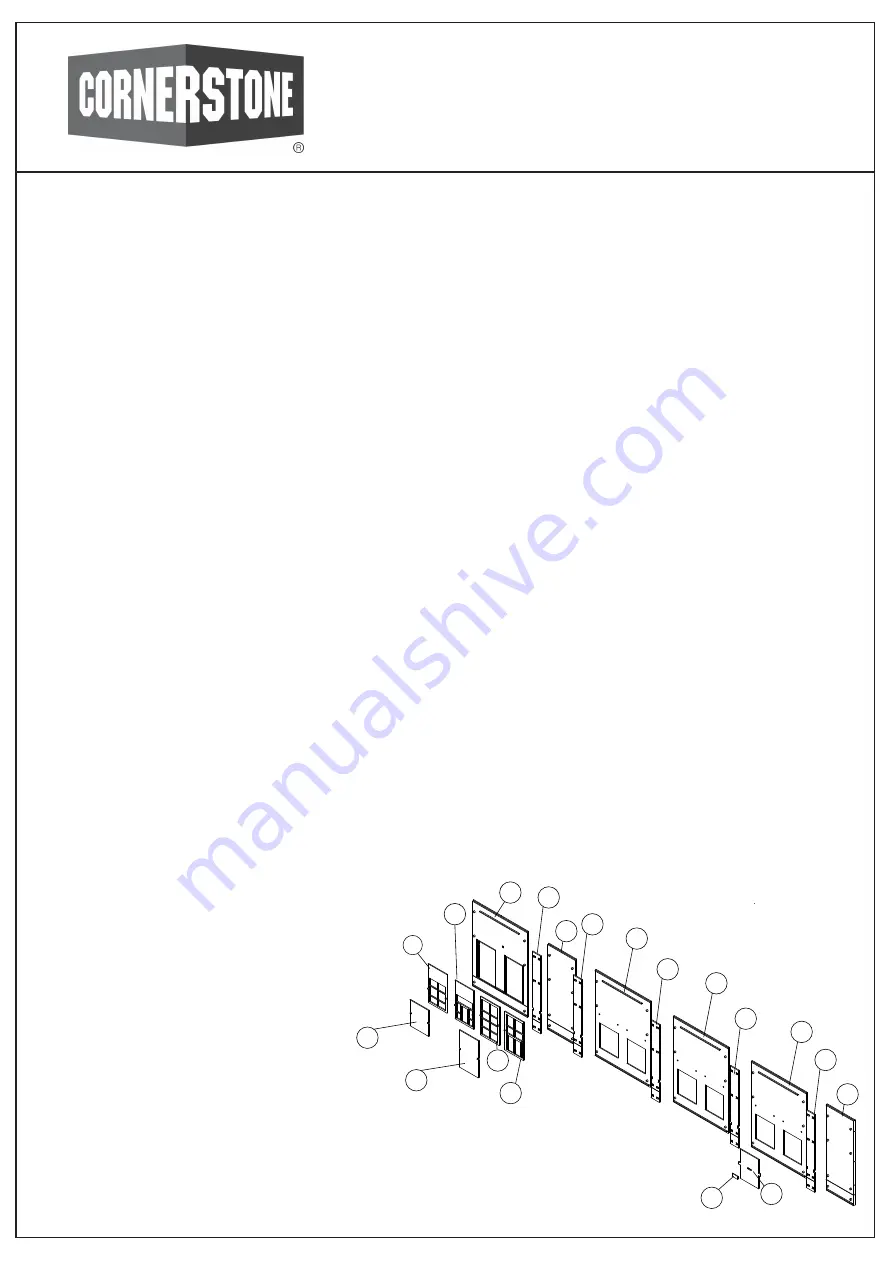
HO Structure Kit
MODERN PRINTING
PLANT
933-4079
© 2017 Wm. K. Walthers, Inc., Milwaukee, WI 53218 waltherscornerstone.com I-933-4079 Printed In Taiwan
40
41
23 x2
24 x2
42
43
12
13
3
26 x6
44 x6
13
13
13
13
2
3
2
2
Thanks for purchasing this Cornerstone kit. All parts are styrene plastic, so use compatible glue and paint to assemble and finish your model.
Please take a few minutes to read these instructions and study the drawings before beginning. You may find it easier to assemble some parts
and paint them as subassemblies before starting the next step. PLEASE NOTE – This model is based on “tip-up” buildings in use since the
1980s, and like the prototypes, consists of interchangeable wall panels that can be arranged as desired to customize your structure. These
instructions cover a typical assembly, however you can use fewer parts to make a smaller structure, or combine complete kits and matching
Truck and Railroad Docks wall panels (#933-4070 sold separately) for a bigger building. The SceneMaster Modern Wall Light 3-Pack #949-
4318, sold separately) may be used in place of the nonworking light fixture (57). For ease of assembly, you may wish to have these additional
parts on hand before starting. Some parts included in this kit are not needed for assembly or are optional, and can be kept for future projects
or discarded as desired.
For thousands of years printed materials of all kinds have entertained, informed and inspired us, and despite late 20th century predictions of a
“paperless society” as computers became an integral part of everyday living, books, magazines and more are still very much in demand. Along
with updated machinery and methods, today’s printing plant is very different from those of earlier times. Like many other industries, printing
operations have consolidated and closed older less efficient plants for newer purpose-built facilities. These can often be found in outlying indus-
trial parks with convenient access to both road and rail transport. Many have been constructed using precast concrete panels, a process known
as “tip-up construction” as the panels are poured in forms on site, then raised or tipped up into final position using a large crane. Although used
by a variety of industries, buildings of this type are especially well suited to the needs of printers, as the concrete allows for more stable control
of both temperature and humidity inside the structure, both of which can play havoc with paper. To further control heat and humidity, large air
conditioning units will be found on the roof the structure. Office, employee facilities and other support services can also be found near a main
entrance. Worker safety and environmental protection have also played a part in the design of such facilities, which now use organic air clean-
ers or regenerative thermal oxidizers to clean exhaust gases of obnoxious odors and hazardous materials found in ink and cleaning solutions.
Because paper is recyclable, and paper dust creates safety and health hazards, additional air cleaners inside the building trap dust and route
it into a particulate dust cyclone. These elevated storage tanks can hold several tons of dust, which can be transported by truck for proper
disposal or recycling Like many industries, printing plants require oddly shaped and heavy raw materials in the form of huge paper rolls.
Depending on the products being produced, this may include newsprint, or coated stocks that are used to print books, magazines and catalogs.
While boxcars may be scarce along some rail lines today, they’re a constant visitor to trackside printers, where they’re spotted for unloading by
forklifts. As paper has to be kept clean and dry in transit, it’s delivered in assigned-service cars, equipped with larger doors and interior load
restraints. With their tight-fitting plug doors that seal out dirt and moisture, it’s not unusual to see RBL insulated boxcars delivering paper as
well. Since presses run nonstop, a typical operation will go through several carloads each day, with loads and empties handled by a local or
wayfreight. Finished products are typically shipped direct to customers by truck, so the far end of the operation will include warehousing and
dock doors for vehicles. A perfect freestanding business in your modern HO industrial park, your new model can also be used to depict a newer
addition to an older plant like George Roberts Printing Co. (#933-3046, sold separately). For additional railroad equipment, support structures,
scenery and supplies, see your participating hobby dealer, check out the current Walthers Model Railroad Reference Book or visit us online at
walthers.com.
BEFORE STARTING...
All wall panels are glued together on the back using molded locater pins and separate connector plates as shown. A raised ridge is molded at
the bottom to align with the base: double walls also have a raised ridge at the top to support the roof, and corner walls have a third raised ridge
along the outside edge. When assembling wall sections, work on a flat surface and allow parts to dry.
TRAILER LOADING DOCK - Assemble from Left to Right
1) Both solid top panel and all-glass style doors and windows
are provided for the Double Office Wall (12); choose one. Solid
Top Style - use Entry Door (40) and Window (41): both use
Small Glass (2x 23). All-Glass Style use Entry Door (42) and
Window (43): both use Large Glass (2x 24): align Glass with
locating pins on back of frames and glue where parts meet.
Glue completed assemblies to openings in rear of Wall.
2) Work on a flat surface and connect individual wall sections
(12, 3x 2, 2x 3) by aligning openings in Large Connectors (5x
13) with raised pins on back of walls and gluing where parts
meet as shown.
3) PLEASE NOTE: Optional Canopies (6x 65; 2 per wall, not shown) are provided for each truck door; if
you wish to use these, drill out mounting holes on the backs of Walls (2) using an .060" (1/16" 1.5mm) bit
- canopies will be installed in step 11. On the Truck Dock Walls (3x 2), Truck Doors (6x 26, one per wall)
can be left off to model an open door: for a closed door, glue Overhead Door Glass (44 - one per door, six
total) to rear of Truck Doors. Glue completed Doors to openings on back of Truck Dock Walls.