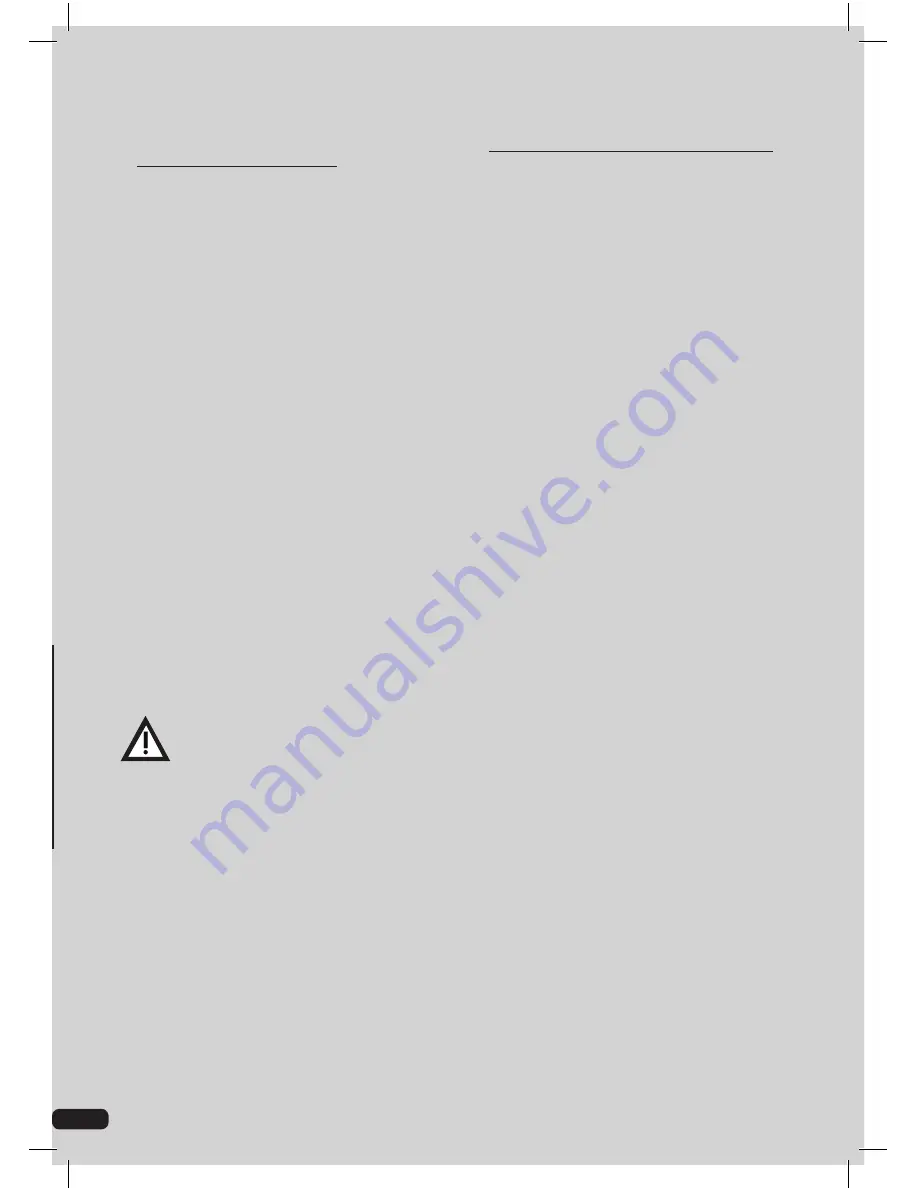
9
SPEED CONTROL
(pos.18 where fitted)
To regulate speed, use the regulator (pos.18 if present) according to the scale:
- low number = high speed
- high number = low speed
Follow any other information on the Angle Grinder and data sheet attachment.
We recommend repeating these operations several times before starting work, in order to familiarise yourself
with the controls as far as possible. If you notice any working defects, switch off the power tool and consult
the chapter ‘Problems, causes and solutions’. When not using the tool, turn it off and disconnect the plug
from the socket.
Tel: 01283 245430
ELECTRONIC SPEED REGULATION
(where fitted)
You need to assess the type of work, type, diameter and material of the part; perform tests at several speeds
on a scrap part before performing on real parts. In general set the speed according to the following chart,
depending of the type of work and accessory used. Also observe any information provided with the parts;
never exceed the maximum rotation speed indicated.
For the backing pad (pos.19) use only low speeds under 6,000 min-1.
WORKS
ACCESSORIES
MATERIAL OF THE
PART
High speeds
≥6000 min -1
<15000 min -1
Cut, Grind
Abrasive discs for
cutting and grinding
Metals Hardwood
Low speeds
>3000 min -1
<6000 min -1
Brush, polish, clean
Rotating brushes,
backing pad with
abrasive paper disc or
fabric disc
Coated surfaces,
plastic, softwood, heat
sensitive materials
CONTINUOUS OPERATION
For single and double-action switches, you can set the fixed switch to ‘ON-I’: when it is switched on, press
to block it. To deactivate this function and switch off, simply press ‘OFF-0’ for a short while and release
immediately. In the event the electricity supply is cut off, press the ‘OFF-0’ switch.
ABRASIVE DISCS
Purchase high quality abrasive discs which have the maximum external diameter indicated in the technical
details of the grinder, a suitable hole which fits the requirements of the flanges, and which are suitable for the
maximum speed of the grinder and the materials to be processed. Contact your retailer who will be able to
give you the best advice. Thorough use, discs wear thin, lose their calibration and expire after a certain date.
Always make a visual check before using and replace if necessary. For the assembly and replacement, go to
the ‘INSTALLATION- Abrasive disc assembly’ chapter. Handle and store the discs with care, do not subject
them to impact, bending, compression, moisture, high or low temperatures, and direct sunlight.
MAINTENANCE & SUPPORT
IMPORTANT! Before any checks or adjustment unplug the tool from the
electric power supply.
Have the maintenance operations carried out on power tools by qualified technical
personnel only using original spare parts.
This will allow the safety of the power tool to be
maintained.
Do not attempt to repair the power tool or to access internal parts.
Interventions by
unqualified personnel and unauthorised by the manufacturer could create serious risks and will
cause the warranty to be null and void.
The working life and costs also depend on constant and meticulous maintenance. Take good care of your
power tool and clean it regularly. In this way its efficiency will be ensured and its life span extended.
- Remove dust and machining residuals with a cloth or a brush with soft bristles.
- Do not wet or spray water over the power tool - risk of internal infiltrations.
- Do not use any inflammables, detergents or solvents.
- The plastic parts can easily be damaged by chemical agents.
- Do not use compressed air for cleaning: risk of material ejection!
- Be careful when cleaning the switch, motor fan slots and hand grips.
Protect the unpainted parts with protective oil and use the original packaging or case (where fitted) to
protect it.
STARTING AND STOPPING THE DEVICE
Single action switch:
- To start, press the ‘ON-I’ switch forward (pos.3).
- To stop, release the ‘OFF-0’ switch.
Double-action switch:
- To start, press the ‘ON-I’ switch down and then forward (pos.3)
- To stop, release the ‘OFF-0’ switch.
Switch with safety device:
- To start, in sequence press the safety device (pos.4) and then press the ‘ON-I’ (pos.3) switch.
- To stop, release the ‘OFF-0’ switch.
RE-ASSEMBLING THE FLANGES
(pos.8-10)
In the event both flanges have been removed, pay attention to the reassembling sequence:
1. Insert the disc hold flange (pos.8) into the threaded shaft; this flange has a contoured sear that must be
coupled with the contored shaft.
2. Screw the disc lock flange (pos.10) into the threaded shaft and tighten with the disc locking key.