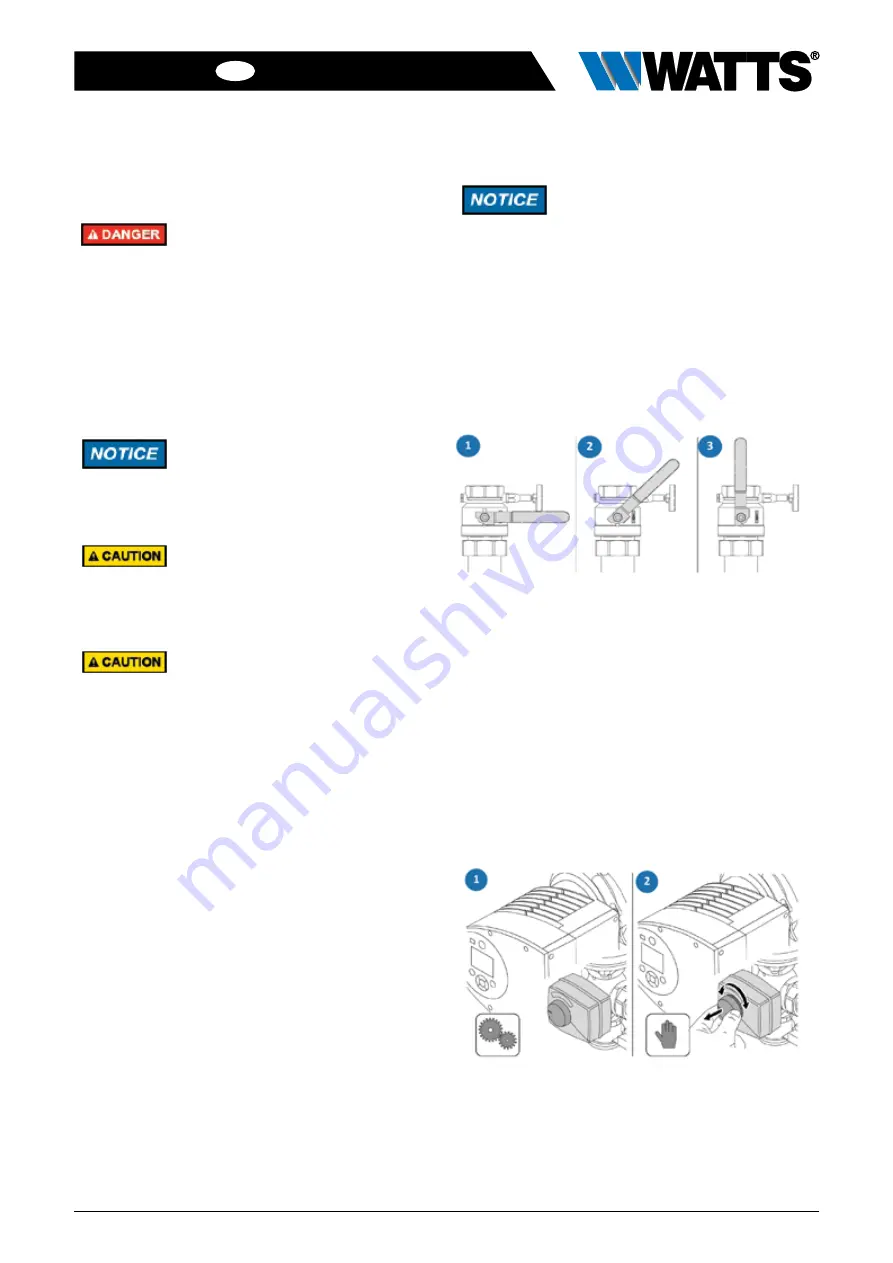
IM-HKM40-50_HK40-50-DE-W-UK-12-2019-Rev.1 | Part no. 10083684
7
EN
ENGLISH
5 Installation and commissioning
Electricity!
Risk of death from electric shock!
• Work on live parts must be carried out only by
trained electricians.
• Disconnect the power supply to the unit before
carrying out any installation, maintenance,
cleaning or repair work and secure it against
reconnection.
Installation and commissioning of the pump
unit must be carried out only by specialist
personnel who have been duly trained and
authorised by the manufacturer.
When carrying out repairs and replacing
parts, the prescribed mounting positions and
flow directions for the individual components
to be replaced must be observed.
Material damage!
Opening shut-off valves quickly produces
pressure surges.
• Always open shut-off valves slowly and in a
controlled manner.
5.1 Installation
Before installing the unit and starting it for the first time,
check all screw fittings and retighten if necessary!
Torque
• 1½” screw fittings 130 Nm
• 2” screw fittings 190 Nm
Requirements
• The fittings are preassembled at the factory; however, the
tightness of the seal is to be checked before commissioning
(pressure test).
5.2 Starting the unit
Requirements
• The pump unit is fully installed.
1. Connect the power supply (see separate pump
documentation).
9
The pump unit automatically switches itself on when
the power supply is connected.
2. Bleed the heating system.
The pump unit must be switched off during
the bleed process.
5.3 Lever position
The ball valve on the return circuit is fitted with a gravity brake.
The gravity brake must be set to fill the system.
• Move the level to position (2).
• The gravity brake is set and allows the system to be bled.
• Fill the system.
1
Service setting: ball valve closed
2
Drain: ball valve half open (only included in the return
circuit)
3
Operating position: ball valve open
5.4 Mixing valve operating position
• Gently pull the knob on the mixing valve out.
• The mixing valve setting can be changed manually.
• Push the knob on the mixing valve back in to its original
position.
• The knob locks, mixing valve is in automatic setting.
1
Automatic setting
2
Manual operation