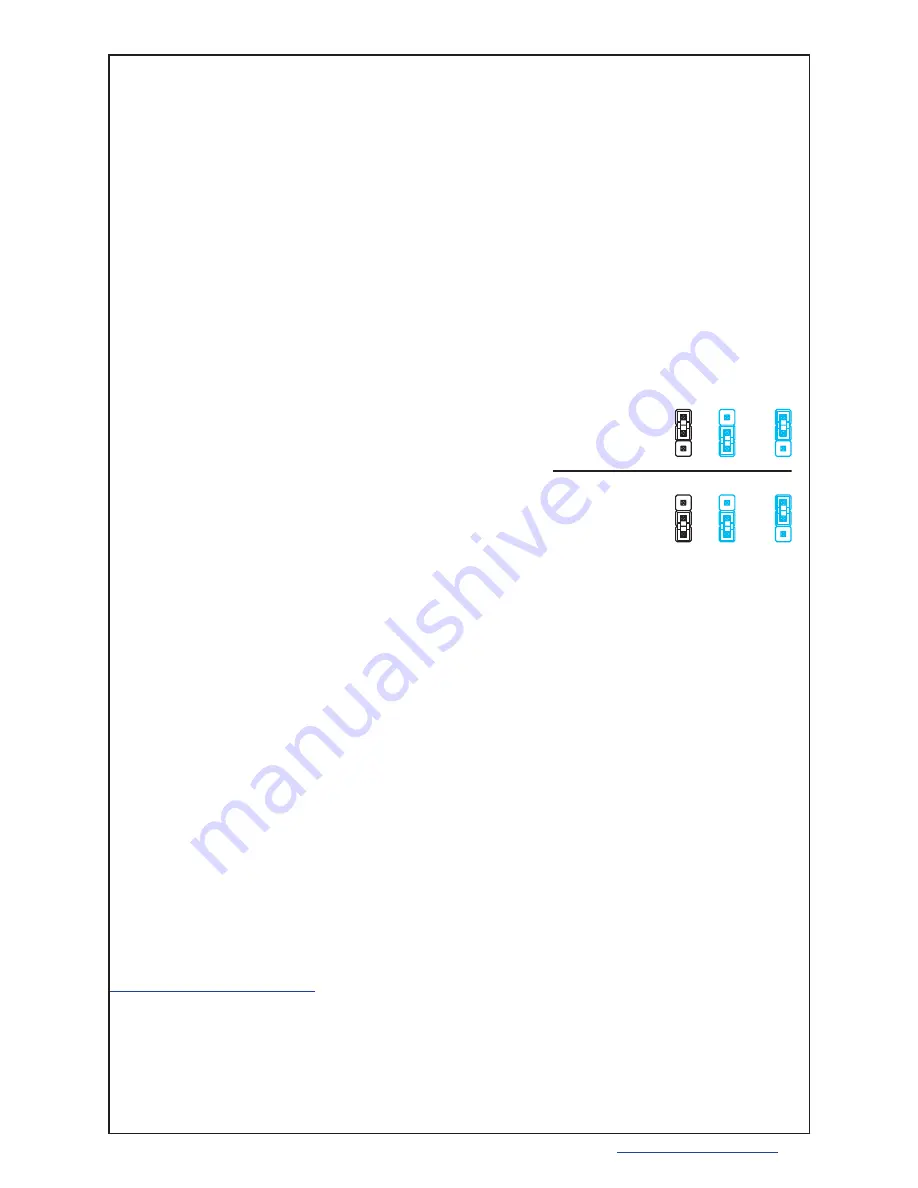
© 2005
PRELIMINARY
LDTC2/2
PAGE 10
LDTC2/2-00400-A Rev A
WTC OPERATION, continued
4. PROPORTIONAL GAIN AND
INTEGRATOR TIME CONSTANT -
PI
TERMS
The LDTC2/2 is confi gured to the mid-range
positions appropriate for most laser diode loads.
To adjust these parameters to optimize the
temperature control system time to temperature or
stability, contact Wavelength.
5. POWER SUPPLY SELECTION
The VDD voltage supply input is common to both
the WLD3343 and the WTC3243. This supply
furnishes the voltage to the control electronics of
the devices as well as the compliance voltage for
the WLD3343 Laser Driver.
The supply should be capable of providing at least
3.0 Amps of current in applications that use a
separate VS supply in the temperature control
implementation. Temperature control applications
that tie VDD and VS together require a VDD
current capacity that equals the sum of the
maximum TEC or Resistive Heater current,
plus the maximum laser diode current, plus
approximately 200 mA for the control electronics
of the WTC3243 Temperature Controller and the
WLD3343 Laser Driver, plus current to an optional
fan. Using the maximum potential of the WLD and
WTC will not require more than 6.0 Amps.
VS is the voltage that is applied to the TEC
or resistive heater. This voltage should be high
enough to supply the voltage required by the TEC
or resistive heater plus the compliance required by
the WTC. The voltage available to the TEC will
be from between 0.5 to 1.8V lower than VS. To
minimize power dissipation in the WTC, keep VS
as low as possible.
Online Safe Operating Area (SOA) calculators
are available for the WTC3243. Calculate the
maximum power dissipation of your design at
http://www.teamwavelength.com/
tools/calculator/soa/defaulttc.htm
before applying
power to the LDTC2/2.
7. MONITOR ACTUAL TEMP AND
SETPOINT
Pins 9 & 10 of Connector 2 are ACT T Monitor and
SET T Monitor respectively. Measure the actual
sensor voltage across Pin 9 and Pin 12 (COM).
For a 10k
Ω
thermistor with 100
µ
A bias current,
the resistance (in k
Ω
) is given by:
R
=
V
PIN 9
/ 0.1
To monitor the Setpoint Voltage used by the WTC,
use pins 10 and 12.
For other sensor calculations, contact Wavelength.
6. TEMPERATURE SETPOINT
Wavelength introduces a special setpoint circuit
with the LDTC2/2. An on-board trimpot (TSET)
will adjust the voltage from 0.3V to 2.5V.
Additionally, Pin 11 (R TC SET) & 12 (COM) of
Connector 2 will accept a DAC voltage (from 0.3
to 2.5V). The new feature - the “Failsafe Setpoint”
will default the setpoint to 1V (~25°C for a 10k
Ω
thermistor) if the chosen signal (from pot or DAC)
falls below 0.3V.
A jumper set lets you choose to use only the
on-board potentiometer or the external voltage.
JP1 confi gures the Remote Temperature Setpoint
choice. There is about 100mV of hysteresis built
into the default voltage. The input impedance of
the R TC SET is greater than 20k
Ω
and is fully
buffered.
If you use a different sensor or would prefer a
different default voltage, contact Wavelength.
8. ENABLE CURRENT TO TEC
Output current is supplied to the load as soon as
power is applied to the controller. The Power LED
indicator will light GREEN when power is applied.
ExtTset
Vset
Vset
PDset
ExtTset
Vset
PDset
Use On-board
trimpot only
Use Extermal
Voltage
Figure 1
Source of setpoint