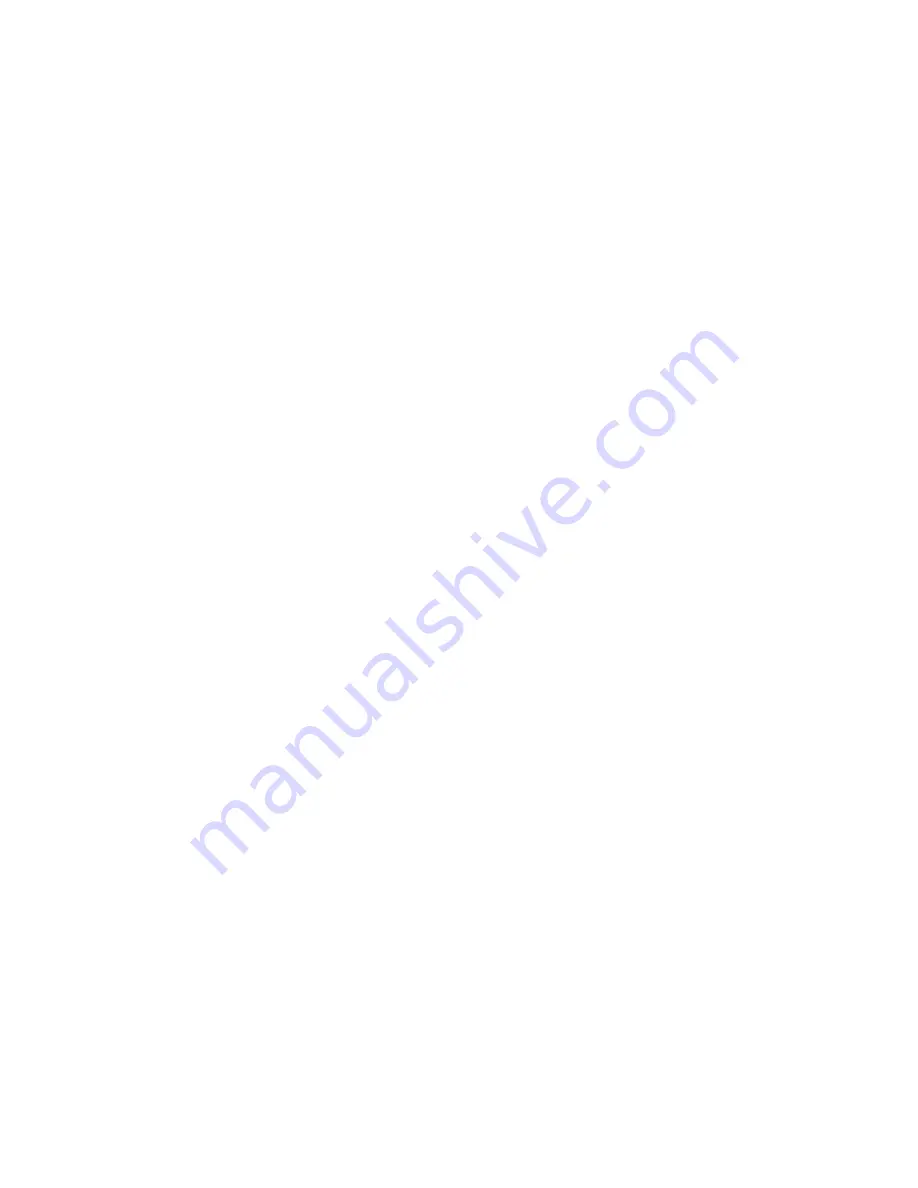
Burners equipped with Posi-Control can be adjusted for
individual air and FGR settings on both fuels and can easily
handle these variations, even with lower NOx levels. Link-
age burners operating at 30 ppm NOx (natural gas) are
equipped with a potentiometer in the control panel that will
allow the shut-off valve to partially open and allows a small
amount of FGR to flow when firing oil. This keeps the oil
inputs close to the gas input (lower FGR rates increase the
combustion air rate). The oil combustion is generally better
when FGR is used at low rates resulting in a lower NOx
level. Linkage systems with NOx levels under 30 ppm can
also use a multiple setpoint modulation motor to provide
separate gas and oil low fire and high fire positions.
Linkage dual fuel units may also be equipped with the
optional multiple set point (Siemens) modulation motor in
addition to the above potentiometer. This motor allows for
different low and high fire settings on gas vs oil to obtain
the correct airflow for each fuel and optimize the turndown
on gas.
The quantity of recirculated flue gas can be adjusted with
the inlet tube on the FGR line. To reduce the quantity of
FGR, push the tube into the FGR line (loosen the two set
screws to adjust the position of the tube, and tighten when
done). Moving the tube into the air stream will increase the
quantity of FGR. An access cover is provided opposite the
FGR line for this adjustment.
On a dual fuel unit, the natural gas should be done first to
properly set the FGR inlet tube. Once gas is setup, oil can
be set.
For dual fuel linkage systems, the following guidelines
should be used:
• A 60 ppm system can be adjusted with the same FGR
rate on both fuels. The FGR control valve is set on gas
and oil follows that setting.
• A 30 ppm system uses the FGR limiting potentiometer
(located in the control panel) to obtain a partial flow of
FGR when firing oil. The FGR control valve is set when
firing gas. The FGR limiting potentiometer is adjusted to
improve combustion but not cause instability. The
combustion needs to be checked at several firing rates.
• Under 30 ppm, separate gas and oil operating points are
established in the modulating motor.
Parallel positioning
(linkageless) systems allow all of the valves to be
positioned independently for each fuel. For this reason,
the setup sequence can be more flexible.
5. Burner Drawer Adjustments
The burner drawer has several adjustments built into the
design that allow the combustion to be tuned during
operation. While this can simplify the combustion tuning
process, care must be used to retain the relative position of
other components during this sequence. If these
adjustments are required, follow the sequence listed to
perform the adjustments.
Before any adjustments are made, the position of each
component must be marked. A felt tip pen or a combination
of masking tape and another type of pen can be used.
• Mark the distance of the oil gun tube from the drawer.
• Mark the distance of the scanner to the drawer
(See Figure E-1).
• Mark the distance of the gas pilot line to the drawer.
a.
To adjust the diffuser to gas spud dimension:
• On units with 12” or 14” heads (J and K heads
respectively), first mark the existing position of the
clamp bolt on each side of the head extension to
establish a baseline.
• Loosen the two clamp bolts on each side of the
head extension & scanner setscrews on the rear
drawer assembly cover.
• Move scanner forward or back first, then move the
diffuser the same distance and direction to keep the
same relative position between the two.
• Retighten diffuser clamp bolts/scanner set screws.
• Adjust Pilot & oil gun (if equipped) to match the
diffuser position change.
• On units with 16” heads or larger (L, M & N heads)
the procedure is the same except the diffuser is
locked into position with setscrews on the central
tube protruding from the drawer assembly.
b.
To adjust the oil nozzle to diffuser position:
• Loosen the two setscrews locking the oil gun lines
to the drawer.
• Adjust the oil nozzle to obtain the best combustion.
• Watch for spray back on the diffuser when the gun
is pulled too far back. The flame may appear good
but carbon will quickly develop on the diffuser.
• Tighten the two setscrews on the oil tubes locking it
into position.
c. If the burner drawer needs to be removed for
servicing or better access to components, perform
the following steps:
• Disconnect the scanner by screwing it off of the
scanner tube. In some cases, the scanner simply
pulls out with a spring tension. Secure the scanner
so that it is protected from shock.
• Disconnect the gas pilot line. Move the pilot line so
the drawer can be pulled out without interference.
• If equipped with oil, disconnect the oil lines, and
move them out of the way to pull out the drawer.
• Disconnect the ignition cable from the transformer.
It is attached with a thumb screw nut.
• Loosen and remove the screws securing the
drawer assy backplate to the blower housing.
• On Units with 12” & 14” heads, the drawer may
now be pulled back until all tubes clear the blower
housing. On units with 16” and larger heads it is
necessary to remove the side access cover on the
head extension and loosen the set screws securing
the center hub of the diffuser to the central drawer
assembly tube before withdrawing drawer
assembly from the blower housing.
To re-install the burner drawer, simply work the
procedure in reverse.
Page 42
Section F - Startup and Operating Instructions
JBE(X) Manual