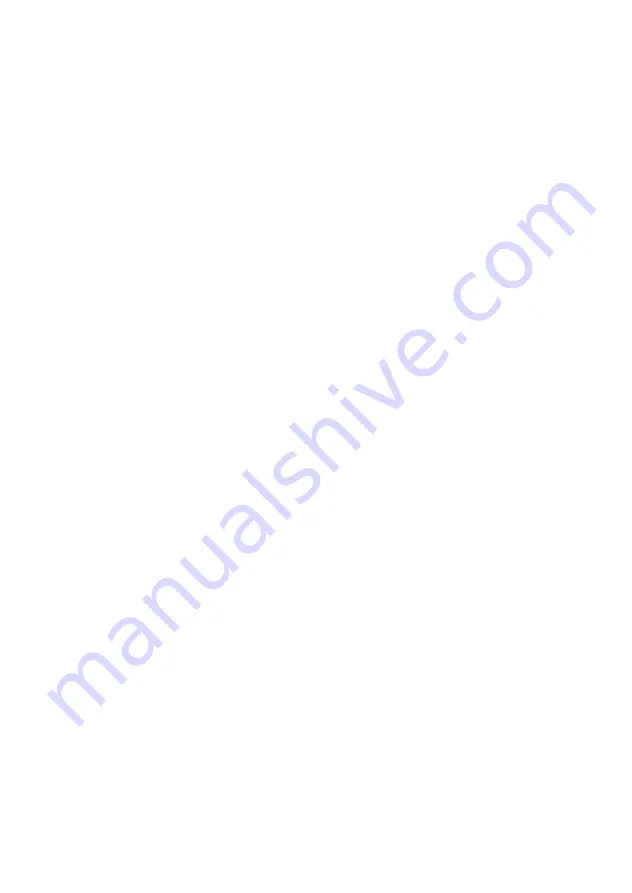
9
5.1
Cylinder Test (See Drawing B.1)
5.11
If the cylinder is slow in operation or cylinder ‘creeps’ under load the following
test should be carried out to check the cylinder seals.
Install the flow meter ‘in line’ as shown in Drawing B.1. Actuate cylinder to raise
and lower the load. Note flow and pressure readings, also note the time taken
by the cylinder to reach full stroke. Compare all readings with manufacturer’s
recommended figures. If flow is correct but time to extend cylinder is greater
than expected leakage across the cylinder seals is indicated. If flow is lower
than expected, investigate control valve function. See Test 5.0.
5.2 Motor Test
5.21 Motor performance is checked by measuring the flow and comparing it to the
equivalent motor speed. Install the tester or remote flow block in the line
upstream of the motor as indicated in the drawing B.1. Fully open the loading
valve and operate the directional control valve ensuring the motor rotates in the
correct direction. Allow motor to run under normal load. Note flow and pressure
readings. If flow is below manufacturer’s data sheet or lower than pump test
(3.0) investigate control valve function. See Test (5.0).
NOTE
: The motor may only be tested in reverse if it has an external drain. Do
not pressurise the outlet port of the motor without first checking the allowable
back pressure with the manufacturer.
Motor Leakage
5.22 Measure hydraulic motor r.p.m. with tachometer when motor is working at
normal pressure. If the motor speed is low and the inlet flow in 5.21 is found to
be correct, internal leakage in the motor is indicated. Check the motor leakage
by installing the remote flow block in the motor case drain. Note: most motors
not fitted with high pressure shaft seals have a maximum case drain pressure
of 1 bar (15 psi)
5.23 When the motor does not have an external drain or the motor cannot be back
pressure loaded connect tester in the other line and repeat the test 5.21 and
5.22 for the other motor direction.
5.3
Alternative Cylinder and Motor Test
5.31 Both motors and cylinders may also be tested as shown in drawing B.2.
Disconnect the two lines from the motor and connect the tester into these lines.
Fully open the loading valve, start the pump and bias the directional valve to
allow flow to the inlet port of the tester. Slowly close the loading valve by turning
clockwise and note the flow and pressure. If the flow is below the
manufacturer’s data or lower than the pump flow test (3.0) investigate the
control valve function. See Test (5.0). If the flow is correct and the speed is slow
this indicates a defective motor or cylinder.
Operate the directional valve to reverse the flow through the tester and record
the flow throughout the pressure range.