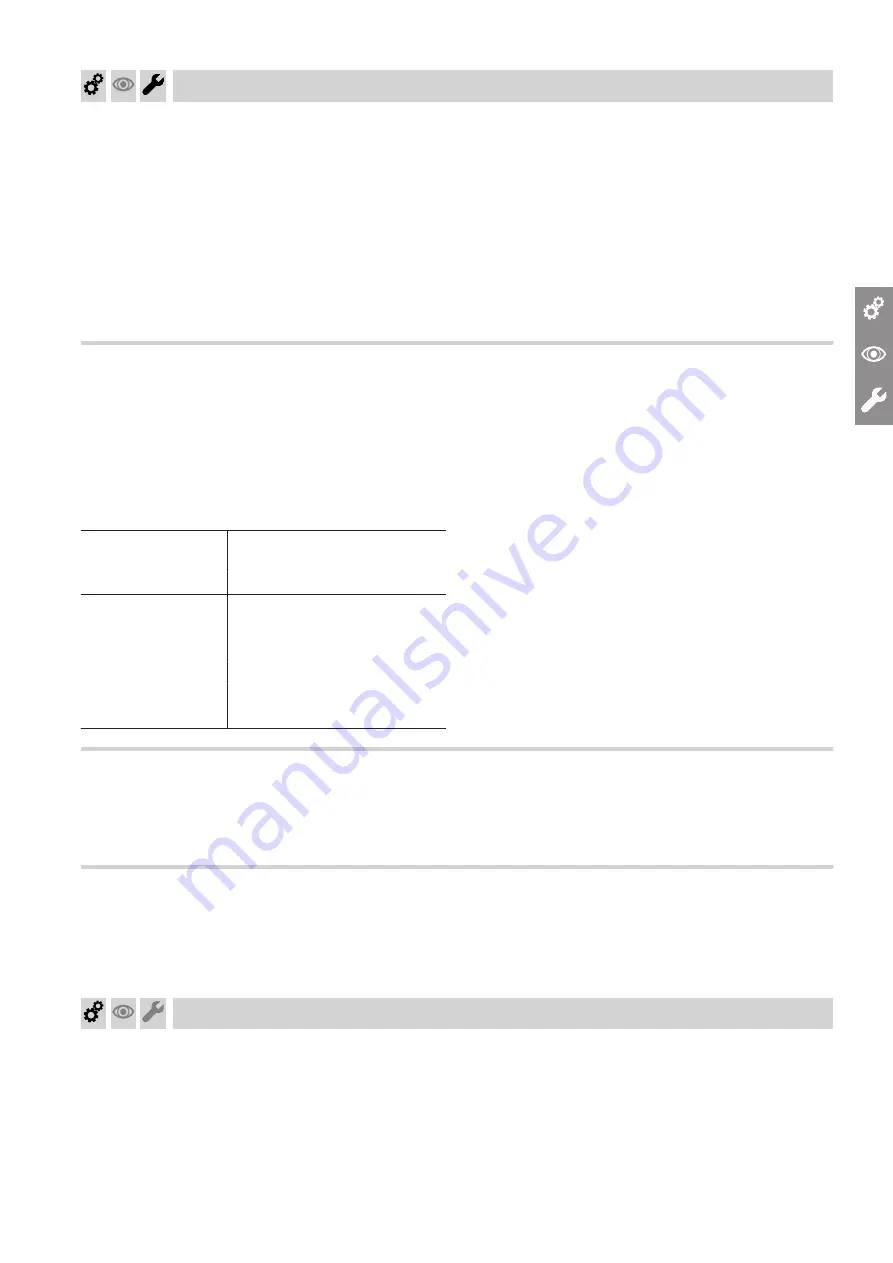
15
Partial load operation
Set the minimum heating output for the base load
stage in accordance with the flue system. The flue sys-
tem must be suitable for the low flue gas temperatures.
In the case of frequent cycling in standby mode and for
partial loads below 40 % we recommend that you:
■
Insulate the flue gas collector
■
Install a motorised flue gas damper
■
Set the minimum runtime of the boiler to 10 min
This extends the service life and reduces running
costs.
Operation with burner load
≥
60 %
The minimum boiler water temperature for oil operation
is 50 °C and for gas operation 60 °C.
Adjust the return temperature raising facility to a mini-
mum of 40 °C (oil operation) or 53 °C (gas operation).
To protect the boiler, the minimum heating output in the
base load stage is set to 60 % of the rated output (see
table).
Rated heating out-
put
Minimum heating output to
be set (burner stage 1)
kW
kW
700
420
900
540
1100
660
1300
780
1600
960
1950
1170
The base load stage requires a minimum flue gas tem-
perature, the value of which is subject to the design of
the flue system.
Operation with burner load
≥
40 % and < 60 %
The minimum system temperatures (flow/return) are
60/50 °C for oil operation and 70/60 °C for gas opera-
tion.
Operation with burner load < 40 %
The minimum system temperatures (flow/return) are
60/55 °C for oil operation and 70/65 °C for gas opera-
tion.
Instructing the system user
The installer should instruct the user in the operation of
the system.
Commissioning, inspection, maintenance
Adjusting the burner
(cont.)
5692849