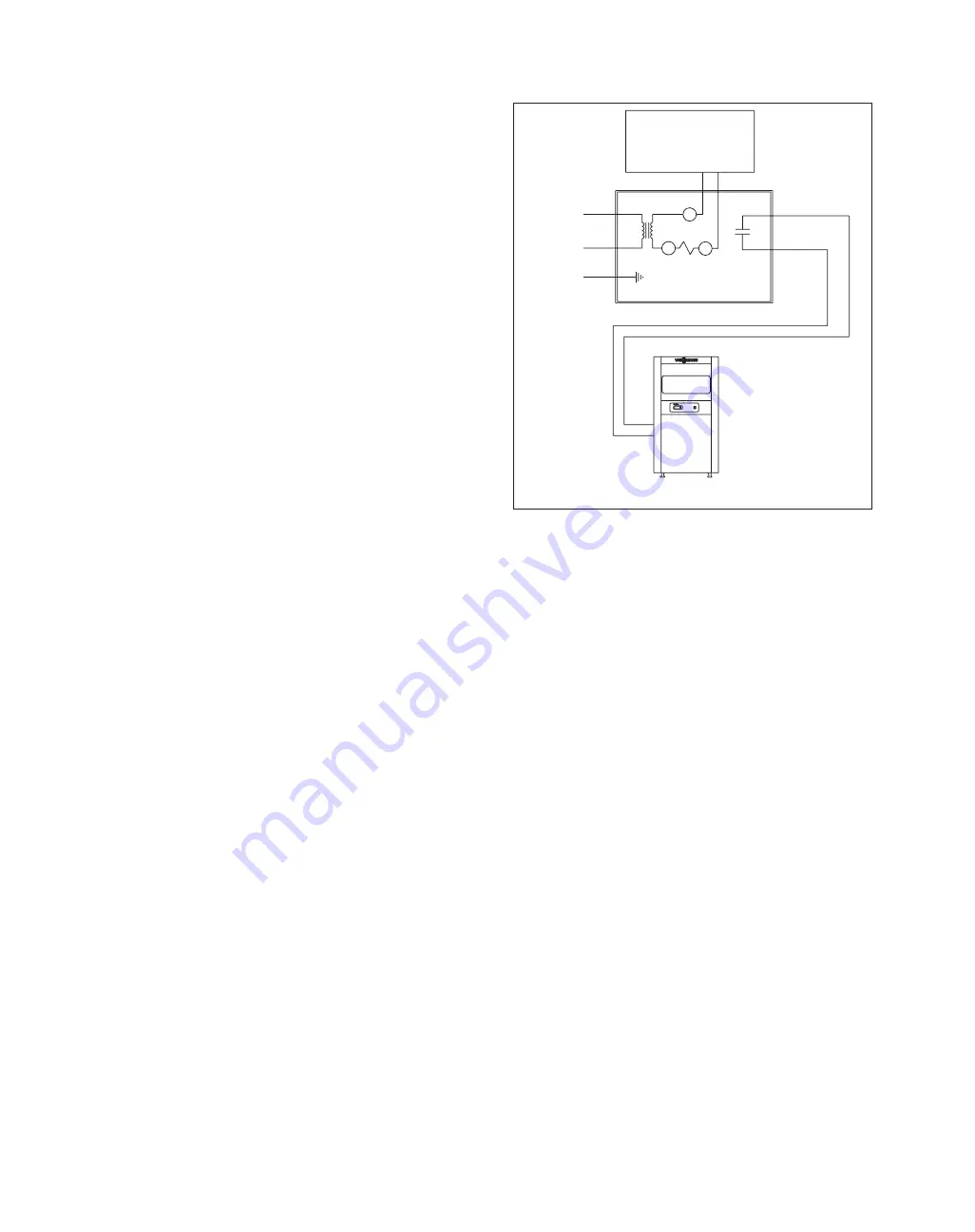
If an external electrical source is utilized, the boiler, when
installed, must be electrically grounded in accordance with the
requirements of the authority having jurisdiction or, in the
absence of such requirements, with the National Electrical
Code, ANSI/NFPA 70.
Boiler electrical requirements are 120V, 60 Hz, less than 12A.
The thermostat connections on the boiler must be connected
to a potential-free (or “dry”) contact such as a room thermostat,
end switch of a zone valve or dry contact of an indoor/outdoor
control.
See wiring diagram in rear of manual and wiring label on
boiler. Viessmann reserves the right to substitute electrical
components as necessary. The boiler wiring label takes
precedence.
Caution
Label all wires prior to disconnection when servicing controls.
Wiring errors can cause improper and dangerous operation.
Verify proper operation after servicing.
Electronic thermostat connection
For those installations where an electronic set-back thermostat
is used, an isolation relay may be necessary (see Fig. 9g). Any
electronic thermostat that constantly requires current from the
boiler transformer will require an isolation relay. For example
when installing a Honeywell Chronotherm, use an isolation
transformer relay (as shown in Fig. 10) to provide current for
the electronic thermostat.
System start-up procedure
If the system was shut down for an extended period of time,
have a qualified service technician restart and recondition your
system. Refer to lighting instructions on page 18.
1.
Check if all national and/or local rules and regulations
have been adhered to on this installation. Do not attempt
to start the boiler if you smell gas. If you smell gas, open
windows. Do not touch electrical switches, extinguish any
open flame, close all gas valves immediately. Call your
gas supplier immediately from a neighbor’s phone.
2.
Check system for proper water fill (cold fill pressure).
Make sure that complete system is properly vented of air.
Adjust automatic feed valve to proper desired fill pressure
between 12-15 psig.
Do not tamper with the unit or controls.
Never burn garbage or paper in the unit or leave
combustible materials around it.
Additional attention must be given to the following
paragraphs
1.
Once system water is heated, deactivate circulating
pump/boiler and vent system of any remaining air within
piping, radiation and boiler.
2.
Check for proper boiler circulation, pump, zone valve,
thermostat or operating control functions.
3.
Check high limit aquastat by dialing it to a setting below
the water temperature in the boiler. The gas burner must
be deactivated. Turning the dial back to a setting higher
than the present boiler water temperature must result in
reactivation of gas burner.
4.
Cycle boiler on and off with the room thermostat (or other
operating control) to verify that the burner shuts down when
the room thermostat is adjusted below room temperature.
Annual shut-down
If boiler is used for comfort heating only and not used with an
indirect-fired domestic hot water storage tank, the
boiler/heating system should be shut down during the summer
time.
1.
Turn down operating control (thermostat).
2.
Disconnect main power switch.
3.
Close main gas shut-off valve and turn knob on gas valve
to “off” (see Figs. 6 and 7).
ATTENTION
If system is shut down during the heating season and subject
to freezing temperatures and is not filled with antifreeze for
protection, the system including the boiler must be drained of
water. Valve before automatic feed valve (if installed) must be
closed; any other valves, air vents and drain valves must stay
open.
Advise the operator/ultimate owner
1.
Of the proper system operation sequence.
2.
Explain the equipment as well as the need for
combustion air.
3.
Demonstrate an emergency shut-down, what to do and
what not. Refer to lighting instructions on page 18.
4.
Explain that there is no substitute for proper maintenance
to help ensure safe operation.
Before leaving jobsite
Fill in and sign warranty card for boiler and hand over to owner
for record keeping.
Maintenance
Inspections during heating season
15
Fig. 10
Isolation relay for electronic thermostat
Honeywell
Chronotherm
electronic set-back
room thermostat
H
N
G
WR 8A02A-8
Isolation transformer relay
R
C
G
To boiler
thermostat
connections
T-T on
terminal strip
120V
24V