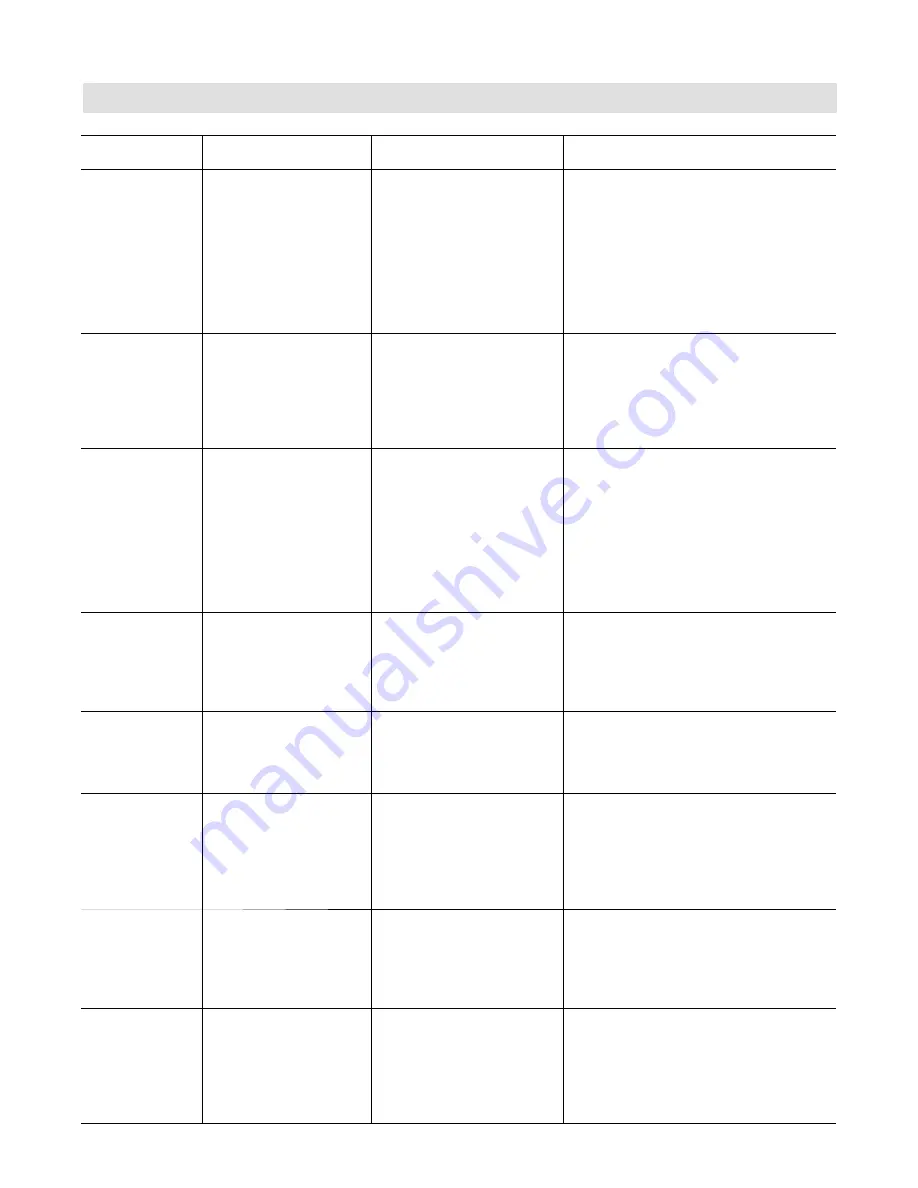
21
5603 884 - 04
Vitoflex 300-UF Service & Maintenance
System Faults
Text for error
shown on display
Indicator
Possible cause
Check / remedy
Excess
temperature, lack
of water, water
pressure
- Fixed high limit at the
top of the boiler (N21)
- Low water cut off (N22)
- Pressure monitor (N23)
- Incorrect set-point adjusted
on the control module
(either the boiler set-point
temperature or the cycle
for “In-feed Auger” is too
high)
- Defective component
..
(pump or valve)
- Sudden output drop to zero
- Why couldn’t the heat be transferred?
- Check the boiler pump and mixing valve
- Reduce the cycle for “In-feed Auger”
(see the Installation and Operating
Instructions)
- Take off the protective cap from the
fixed high limit and press the reset
button (this is only possible at boiler
temperatures less than 158°F (70°C)
- Acknowledge in Screen 2
Underfeed pipe
is hot
- Temperature sensor
on the in-feed auger
(B02)
- Power failure
- Consequent malfunction,
caused by excess temperature
- Light barriers for ember
monitoring system are soiled
- Cycle for “Sustain Embers”
is set too low
- Call a qualified electrician
- Check light barriers at the embers
- Set cycle higher for “Sustain Embers”
(see the Installation and Operating
Instructions)
- Acknowledge in Screen 2
Malfunction,
excess pressure
in combustion
chamber
- Negative pressure
monitoring assembly
on the combustion
chamber (N70)
- Flue gas exhaust blower is
broken
- Boiler is very soiled
- Ash container has been
removed or is mounted
incorrectly
- Check flue gas exhaust blower
- Clean boiler
- Check mounting of ash container
- Reset negative pressure monitoring
assembly (N70) (on the fixed high limit
for the combustion chamber, take off
the protective cap and press the reset
button - this is only possible at boiler
temperatures less than 158°F (70°C)
- Acknowledge in Screen 2
Malfunction,
low pressure
measured in
combustion
chamber
- Negative pressure
gauge (B70)
- Flue gas exhaust blower is
broken
- Boiler is very soiled
- Ash container has been
removed or is mounted
incorrectly
- Check flue gas exhaust blower
- Clean boiler
- Check mounting of ash container
- Acknowledge in Screen 2
Malfunction,
measurement
of combustion
chamber negative
pressure
- Negative pressure
gauge (B70)
- Flue gas exhaust blower is
broken
- Boiler is very soiled
- Check flue gas exhaust blower
- Clean boiler
- Acknowledge in Screen 2
Malfunction,
frequency
converter for
flue gas exhaust
blower
- Frequency converter for
flue gas exhaust blower
(U1)
- Check the error
indication on the
frequency converter
in the control cabinet
- Overload of flue gas
exhaust blower motor (M1)
- Turn off main switch
- Check flue gas exhaust blower
for smooth running
- Acknowledge in Screen 2
Malfunction,
frequency
converter for
Primary air
blower
- Frequency converter for
primary air blower (U12)
- Check the error
indication on the
frequency converter in
the control cabinet
- Overload of one of the
Primary air blower motors
(M12.1, M12.2, and
Primary -3 blower: M12.3)
- Turn off main switch
- Check primary air blower for smooth
running
- Acknowledge in Screen 2
Malfunction,
frequency
converter for
Secondary air
blower
- Frequency converter for
secondary air blower
(U13)
- Check the error
indication on the
frequency converter
in the control cabinet
- Overload of the Secondary
air blower motor (M13)
- Turn off main switch
- Check secondary air blower for smooth
running
- Acknowledge in Screen 2
Troubleshooting Guide