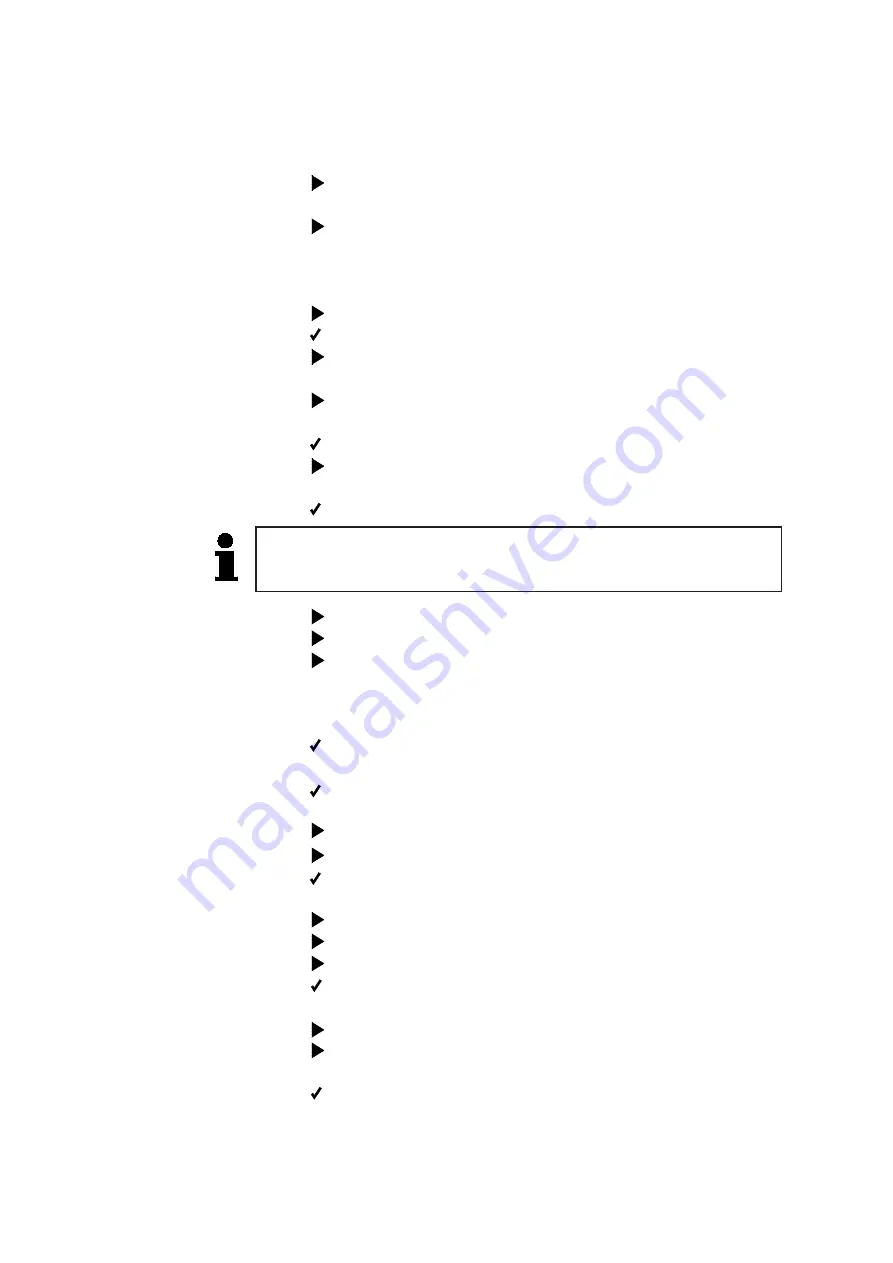
22
5.5. Testing the safety devices
Every day before placing the machine into operation and after
extended work breaks, the operation of the near-field shutdown
system of the radio remote control and of the emergency stop
switch must be tested.
Testing the near-field
shutdown system
Start the engine.
Stand at least 5m (=16 ft) behind the machine.
Drive toward you using the operating speed.
To use the operating speed:
- select the ECO-Mode
- Navigate the machine with the joysticks
The movement is stopped once you step into the near field of
the machine.
The display of the remote control indicates in which area
the minimum distance was not observed.
Step out of the safety area OR
Use the drive lever to steer in the opposite direction.
The machine can be driven again.
Testing the emergency
stop switch
Start the engine.
Drive forward at operating speed.
Press the emergency stop switch.
The machine stops moving and switches off the diesel engine;
the remote control is powered off.
Set the ignition switch on the machine to the “0” (OFF) position.
Unlock the emergency stop switch on the remote control
by turning it in arrow direction.
The machine can be started again.
If the safety devices are not operational, stop working with
the machine immediately and promptly rectify the cause.
For this purpose, contact Weber MT’s service organization.
Starting the engine
Take the radio remote control out of its holder in the rear
hood and safely place the carrying strap around you.
Check the position of the following switches:
- Remote control on/off: off
- Vibration:
off
- Steering joysticks:
neutral position
Turn the key switch on the machine to the “I” (ON) position.
The power is switched on, and the roller is ready to start.
Switch on the radio remote control with the corresponding
selector switch.
Press and hold the pushbutton “Engine start” until the engine
starts running.
The machine begins with the start-up procedure.
Allow the engine to warm up at idle speed for a few moments
before activating other functions (e.g. vibration or ECO mode).
The machine is ready for operation.
After igniting, the engine will run at full throttle for approx.
5 seconds. Only after that time will the remote control indicate
any errors of the machine.
Содержание MC 85
Страница 1: ...MC 85 0142410 0142411 Operating and Maintenance Manual...
Страница 55: ...55...
Страница 56: ...56 10 5 Hydraulic circuit diagram...
Страница 58: ...58 Notiz note...
Страница 59: ...59 Notiz note...