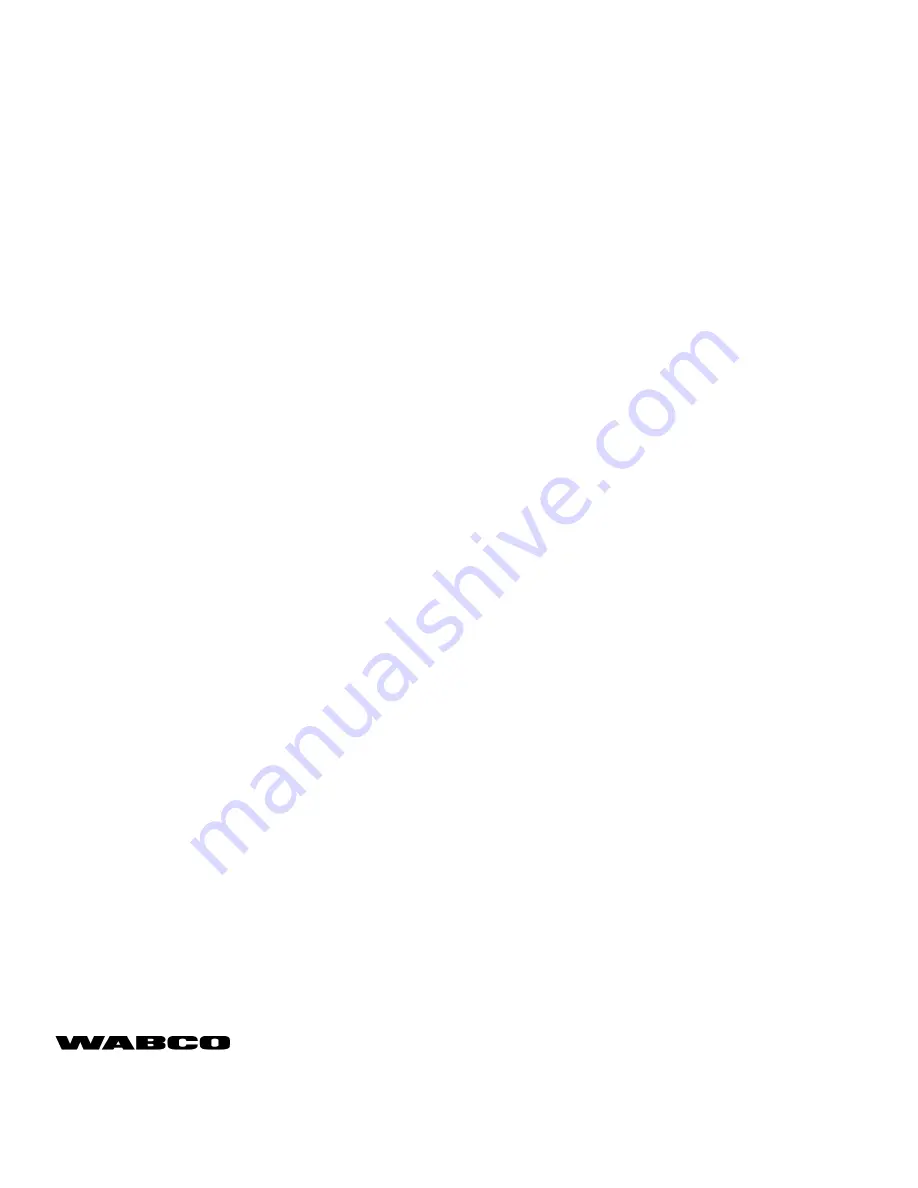
WABCO North America
1220 Pacific Drive
Auburn Hills, MI 48326 USA
855-228-3203
wabco-na.com
Information contained in this publication was in effect at the time the publication was approved for printing and is subject to
change without notice or liability. WABCO reserves the right to revise the information presented or to discontinue the
production of parts described at any time.
Copyright 2019
TP-0357
WABCO, Inc.
Revised 06-19
All Rights Reserved
Printed in USA
(16579)
Failed Primary System Function
If there is a loss of the primary system air, the valve will respond to
the remaining signal from the secondary brake system. When
secondary pressure increases to 10 psi (69 kPa), the valve will
begin to exhaust air from the spring brake chambers. The spring
brake chambers will be exhausted, fully applying the brakes, before
the secondary service pressure exceeds 75 psi (517 kPa). To test
this function:
1.
Place blocks under the tires to prevent the vehicle from
moving.
2.
Follow standard shop procedures to install a test gauge in the
delivery line of the valve or at the spring brake chamber.
3.
Fully charge the air brake system to 105-130 psi
(724-896 kPa).
4.
Drain the air from the primary reservoir.
5.
Make a service brake application by stepping on the foot valve.
This exhausts air from the spring brakes.
6.
Check the pressure reading. The test gauge should read 0
when the secondary service pressure exceeds 70 psi (483
kPa).
If the IR-2 valve does not function as described, check the
installation. Make sure all air lines are correctly routed. Check
the connections for leaks. Make the necessary repairs and
retest. If the problem persists, it may be necessary to replace
the valve. If you have any questions or need additional
assistance, contact the WABCO Customer Care Center at
855-228-3203.
Air Leakage
Replace the IR-2 valve if leakage exceeds 175 sccm.
NOTE:
If accurate measurement equipment is not available, replace
any valve that has a clearly audible air leak.
Leak Test
Perform a leak test to check for air leakage at the air line
connections.
1.
Place blocks under the tires to prevent the vehicle from
moving.
2.
Drain air from all system tanks.
3.
Close the reservoir drain cocks.
4.
Start the vehicle. Allow air system pressure to build to
cut-out pressure while the engine idles.
앫
If the vehicle is equipped with an air dryer:
There will be
a purge or strong blast of air from the air dryer, followed by
a mild flow which will last 10-25 seconds when cut-out
pressure is reached.
5.
Apply a soap solution to each connection that contains
pressurized air. Check the connections for soap solution
bubbles.
앫
No soap bubbles:
Connections are sealed.
앫
Soap bubbles:
Connections are not sealed.
Connection Seal Repair
To repair connection seals:
1.
Drain all reservoirs.
2.
Remove the leaking connection.
3.
Inspect the connections and ports for damaged threads or
cracks. Replace if necessary.
4.
Apply pipe sealant to the pipe thread connection.
NOTE:
Repeat the leak test until all connections are sealed.
Ensure that tubes are cut squarely to avoid damage to seals during
insertion into push-to-connect fittings.
Procedures
Valve Replacement
1.
Place blocks under the tires to prevent the vehicle from moving
2.
Identify, mark and disconnect all air lines from the valve.
3.
Remove the mounting hardware that holds the valve to the
vehicle.
4.
Remove the old valve from the vehicle.
5.
Install the replacement IR-2 valve. Refer to the installation
guidelines in this bulletin for installation instructions.
6.
Reconnect the pneumatic lines. Refer to Table A for more
information.
NOTE:
All lines must be reinstalled in the same location they
were in before they were removed. Refer to the vehicle
manufacturer’s service manual for complete instructions.
7.
Apply 105-130 psi (724-896 kPa) minimum air system
pressure. Test the installation, following the function tests
procedures in this bulletin.