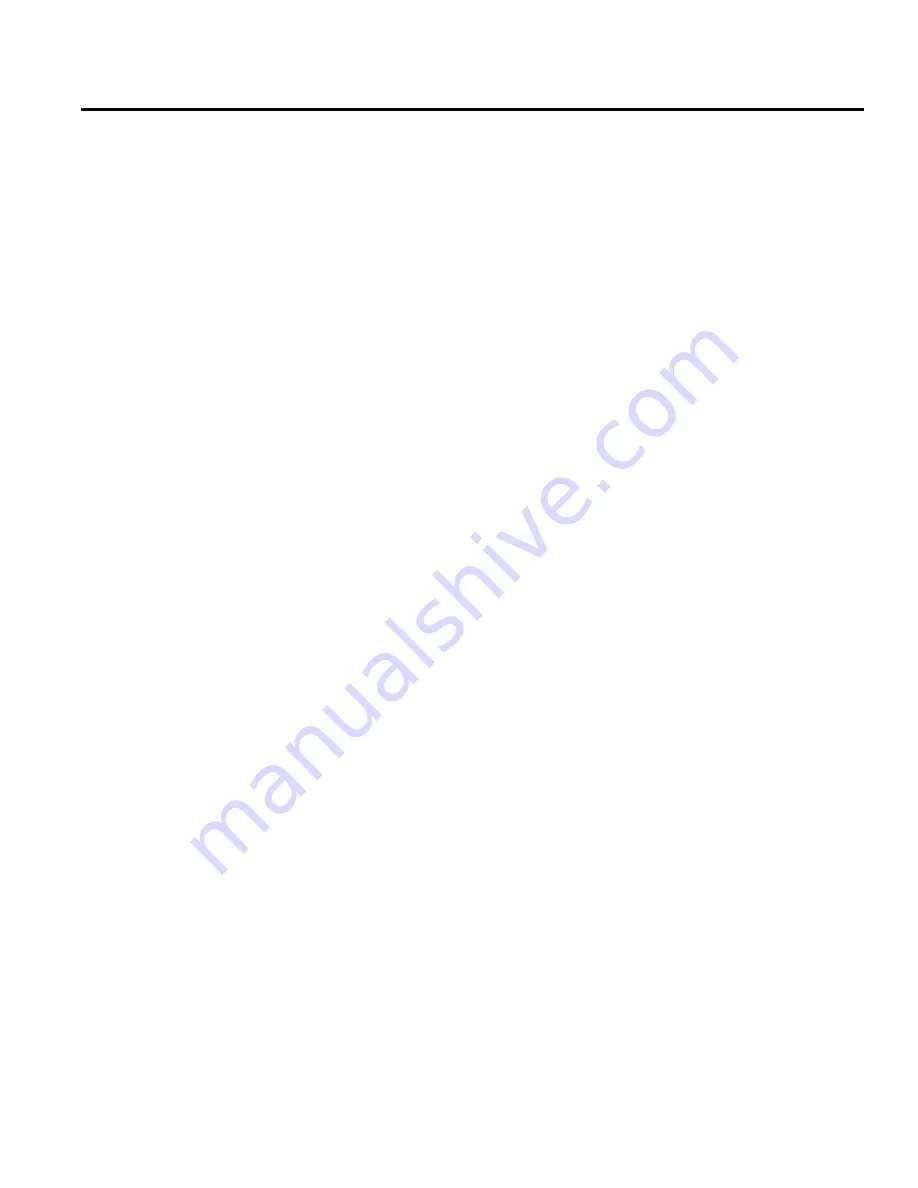
17
D10-991-2400 5/1/04
e. Using petroleum jelly or grease to retain it, install the O-ring
(65) and slide the housing (30) down over the shaft. Be sure
the holes in the housing and the cylinder housing are
properly aligned.
f.
Install two assembly studes from Tool Kit, washers and nuts
on the threaded studs, but don’t tighten yet. You may want
to insert two or more bolts (4) into the unthreaded holes of
the housing and cylinder housing to help align the parts.
g. Alternately tighten the nuts of the assembly studs to evenly
draw the housing down to the cylinder housing. Be sure the
O-ring (65) stays in place.
Also, as you tighten the nuts keep checking the shaft
alignment by turning the shaft (use the rotator in the Wanner
Tool Kit). If the shaft begins to bind and become difficult to
turn, back off the nuts and realign the shaft. When the
housing is tight against the cylinder housing, you should be
able to turn the shaft smoothly.
h. After the pump housing and cylinder housing are together,
insert bolt (25) with lock washer (5) (at the 4 o’clock position)
through the pump housing and into the cylinder housing.
Repeat with a bolt (29) in the 10 o’clock position. Tighten
evenly and then remove asembly studs.
i.
Turn the shaft again to check its alignment.
5. Replace Shaft Seals
a. Apply a thin film of grease on the seal protector tool (part of
the Wanner Tool Kit). Slide both seals onto the tool, with the
spring side of the seals toward the open end of the tool.
Apply a heavier coat of grease between the seals and press
them together.
b. Apply a coating of Loctite® High-Performance Pipe Sealant
With Teflon®, or a comparable product, to the outer surface
of both seals and the inside surface of the opening in the
pump housing where the seals will rest.
c. Apply a light film of grease to the drive shaft. Slide the seal
protector tool (with the two seals) over the end of the shaft.
d. Slide the seal inserter tool (from the Wanner Tool Kit) over
the seal protector tool, and press the seals completely into
place. Tap the tool with a soft mallet to firmly seat the seals.
6. Adjust CamShaft Endplay
a. Remove the three set screws (22) from the cylinder casting
(24), and clean them.
b. Insert the centerbolt (1) into the hole in the center of the
cylinder casting. Turn it in to move the bearing adjusting
plate (61) and cup tight against the bearing cone.
c. Back out the centerbolt two full turns, then turn it back in
again until it is tight against the adjusting plate (61).
d. Back out the centerbolt exactly 1/4 of a turn.
e. With a plastic mallet (or a regular mallet and wooden board)
to prevent damage to the shaft, rap the end of the shaft 3 or
4 times. This will provide about 0.006 in. (0.15 mm) endplay
in the shaft.
f.
Apply removable threadlocker to the threads of the three
cleaned set screws (22).
Screw the three set screws (22) into the cylinder casting
until they contact the bearing adjusting plate (61).
g. Remove the centerbolt (1).
D/G-10 Service (Hydraulic End)
7. Install Plungers
NOTE: If the plungers (21) have been removed from the
valve plungers (54), do not reuse them. Install new ones
instead.
a. Rotate the pump shaft so the piston is at the top-dead-center
position.
b. Place a plunger on the exposed screw end of the plunger
guide tool from the Wanner Tool Kit. The larger-diameter
side of the plunger should face the tool.
c. Screw the guide (with the plunger) into the valve plunger
(54) until tight.
d. Hold the single bottom handle of the guide, and turn the
double top handle to force the plunger to seat on the valve
plunger. This is a press-fit – when installed, the plunger
should be tight against the shoulder of the valve plunger.
NOTE: Do not remove the plunger guide until the
diaphragm is installed (see below).
e. Install the diaphragm as outlined below, then repeat the
procedure for the other two plungers and diaphragms.
8. Reinstall Diaphragms
a. With the plunger guide tool still screwed into the valve
plunger (54), pull the valve plunger up until the cross-holes
in the valve plunger are exposed.
b. Insert a diaphragm Allen wrench (from the Wanner Tool Kit),
through the top hole — to hold the plunger (21) away from
the cylinder casting, and to keep the valve plunger from
turning when the diaphragm is being installed.
c. Place the diaphragm (20) onto the plunger (21), ridge-side
out.
d. Center the diaphragm follower (19) on the diaphragm.
e. Place the O-ring (18) onto the follower screw (17).
f.
Apply a small amount of threadlocker to the threads of the
follower screw.
g. Insert the follower screw (with O-ring) through the diaphragm
follower (19) and diaphragm (20), and screw it into the valve
plunger (54).
h. Hold the plunger holder, and torque the follower screw to
18 in.-lbs (2.0 N-m).
i.
Repeat the above procedure for the plungers and
diaphragms of the other two cylinders.
j.
Fill the reservoir with fresh oil and prime the pump, as
outlined in the Fluid-End Service Section.
9. Reassemble Pump Head
Reassemble the pump head as outlined in the Fluid-End
Service Section.