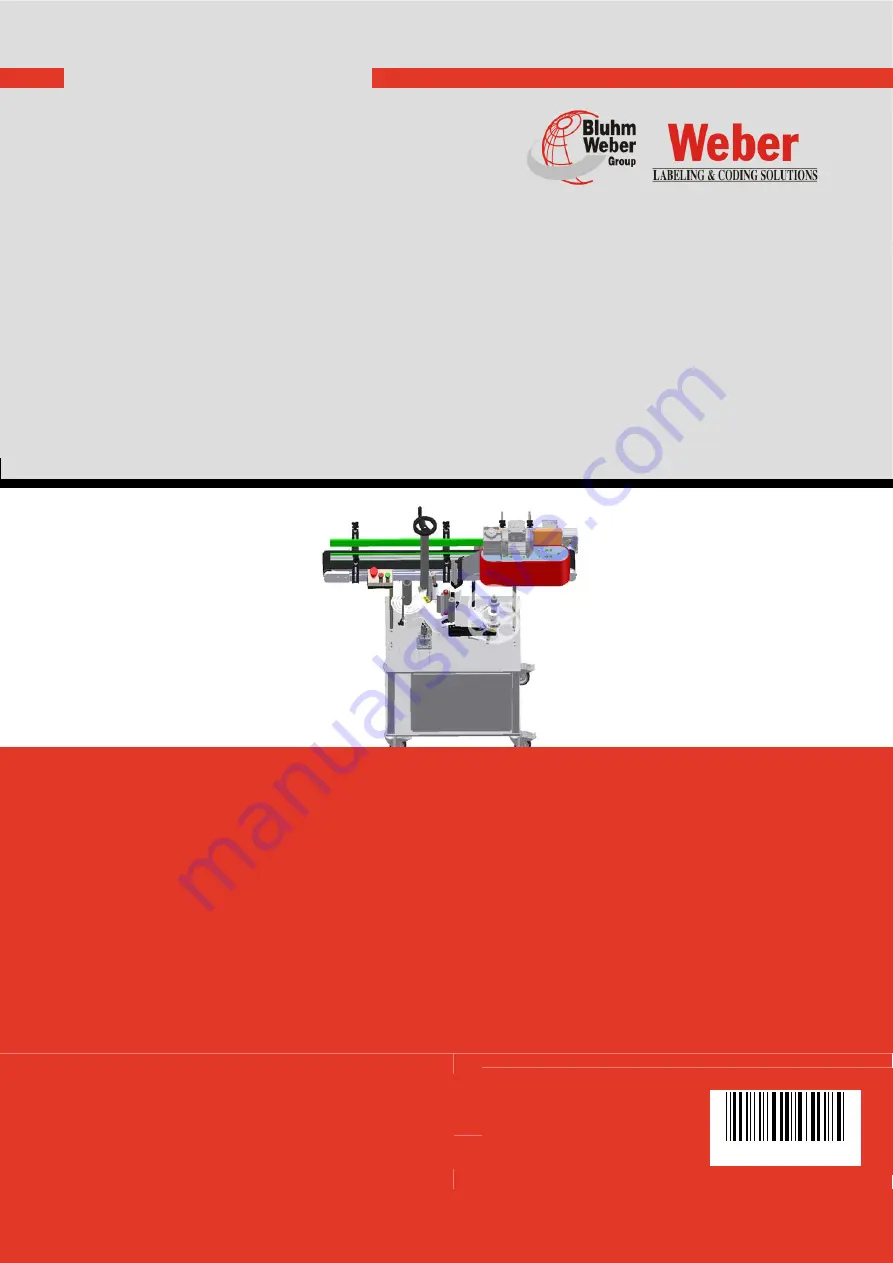
Original User’s Manual
Installation, Setup, Operation and Maintenance
Geset 121
Article number of documentation 32708732
Copyright ©, Weber Marking Systems GmbH
Weber Marking Systems GmbH
Maarweg 33
D-53619 Rheinbreitbach
E-Mail: [email protected]
http://www.webermarking.de
Version: 02.08.12 /GRN
32708732
Содержание Geset 121
Страница 2: ...Blank page...