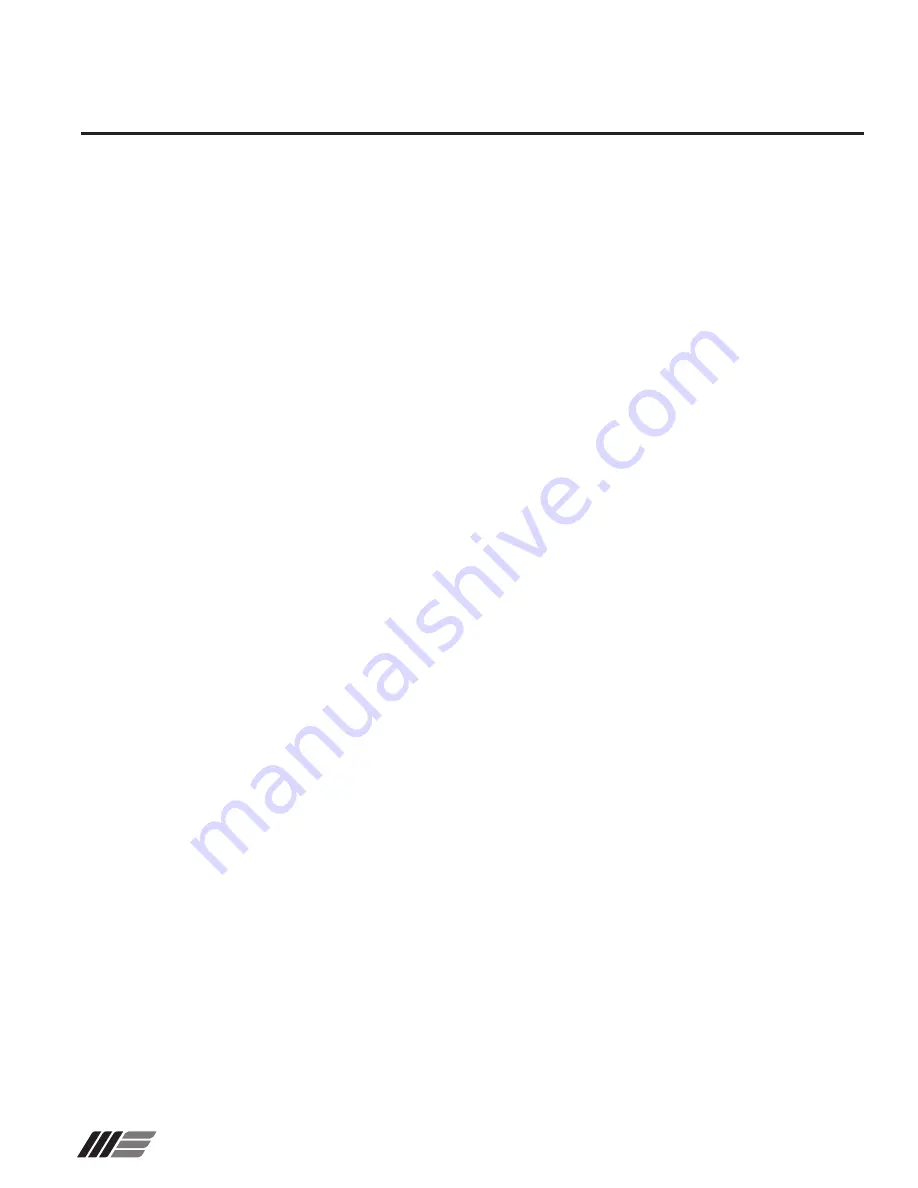
11
Wanner Engineering, Inc.
United States
Instant Information: www.wannereng.com
(61) 33-5681 Fax (61) 33-6937
SCK-991-400B
Note:
The troubleshooting of mechanical seals is ordinarily
left to the seal manufacturer. However, the fact that Stan-Cor
pumps are nonmetallic presents some possible problems that
are particularly germane to plastic pumps. Refer also to Fig. 8
for a general guide to troubleshooting centrifugal pumps.
Leakage At Rotating Face Of Mechanical Seal
Improper Setting of Rotating Member. Check the operating length
of the mechanical seal to be sure the seal is set according to the
manufacturer’s recommendations:
• If too
long
, the spring force may not be sufficient to seal off
at the rotating face.
• If too
short
, the spring force may be excessive and result in
premature wear of rotating elements. Examine the rotating
face for evidence of chemical attack.
Foreign particles Between Rotating Member and Stationary
Seat
. The mating surfaces of the rotating element and the
stationary seat are highly polished, and the introduction of any
foreign particles results in abrasion and leakage. These particles
may be introduced on reassembly, or may precipitate from the
fluid being pumped (e.g., crystallization in a saturated fluid). To
reduce the possibility of foreign particles on reassembly, be very
careful to keep both elements of the mechanical seal free of dust
prior to assembly. Wipe the mating surfaces with a lint-free cloth
saturated with clean, light oil. A double seal with flush may be
required when solids are excessive.
Stationary Seat Cracked or Chipped
. Check the stationary seat
element for cracks or chips on the sealing surface which could
cause excessive wear and leakage at the rotating face.
Mechanical Defects
. Check the rotating member of the
mechanical seal for defects in the body or clamp ring.
Troubleshooting
Leakage Behind Rotating Face Or At Clamp Ring
Of Mechanical Seal
Mechanical Defects
. Check the rotating member of the
mechanical seal for defects in the body or clamp ring.
Teflon Bellows Not Concentric with Shaft
. Apply Light
pressure to the O.D. of the spring adaptor, while you rotate the
impeller shaft until radial runout is eliminated.
Surface Defect in Shaft Sleeve
. Check the surface of the shaft
sleeve under the rotating member for scratches, indentations, or
foreign particles which may cause leakage. Minor imperfections
can be removed with emery paper.
Leakage Behind Retainer Gland From Stationary
Seat
Foreign Particles Under Gaskets
. Check the seat gaskets and
back cover to be sure that they are clean and free of foreign
particles.
Stationary Seat Cocked
. If the retainer gland is not tightened
squarely, the seat may be cocked, permitting leakage past the
gaskets. Readjust the four hex nuts which hold the retainer gland
in place, until leakage stops. Place the ceramic stationary seat
into the back cover by hand: do not use the retainer gland to force
the seat into position. Excessive torque loads on gland nuts may
break the back cover.
Stationary Seat Cracked or Chipped
. Slide the rotating element
and retainer gland back, if possible, and inspect the stationary
seat. Check carefully for hairline cracks or chips in the sealing
area.