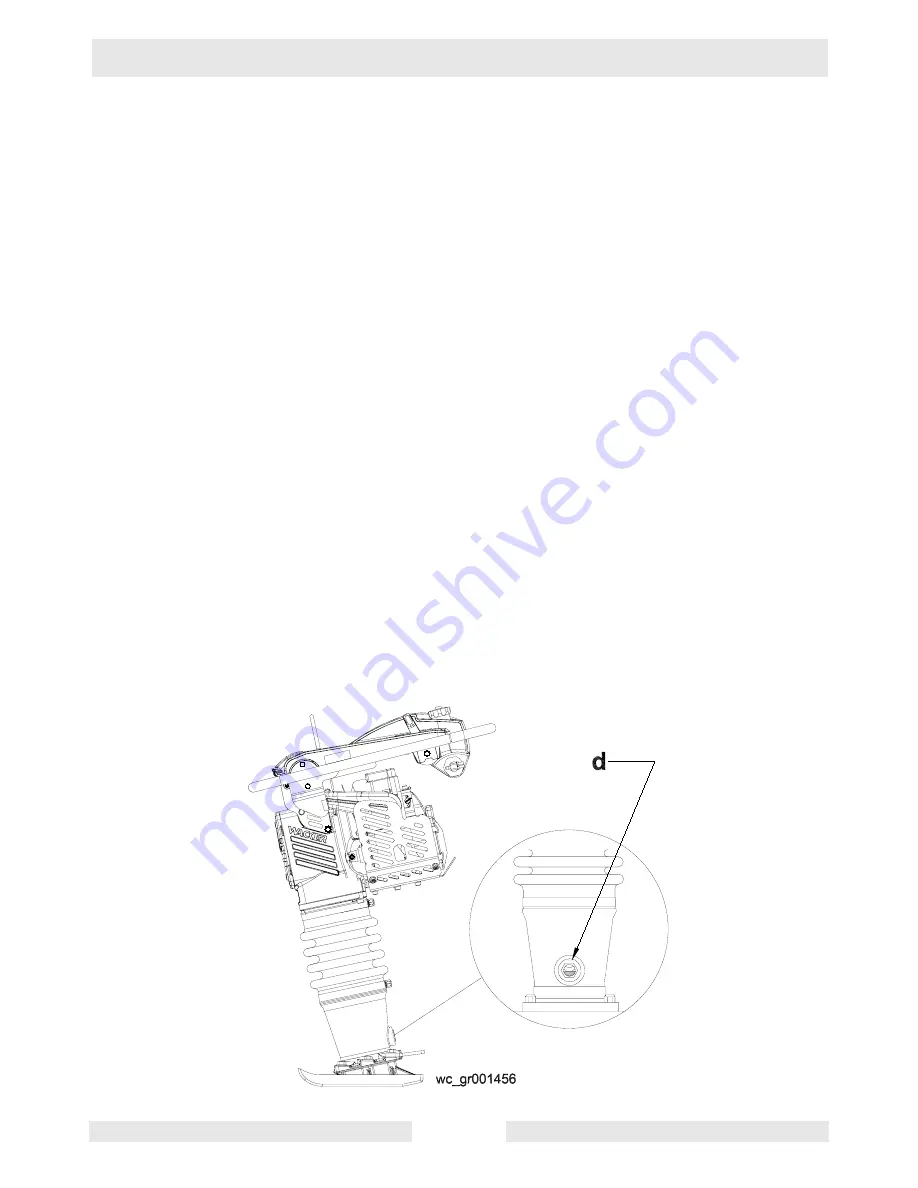
Maintenance
BS 50-4
wc_tx000309gb.fm
32
6.4
Lubrication
See Graphic: wc_gr001456
Ramming system
Check oil level:
6.4.1
Place the rammer so it is resting on its shoe on a level surface.
6.4.2
Check the oil level through oil sightglass
(d)
. Proper ramming system
lubrication is indicated when approximately 1/2–3/4 of the sightglass is
full.
6.4.3
If the oil is not visible, oil must be added through the sightglass port.
Tilt rammer forward and remove sightglass
(d)
. See
Technical Data
for oil quantity and type.
6.4.4
Wrap the sightglass threads with teflon tape. Install the sightglass
(d)
.
Torque to 9 Nm (6 ft.lbs.).
Oil change:
6.4.1
To drain oil, remove sightglass
(d)
and tilt the machine back until it is
resting on its handle.
Note:
In the interests of environmental protection, place a plastic sheet
and a container under the machine to collect any liquid which drains
off. Dispose of this liquid in accordance with environmental protection
legislation.
6.4.2
Remove sightglass
(d)
and fill with oil. See
Technical Data
for oil
quantity and type. Wrap the sightglass threads with teflon tape. Install
the sightglass
(d)
. Torque to 9 Nm (6 ft.lbs.).