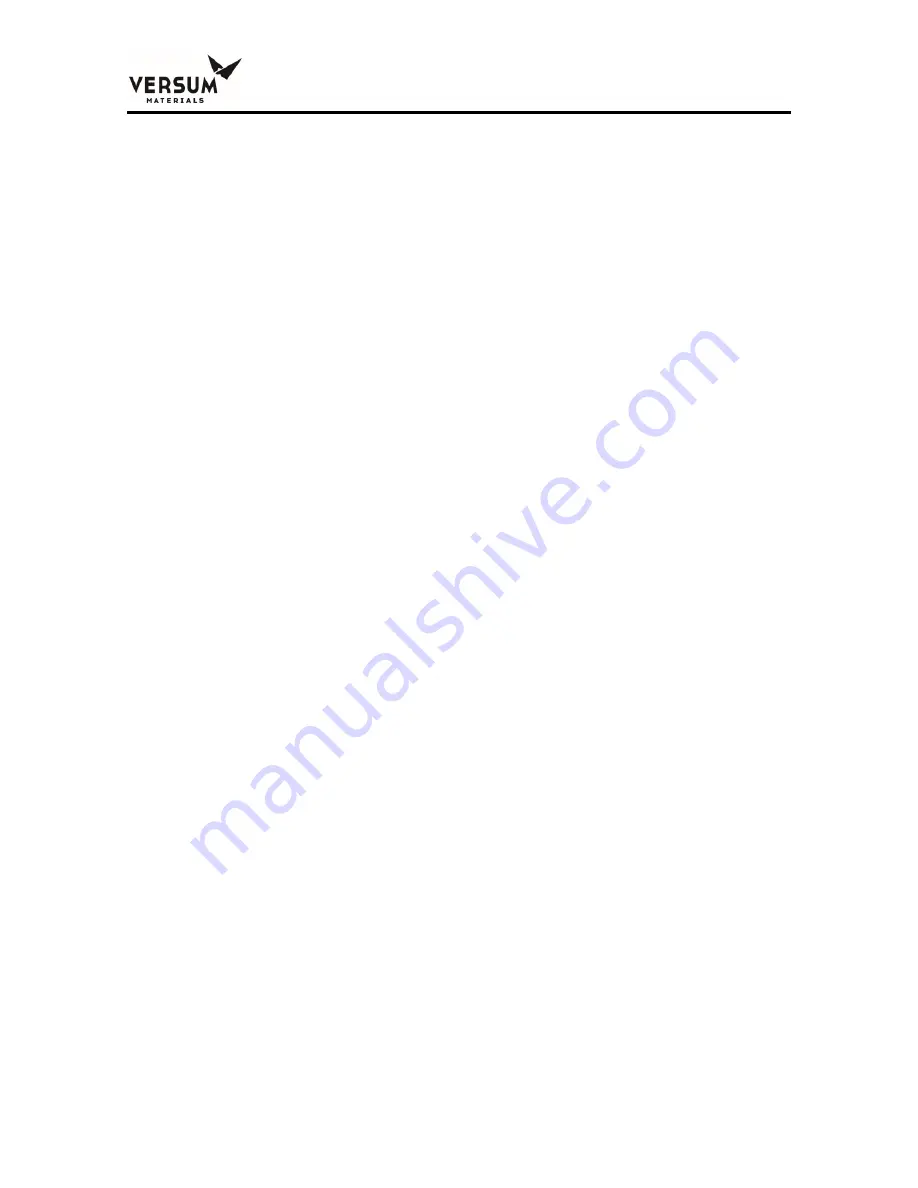
Chapter 3 - Installation
MNL000624.doc
Revision 0
06/25/2019
Chemical Equipment
© Versum Materials US, LLC. as of the revision and date shown. All rights reserved.
Confidential and Proprietary Data
Page 3
-
14
Versum Materials Confidential
with a potential spark source. Provided that these components are purged and
pressurized at a flow of 25 scfh, the risk of spark is eliminated.
Every ChemGuard® shipped has z-purge enabled and can be installed in
hazardous areas.
3.6.8
Z-Purge Setup
A Z-Purge flow valve is located on the right rear of the controller and can be
adjusted via the penetration into the ChemGuard® cabinet between the pneumatic
control bulkheads.
The flow valve controls the flow of the house nitrogen to the controller interior. Its
use may be required in certain areas (i.e. Class I, Division II designated areas in
the U.S.A. or Group II, Category 3 areas in the European Community.)
There are three pressure switches located within the cabinet. There is one switch
in the controller housing, one in the upper cabinet door and one in the interface
box to ensure adequate pressure (
0.1" H2O) during the Z-purging. Low Z-purge
alarms will be triggered if pressure falls below the pressure adjustment in the
pressure switches. The nitrogen flow must be increased until the alarms can be
reset.
The Z purge pressure is controlled by a needle valve at the base of the controller.
After opening the controller in a suspected hazardous area it is necessary to use
the following procedure to re-establish the Z-purge before operating the controller:
1. Close the controller front and tighten both latches completely.
2. Open the needle valve 4 to 5 turns (counter-clockwise). Allow the controller
to purge for 30 minutes.
3.
Adjust needle valve to satisfy all three of the “Z-Purge” alarm
(approximately 2 total turns open).
Flow requirements to operate the solenoid valves are very small, less than 1 LPM
(2 CFH). If Type Z purge is required, a minimum flow rate of 5.5 SLPM will be
needed, depending on the tightness of the individual controller and the installation.