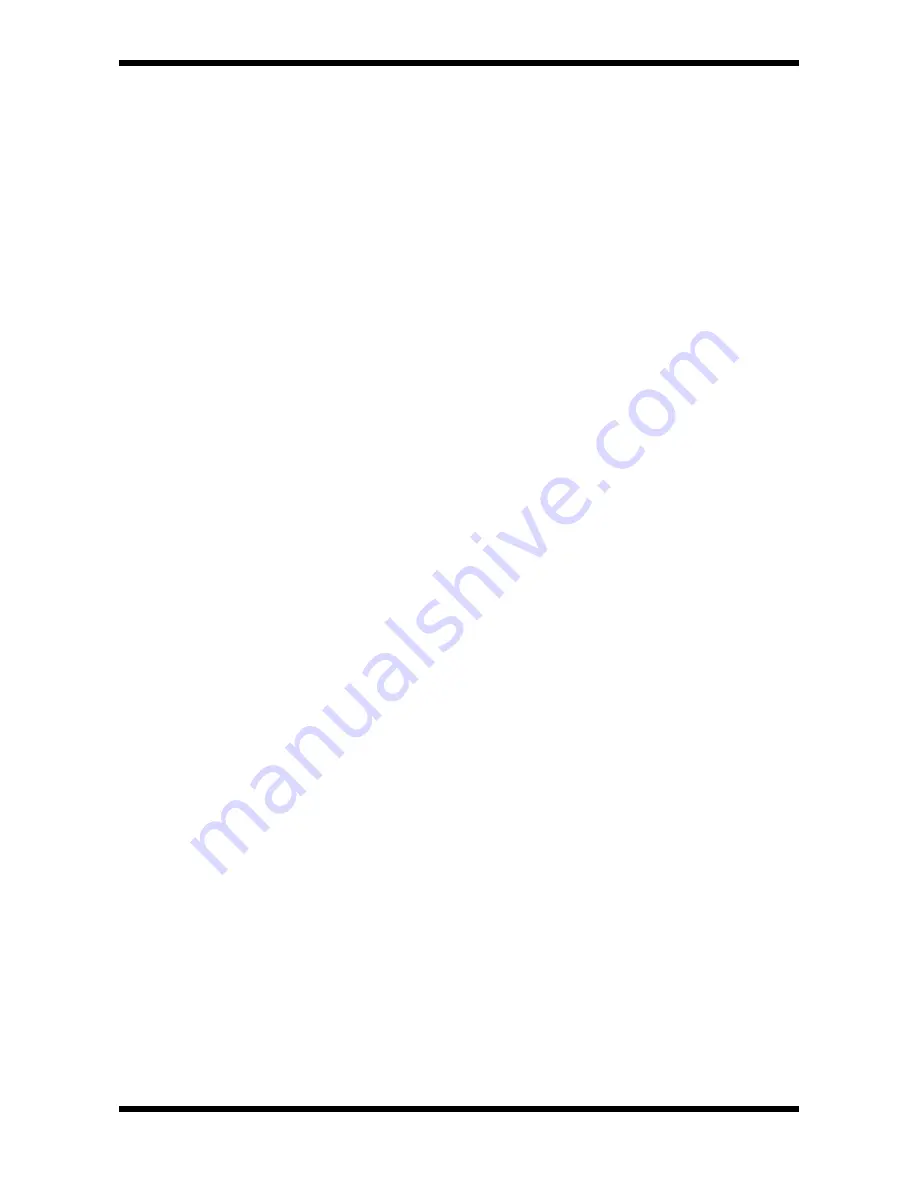
Contents
Section
Page
Technical Data
1
Introduction
2
Boiler Location
3
Gas Supply
3
Flueing
3
Air Supply
4
Water Supply
4
Condensate Drain
4
Sealed Systems
5
Electricity Supply
5
Installation
5
Removing Case
6
Boiler Mounting Box
6
Flue and Air Duct
6
Terminal
6
Twin Pipe Assembly
6
Plumbing
7
Gas Connection
7
Condensate
7
System Design
8
Electrical Connections
8
Commissioning
9
Fault Finding
18
Servicing
20
List of Figures
Page
Fig 1.
Gas Valve
11
Fig 2.
Installation Dimensions
12
Fig 3.
Schematic Wiring
13
Fig 4.
Physical Wiring
14
Fig 5.
Fixing Positions
15
Fig 6.
Boiler Panel Assembly
16
Fig 7.
Concentric Flue & Air duct
17
Positions
Fig 8.
Twin Pipe Positions
17
Fig 9.
Spares
23
Fig 10.
Major Components
24
Fig 11.
Example Condensate Disposal
25
Fig 12.
Condensate Drain Trap
25
Introduction
These Instructions cover a range of lightweight, wall
hung, gas fired, condensing boilers which are room
sealed and fan assisted on the flue side. The flue
systems available are Concentric, left, right, or rear,
up to 2 metres and, Twin Pipe, horizontal total
combined length of 22 metres or vertical, up to a
total length of 30 metres. The ignition system is fully
automatic and the boiler incorporates an electronic
modulation gas control.
There are two models with different output ranges -
see the
Technical Data on page 1
for details.
The boiler casing is of white enamelled mild steel.
They are suitable for connection to open vented or
sealed systems. These systems may be pumped
central heating or pumped central heating combined
with a pumped indirect domestic hot water circuit.
Gravity circuits must NOT be used.
The boilers include a pump overrun device so it is
essential that there is an open circuit for water to
flow between the flow and return. In some system
designs this may require the addition of a bypass, an
automatic bypass is preferred.
The boilers also contain integral frost protection, the
boiler will fire if the temperature within it approaches
4 to 5 degrees Centigrade. It will do this even when
turned to Off, and can only be inhibited by removing
the Permanent Live supply to the boiler.
Adequate arrangements for completely draining the
system, by provision of drain cocks MUST be
provided.
Gas Safety (Installation and Use)
Regulations, (as amended).
It is the law that all gas appliances are installed by a
competent person (e.g. a CORGI registered opera-
tive) in accordance with the above Regulations.
Failure to install appliances correctly could lead to
prosecution.
It is in your own interest, and that of safety, to
ensure that the law is complied with. The installation
of the boiler MUST also be in accordance with the
current I.E.E.. Wiring Regulations, the Local Building
Regulations, Building Standards (Scotland), the Bye
Laws of the Local Water Undertaking, any relevant
requirements of the Local Authority, and Health and
Safety document No 635, “Electricity at Work Regu-
lations”.
Detailed recommendations are contained in the
following British Standard Codes of Practice.
Codes of Practice.
BS.6798 Installation of gas fired hot water boilers of
rated input not exceeding 60kW.
BS.5449:1 Forced circulation hot water systems
(small bore and microbore domestic central heating
systems).
BS.5546 Installation of gas hot water supplies for
domestic purpose (2nd Family Gases).
BS.5440: Part1. Flues (for gas appliances of rated
input not exceeding 60kW).
BS 6891 Specification for installation of low pressure
gas pipework.
BS 7074:1 Application, selection and installation of
expansion vessels and ancillary equipment for
sealed water systems.
Condensing Boiler
2
06/06/01
Содержание FFC 30/60
Страница 13: ...Condensing Boiler 12 06 06 01 Installation Dimensions Fig 2 Pipe Connections Locations Service Access ...
Страница 14: ...Condensing Boiler 13 14 12 00 Schematic Wiring Fig 3 ...
Страница 15: ...Condensing Boiler 14 06 06 01 Physical Wiring Diagram Fig 4 ...
Страница 20: ...Condensing Boiler 19 Fault Diagnosis ...