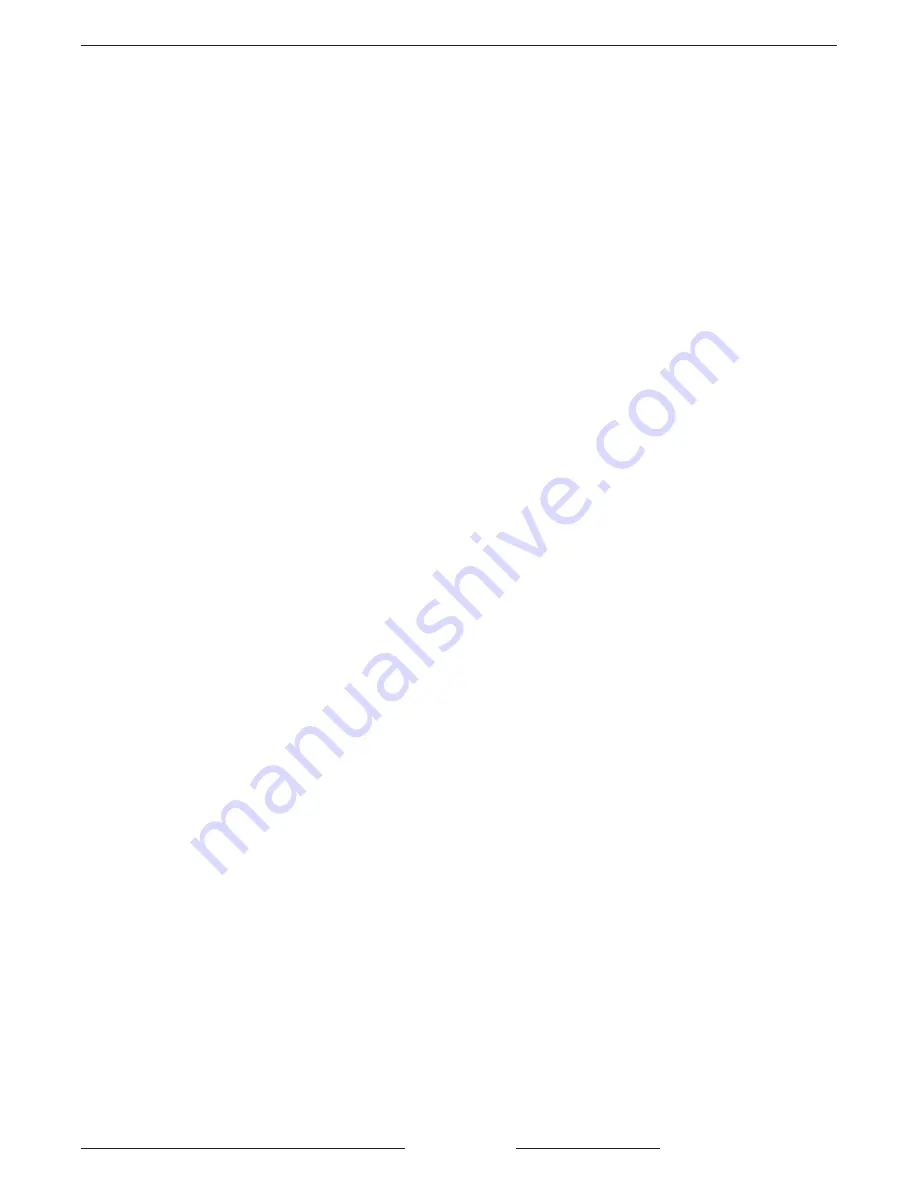
F35425 (February 2006)
Page 33 of 40
C24GA SERIES CONVECTION STEAMERS - TROUBLESHOOTING
General
The following paragraphs provide descriptive information
of the most common troubles that can occur in the
steamer. The Troubleshooting Chart provides a list of
other typical fault conditions. The left-hand column of
the table lists typical symptoms and the right-hand
column lists probable causes and the suggested
remedies.
Water Not Being Supplied to Generator
Turn the steamer on. Check that water supply is
available to the steamer. After approximately 10
minutes, if no water is present, then check for a
problem with the water solenoid valve or water level
control probe.
Scalants may be covering the water level control probe
giving a false indication of a sufficient water level in the
generator. Detach, remove and thoroughly clean the
water level probe assembly to remove scalants and lime
build-up. This condition indicates extremely poor water
quality being supplied to the generator and/or generator
clean out and deliming has not been performed. The
water condition must be cleared up immediately with a
proper water conditioner to avoid further problems with
the steamer. Replace the water level probes and
canister assembly. Water may be draining through an
open generator solenoid valve as quickly as it’s fed to
the generator. Particles of scale trapped in the genera-
tor solenoid valve seat may prevent the valve from
closing.
Pilot Or Main Burner Will Not Light
Check blower air pressure, air pressure switch adjust-
ment, pilot burner adjustment, gas inlet and manifold
pressures. The pilot burner orifice should be a 1/8" hole.
Drain Solenoid Valve Does Not Drain
The drain solenoid valve is normally closed when the
main power switch is in the on position. When the main
power switch is set to off, the solenoid valve is ener-
gized and the generator drain valve opens for 1000
seconds.
Water contained in the generator, being under pressure,
should be draining through this valve and be noticeable
exhausting out the steamer drain.
If the drain operation appears to function sluggishly or
not at all, scalants may be lodged in the drain pipe and/
or the valve. Disconnect the drain solenoid valve from
the drain line and inspect both the valve and the drain
pipe fixed to the generator. If considerable scalants or
lime build-up is apparent, then not only the drain
solenoid valve, but also the generator and water level
control must be thoroughly cleaned.
TROUBLESHOOTING
Water Accumulating in Compartment
Water accumulation on the bottom of the cooking
compartment(s) is primarily condensed steam. Failure
to drain out quickly and completely may be due to
debris in the compartment drain screen. Pull screen
straight out and thoroughly clean, then replace. Failure
to drain completely may also be due to improper
leveling of the steamer.
Cooking Cycle Cannot Be Activated
Inspect all wire terminals to ensure they are positive
and secure before assuming any other problem. When
the power switch on generator control box is in the on
position, set the timer knob to 2 minutes. Both Ready
lights should go off, Cooking lights should come on and
steam should be entering both compartments.
Steamer Achieves Pressure Slower Than Normal
If the generator requires more than 18 minutes to
achieve normal operating pressure of 3 – 4 psi, then
check the following conditions.
A.
A heavy build-up of scalants has possibly coated
the interior of the generator. The insulating effect of
the scalants hampers heat transfer. Unscrew and
remove the clean-out port plug on the bottom of
the generator. Using a small mirror examine
interior of generator and if scalants and/or lime
build-up is apparent, perform a generator clean-out
and deliming procedure (see DELIMING THE
GENERATOR). If considerable scalants are
evident, both the generator drain solenoid valve and
the water level control must also be examined.
B.
Low incoming gas pressure. Check the incoming
line and manifold gas pressures as outlined in
MANIFOLD PRESSURE ADJUSTMENT under
SERVICE PROCEDURES AND ADJUSTMENTS.
C.
Gas combination control valve malfunction. Check
the incoming and manifold gas pressures as
outlined in MANIFOLD PRESSURE
ADJUSTMENT under SERVICE PROCEDURES
AND ADJUSTMENTS.
If pressure adjustments are made and manifold pres-
sure remains low, replace the gas combination control
valve and test the steamer for proper operation.
D.
Gas orifice clogged or obstructed around air
shutter. It is possible for debris to become lodged
in the small gas orifice opening over time. Clean
out the gas orifice using a round metal instrument
of the same hole diameter or slightly smaller.
Clean as needed. If clogging reappears, the orifice
should be removed, cleaned, and reinstalled.
Remove any other foreign objects that appear to
be obstructing the gas orifice or air shutter.
Содержание C24GA10
Страница 39: ...F35425 February 2006 Page 39 of 40...
Страница 40: ......