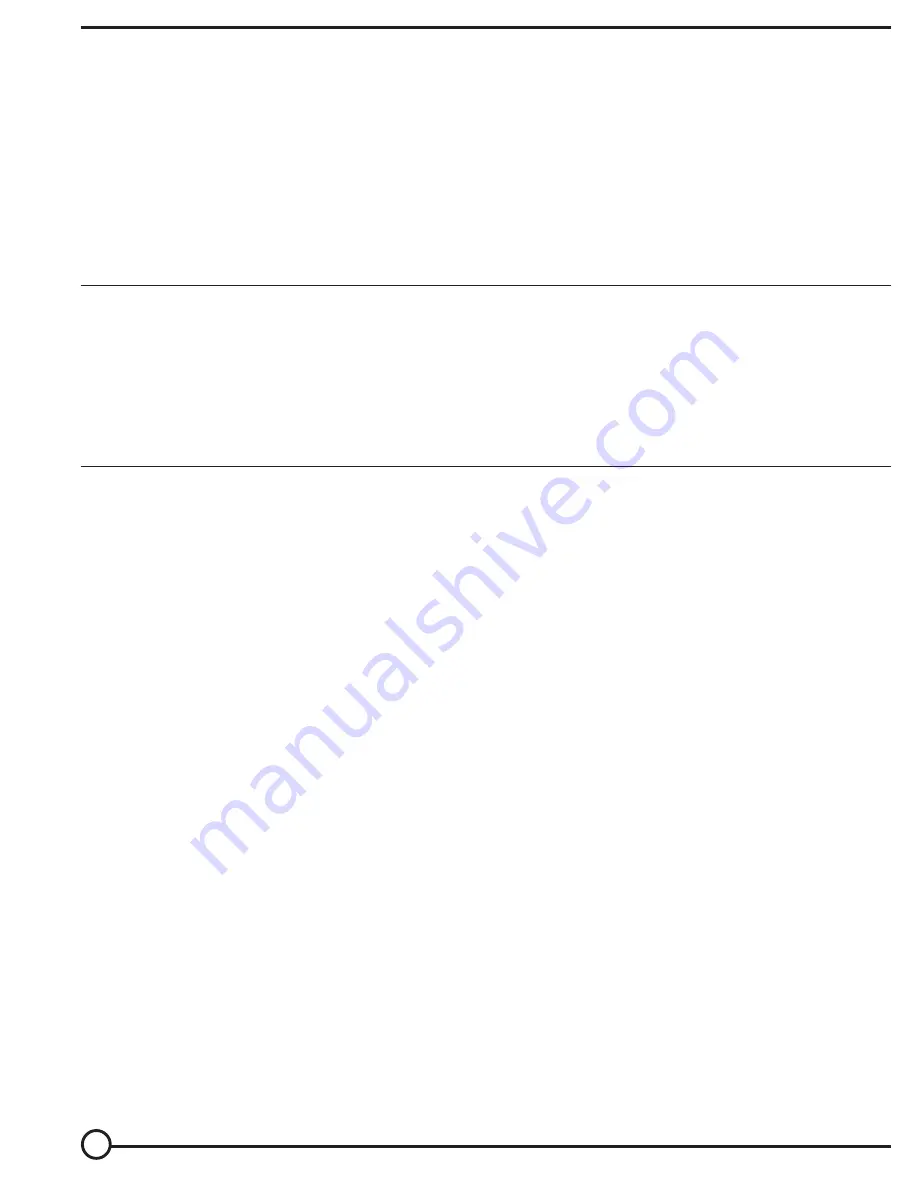
INSTALLATION INSTRUCTIONS – EHLTG
Review this entire page before installing the ground-clearance scissor lift.
Consult the factory in the event there are any questions or problems at the time of installation, or for
information regarding optional features not covered by the owner’s manual.
The lift must be removed from the shipping wood and securely anchored to the floor before use!
• Modifications or additions made without prior manufacturer’s authorization may void the lift’s warranty. The addition of
ancillary equipment to the lift may necessitate that its load capacity be reduced.
• The installation must be made so that it complies with all the regulations applicable to the machine and its location. The
end-user must verify that the supplied equipment is installed so it will be suited to the environment in which it will be
used.
• Installation must be performed by suitably trained personnel with access to the appropriate equipment. The electrical
aspects of the installation should be performed by an electrician.
For a typical installation you will need the following:
1. A fork truck or hoisting means to unload the lift from the freight truck and set it into place.
2. A smooth, level, and adequately strong concrete surface on which to mount the lift.
3. Concrete anchors, a masonry drill, a masonry bit, hand tools, grout, and steel shims. Consult the building’s architect or
facility engineer to determine the best size and type of hardware with which to anchor the machine to the floor.
4. A power supply circuit and disconnect matching the motor voltage and current requirements. Refer to the machine’s
dataplate, to the labels on the control enclosure, and to the electrical section in this manual for more information.
The end-user is responsible for supplying the branch circuit’s required overcurrent and short-circuit protection, which
typically can be a 20A (maximum) inverse-time circuit breaker.
1. The lift must be lowered and fully supported. Move the lift into place with straps or forks placed underneath both the
frame and the platform. Use care to avoid damage to the electrical or hydraulic components from the remotely-
located power unit attached at the operator’s side of the lift.
2. Temporarily connect the power supply to the pigtail cord supplied with the power unit, and raise the platform so the
lift’s safety maintenance props can be utilized. Lower the platform so the legset is supported on the maintenance
props.
3. Anchor the frame to the floor through the 9/16” holes located at the corners of the frame.
4. Shim and/or grout under the full length of the frame sides.
5. Make permanent connection to the power supply, using an appropriate wiring method.
6. Operate the lift through several full up and down cycles. Verify that the upper travel limit switch (mounted in one side
of the leg set) and the toe guard switch (at one end of the toe guard bar, across the loading side of the platform)
function properly.
7. Check the remote power unit’s hydraulic oil level. It should be filled to within 1” to 1½” of the reservoir’s fill hole. If
oil is needed, use an anti-wear hydraulic oil with a viscosity grade of 150 SUS at 100°F (ISO 32 at 40°C) or a non-
synthetic automatic transmission fluid.
8. Clean up any debris or spilled oil, and verify that all of the warning and safety labels are intact.
• If the platform must be raised without first having the proper power supply connected, raise the platform at the end of
the lift to which the electrical cord and hydraulic hose attaches. Use a lifting hook on each side, attached near the
deck hinges. With this method, the frame must be held down at the hinged end of the lift while the platform is raised.
2
Содержание EHLTG
Страница 6: ...MOTOR TRANSFORMER CONNECTION DIAGRAMS 6 ...