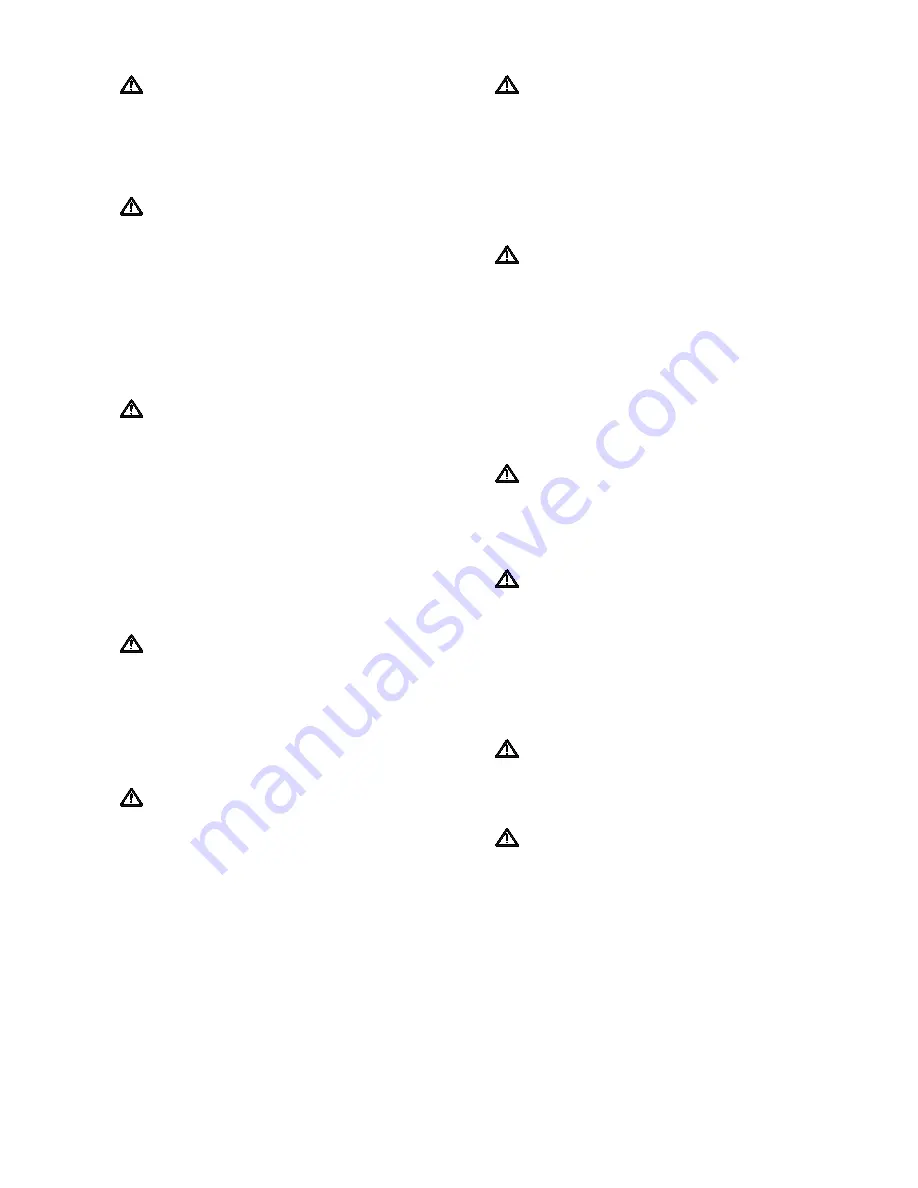
3
Always use protective goggles where there is a
danger of pieces of metal, sparks from grinding,
acid or other chemicals being thrown into your
eyes. Your eyes are very sensitive, injury can
lead to loss of sight!
Avoid skin contact with oil. Long-term or repeat-
ed contact with oil can remove the natural oils
from your skin. The result can be irritation, dry
skin, eczema and other skin problems. Used oil
is more dangerous to health than new oil. Use
protective gloves and avoid using oil-soaked
clothes and rags. Wash regularly, especially
before meals. Use the correct barrier cream to
prevent dry skin and to make cleaning your skin
easier.
Most chemicals used in products (engine and
transmission oils, glycol, petrol and diesel oil)
and workshop chemicals (solvents and paints)
are hazardous to health Read the instructions
on the product packaging carefully! Always fol-
low safety instructions (using breathing appar-
atus, protective goggles and gloves for ex-
ample). Ensure that other personnel are not
unwittingly exposed to hazardous substances
(by breathing them in for example). Ensure that
ventilation is good. Handle used and excess
chemicals according to instructions.
Be extremely careful when tracing leaks in the
fuel system and testing fuel injection nozzles.
Use protective goggles! The jet ejected from a
fuel injection nozzle is under very high pres-
sure, it can penetrate body tissue and cause
serious injury There is a danger of blood pois-
oning.
All fuels and many chemicals are inflammable.
Ensure that a naked flame or sparks cannot ig-
nite fuel or chemicals. Combined with air in cer-
tain ratios, petrol, some solvents and hydrogen
from batteries are easily inflammable and ex-
plosive. Smoking is prohibited! Ensure that ven-
tilation is good and that the necessary safety
precautions have been taken before carrying
out welding or grinding work. Always have a fire
extinguisher to hand in the workplace.
Store oil and fuel-soaked rags and fuel and oil
filters safely. In certain conditions oil-soaked
rags can spontaneously ignite. Used fuel and oil
filters are environmentally dangerous waste and
must be deposited at an approved site for de-
struction together with used lubricating oil, con-
taminated fuel, paint remnants, solvent, de-
greasing agents and waste from washing parts.
Never allow a naked flame or electric sparks
near the batteries. Never smoke in proximity to
the batteries. The batteries give off hydrogen
gas during charging which when mixed with air
can form an explosive gas - oxyhydrogen. This
gas is easily ignited and highly volatile. Incor-
rect connection of the battery can cause a
spark which is sufficient to cause an explosion
with resulting damage. Do not disturb battery
connections when starting the engine (spark
risk) and do not lean over batteries.
Never mix up the positive and negative battery
terminals when installing. Incorrect installation
can result in serious damage to electrical equip-
ment. Refer to wiring diagrams.
Always use protective goggles when charging
and handling batteries. The battery electrolyte
contains extremely corrosive sulfuric acid. If
this comes into contact with the skin, wash im-
mediately with soap and plenty of water. If bat-
tery acid comes into contact with the eyes, im-
mediately flush with copious amounts of water
and obtain medical assistance.
Turn off the engine and turn off power at main
switch(es) before carrying out work on the elec-
trical system.
Clutch adjustments must be carried out with the
engine turned off.
Содержание Aquamatic 250A
Страница 1: ...Workshop Manual Drive Aquamatic 250 C 2 0 ...
Страница 2: ......
Страница 26: ...24 Fig 34 ...
Страница 30: ...28 Fig 37 Transom ...
Страница 31: ...29 Fig 38 Upper gear housing ...
Страница 32: ...30 Fig 39 Intermediate housing ...
Страница 33: ...31 Fig 40 Lower gear housing ...
Страница 34: ...32 Fig 41 Extensions ...
Страница 36: ...7722840 1 English 01 1999 ...