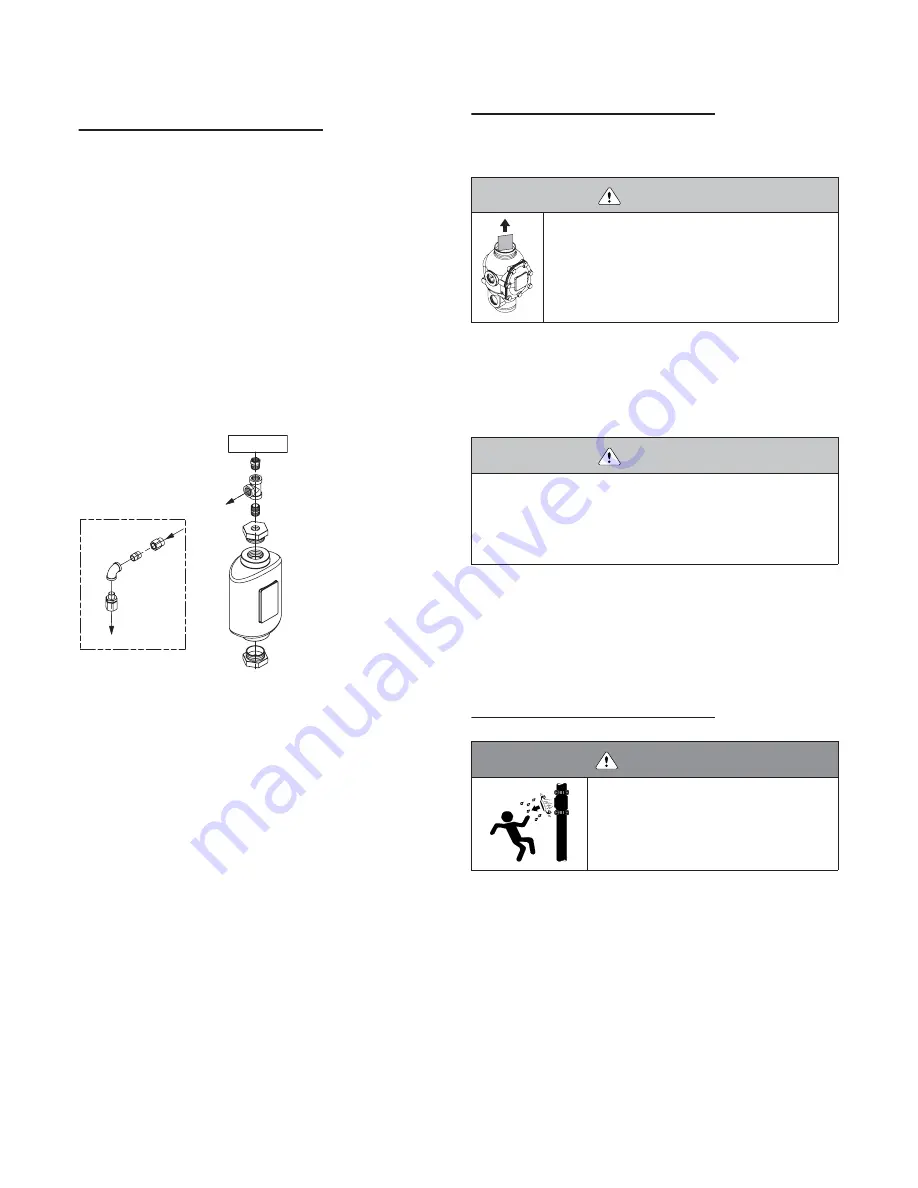
Series 751 FireLock® Alarm Check Valve
8
IMPORTANT INSTALLATION
INFORMATION
1.
For proper operation and approval, the Series 751 Alarm Check
Valve must be installed in accordance with the specific trim diagrams
included in the shipment.
NOTE:
Victaulic provides specific trim dia-
grams for vertical and horizontal installations.
2.
Before installing the Series 751 Alarm Check Valve, flush the
water supply piping thoroughly to remove all foreign material.
3.
Series 751 Alarm Check Valves
MUST NOT
be located in an area
where the valve can be exposed to freezing temperatures. In addition,
the Series 751 Alarm Check Valve
MUST NOT
be located in an area
where physical damage may occur.
4.
It is the owner’s responsibility to confirm material compatibility of
the Series 751 Alarm Check Valve, trim, and associated accessories
when a corrosive environment or contaminated water is present.
5.
The Victaulic Series 752 Retard Chamber should be installed in
variable pressure installations.
NOTE:
Victaulic provides specific trim
drawings for installations that involve a Series 752 Retard Chamber.
6.
The Series 752V Retard Vent Kit is required any time an air break
is needed above the retard chamber. In addition, the Series 752V
Retard Vent Kit is required if multiple valves are tied into one water
motor alarm and a check valve isolates each line. Refer to the drawing
above.
7.
Series 751 Alarm Check Valves can be installed in the vertical
position with the arrow on the body pointing upward. The arrow on the
swing check valve in the bypass line must point upward.
8.
When installed horizontally, the cover plate must face up-
ward. The arrow on the swing check valve in the bypass line must
match the direction of the water flow.
9.
When the Series 751 Alarm Check Valve is used with a water
motor alarm, it is recommended that the valve contain an uninterrupted,
low-pressure alarm that is installed on the piston charge line down-
stream of the check valve.
VALVE/TRIM INSTALLATION
1.
Make sure trim drawings match system requirements. Refer to
page 7 for the listing.
2.
Remove all plastic caps and foam spacers from the valve.
3.
Apply a small amount of pipe joint compound or Teflon* tape to
the external threads of all threaded pipe connections. DO NOT get any
tape, compound, or other foreign material in the valve body, pipe nip-
ples, or valve openings.
4.
Install the valve, trim, and accessories per the trim drawing.
* Teflon is a registered trademark of the Dupont Company
HYDROSTATIC TESTING
The Victaulic Series 751 Alarm Valve is UL Listed and FM Approved for
a maximum working pressure of 300 psi (2065 kPa) for 1
1
/
2
- 6-inch (40
– 150-mm) sizes and 225 psi (1551 kPa) for the 8-inch (200-mm) size.
The valve is factory tested to 600 psi (4135 kPa) for 1
1
/
2
- 6-inch (40 –
150-mm) sizes and 500 psi (3447 kPa) for the 8-inch (200-mm) size. The
valve can be hydrostatically tested against the clapper at 200 psi (1380
kPa) or 50 psi (345 kPa) above the normal water supply pressure (2-
hour limited time period) for acceptance by the authority having
jurisdiction.
Optional Series 752V
Retard Vent Kit
To Water Motor
Alarm or Optional
Restrictor
Optional Pressure
Switch
Pipe to
Open Drain
CAUTION
• Make sure the foam spacer is removed from inside
the valve body before attempting to install the valve.
Failure to follow this instruction could cause improper
valve operation, resulting in personal injury and/or
property damage.
CAUTION
• Make sure no foreign material gets into the valve body, pipe nip-
ples, or valve openings.
• If using any material other than Teflon tape, use extra caution so
that no material gets into the trim.
Failure to follow these instructions could cause improper valve
operation and/or property damage.
WARNING
• If air testing is required, DO NOT exceed 50-
psi (345-kPa) air pressure.
Failure to follow this instruction could result in
serious personal injury and/or property dam-
age.