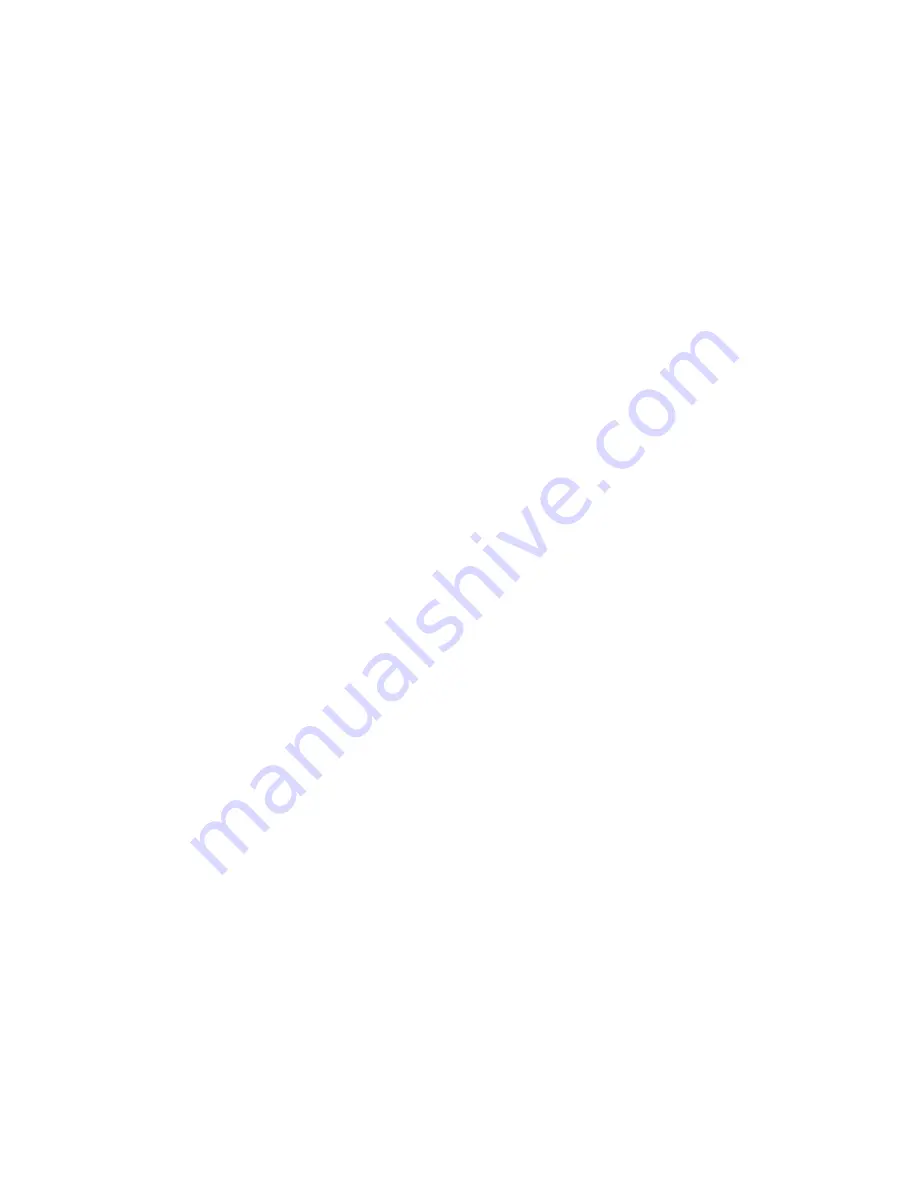
2
07-1036
MAIN SPEED CONTROL KNOB
Located next to the start pushbutton, the main speed
control knob is used to set the running speed before the
deceleration count is reached. Turning the knob clock-
wise will increase the speed. Rapid speed increases can
cause telescoping of the rewind roll and web breakage.
Therefore, the motor control has been pre-adjusted to
accelerate at an appropriate rate.
START PUSHBUTTON
Pressing of the START pushbutton will perform two
tasks. Most importantly, the motor control is enabled,
permitting the motor to run at the set speed. In addi-
tion, when operating the counting system in the length
mode, the START pushbutton will also reset the counter
to zero if the counter stop setting (Preset B) has been
reached. Automatic reset to zero does not take place in
the photoelectric counting mode because the operator
may have already set an initial count into the counter to
account for labels that have passed the scanner.
STOP PUSHBUTTON
The STOP pushbutton provides rapid stopping of the
machine. When pushed, the main drive motor is turned
off and dynamic motor braking is applied. Although it is
also possible to stop the machine by turning the speed
control down to zero, it is recommended that the STOP
pushbutton be used to insure that the machine will not
start again until desired.
IDLE SPEED CONTROL KNOB
The idle speed control knob is located on the control
cabinet on the far right hand side of the machine. When
the deceleration preset number (Preset A on the coun-
ter) is reached, provided you have the STOP AT PRE-
SET/BYPASS PRESET switch in the “STOP AT PRESET”
mode, the motor control will automatically switch from
the main speed control knob to the idle speed control
knob. The speed range of this knob is restricted to only
the lower twenty percent of the speed range. Once the
counter has been reset, the main speed control knob is
reactivated.
POWER ON/OFF SWITCH (AND POWER
INDICATOR)
The POWER ON/OFF switch is used to turn the main
power to the machine on and off. The switch has an
indicator light that illuminates when power is on.
UNWIND TENSION CONTROL
The unwind brake is a mechanical friction type consist-
ing of a brake band wrapped around a drum. An ad-
justing knob on the front of the machine provides a
means of tightening the brake band. Turning the knob
clockwise increases the unwind brake tension. To set
the brake initially, turn the unwind coreholder manually
and adjust the brake tension until a slight amount of
drag can be felt when turning the coreholder. When the
machine is running, make small adjustments as required
to obtain the desired web tension.
COREHOLDERS
Web Techniques rewind machines are available with
various types of coreholders. Lift-off cam-lock core-
holders are supplied as standard equipment. Air inflat-
able coreholders are available as an option. In addition,
some machines are configured with a combination of
both systems (usually a lift-off cam-lock coreholder on
the unwind and an air inflatable coreholder on the re-
wind). An air inflatable coreholder is required on the
rewind position in order to use an optional slitting
attachment.
LIFT-OFF CAM-LOCK COREHOLDERS
As the name implies, these coreholders can be removed
from the machine by simply lifting them straight up
from the table top and out of their sockets. The ad-
vantage of this type of coreholder is that heavy rolls can
be installed and removed by sliding them onto and off
the machine. If your machine is equipped with lift-off
cam-lock coreholders, they will be packaged separately
and must be installed on the machine.
A) Locate the package containing the coreholders. Ob-
serve that there is a slotted shaft protruding from
the lower end of the coreholder.
B) GENTLY lower the shaft into the socket in the un-
wind and rewind spindle. The shaft will probably
come to rest on top of the drive pin inside the spin-
dle and the bottom of the coreholder will be ap-
proximately 3/8 inch above the table top. Simply ro-
tate the coreholder until the drive pin and slot align
and the coreholder drops the rest of the way into its
socket.
C) Remove and install the coreholder several times so
that you become familiar with the “feel” of proper
coreholder engagement. This is important because
when the coreholder is installed by inserting it
through the core of a roll of material, you will not