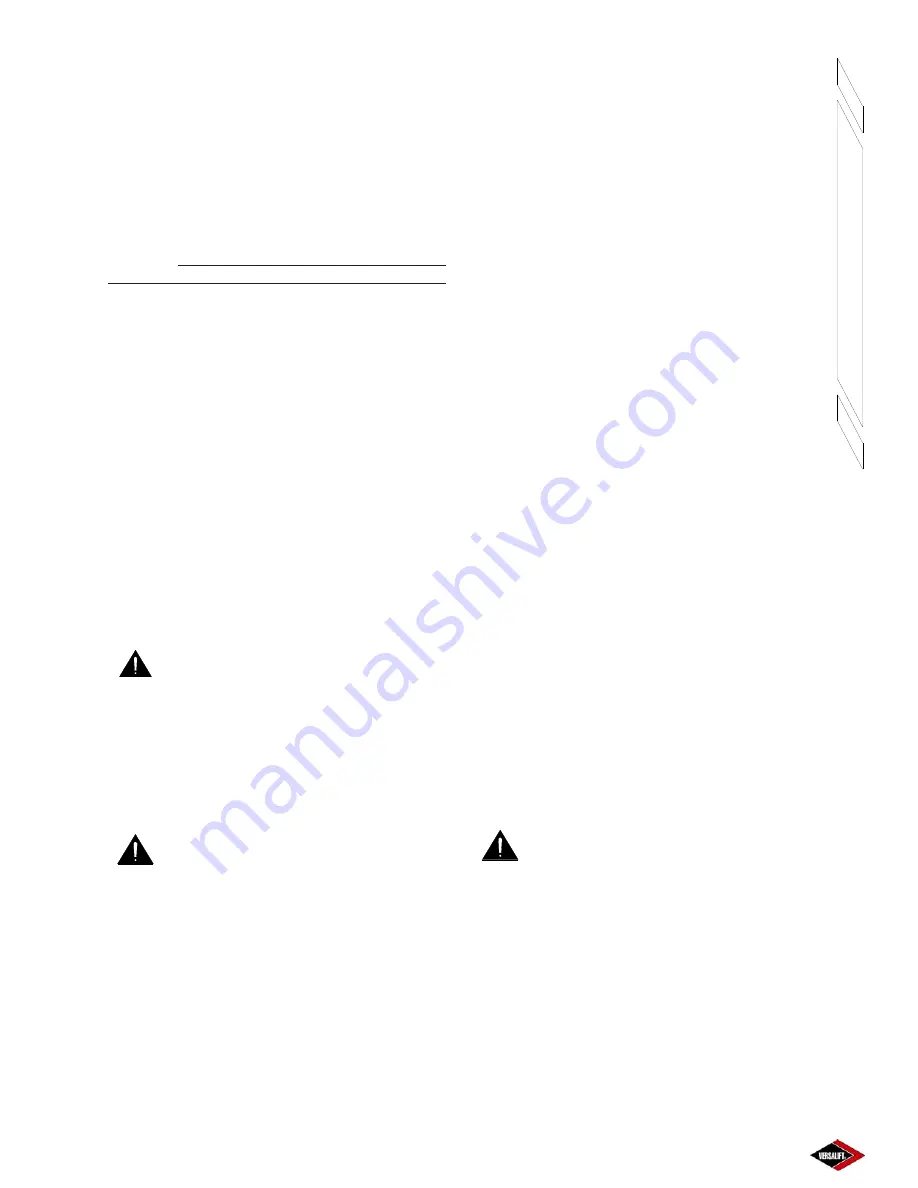
4-7
39049-01 01/17
VERSALIFT VO-452/455/460-MHI
OPERA
TION
To slow the engine to an idle from the pedestal
,
push the toggle to the “DISENGAGE” position. Allow
the toggle to return to the centered or neutral position.
BACKUP PUMP CONTROL (Option)
- If the aerial
lift main power source fails, the backup pump option
can be activated to operate the lift. The backup pump
control is a detented toggle switch located at the
pedestal. The backup pump system should not be
operated longer than 30 seconds continuously.
Continuous use will drain the battery and damage (over
heat) the backup pump motor.
To activate the backup pump from the pedestal
,
push the toggle switch to the “ON” position and operate
the appropriate lift controls.
To deactivate the backup pump from the
pedestal
, push the toggle switch down (towards the
“30 SECOND INTERMITTENT” message).
UPPER CONTROL OPERATION
This section describes how the operator can identify
and operate the upper controls (at the dual platforms).
Never allow an untrained individual to operate the aerial
lift.
DANGER:
AN UNTRAINED OR
CARELESS OPERATOR SUBJECTS HIM/
HERSELF AND OTHERS TO DEATH OR SERIOUS
INJURY.
When operating the lift all lift movements must be
started and stopped gradually.
DANGER:
NEVER REVERSE OR STOP
THE DIRECTION OF THE LIFT TRAVEL SUDDENLY
AND AVOID REACHING THE END OF THE BOOM
TRAVEL AT EXCESSIVE SPEEDS.
STRUCTURAL
DAMAGE OR INSTABILITY MAY RESULT
CAUSING DEATH OR SERIOUS INJURY.
Never operate the upper controls without using the
personnel restraint system.
Speed and smoothness of lift operation are controlled
by feathering the control valves. Feathering a control
function allows the operator to change the speed by
adjusting how far the control is moved. Flow can be
directed to one function or multiple functions
simultaneously. Function speed depends on flow to
each valve. Regular practice will develop operator
proficiency.
SINGLE STICK CONTROL
- Refer to Figure 4.6 for
clarification. This multi-jointed handle operates the
valve spools and enables the operator to control all
lift movements. The three bi-directional handle
movements (in-out, up-down, and right-left) are
illustrated on the placard mounted on top of the single
stick control.
Lift operations are selected by depressing the safety
trigger while actuating the single stick control handle.
Slowly move the single stick handle in the desired
direction until motion begins. Further movement of
the handle in the same direction will increase the
speed of the motion. To stop a lift movement, move
the single stick lever back to the neutral position and
release the trigger. Releasing the safety trigger in
any position except neutral will cause the selector
valve to slam shut and stop lift travel with an abrupt
jerking motion resulting in unnecessary loads and
stresses.
To operate two or more functions at the same time,
position the single stick handle anywhere in an area
between the separate paths of the desired functions.
HYDRAULIC TOOL POWER (Standard)
- The
hydraulic tool ports are located on the side of the
upper controls. Always relieve the pressure to the
tool ports before connecting or disconnecting the
hydraulic tool hoses. To relieve the pressure, move
the tool selector handle to the “OFF” position. Then
connect or disconnect the hydraulic tool hoses to the
tool ports. (Quick Disconnect Outlets). Activate
operating pressure to the hydraulic tools by moving
the tool selector to the “ON” position.
WARNING:
FAILURE TO RELIEVE
PRESSURE TO THE TOOL PORTS BEFORE
CONNECTING OR DISCONNECTING THE
HYDRAULIC TOOL HOSES MAY RESULT IN A
HIGH PRESSURE HYDRAULIC OIL SPRAY. THIS
SPRAY OR MIST CAN PUNCTURE OR BECOME
EMBEDDED BENEATH THE SKIN OR
CONTAMINATE THE EYES. THESE CONDITIONS
REQUIRE IMMEDIATE MEDICAL ATTENTION.
EMERGENCY STOP (Standard)
- The primary
purpose of the emergency stop valve is to deactivate
all the upper controls in the event of a control valve
malfunction (i.e. a valve spool stuck in the open
position) or other hydraulic emergency. Push the
Содержание VO-452-MHI
Страница 2: ......
Страница 4: ......
Страница 6: ......
Страница 8: ...1 2 39049 01 01 17 VERSALIFT VO 452 455 460 MHI INTRODUCTION ...
Страница 11: ...2 3 39049 01 01 17 VERSALIFT VO 452 455 460 MHI RESPONSIBILITIES SAFETY ...
Страница 12: ...2 4 RESPONSIBILITIES SAFETY 39049 01 01 17 VERSALIFT VO 452 455 460 MHI ...
Страница 18: ......
Страница 24: ...3 6 39049 01 01 17 VERSALIFT VO 452 455 460 MHI SPECIFICATIONS ...
Страница 25: ...3 7 39049 01 01 17 VERSALIFT VO 452 455 460 MHI SPECIFICATIONS ...
Страница 26: ...3 8 39049 01 01 17 VERSALIFT VO 452 455 460 MHI SPECIFICATIONS ...
Страница 28: ...3 10 39049 01 01 17 VERSALIFT VO 452 455 460 MHI SPECIFICATIONS ...
Страница 44: ......
Страница 48: ...6 4 39049 01 01 17 VERSALIFT VO 452 455 460 MHI DAILY VISUAL INSPECTION ...
Страница 49: ...6 5 39049 01 01 17 VERSALIFT VO 452 455 460 MHI DAILY VISUAL INSPECTION ...
Страница 50: ...6 6 39049 01 01 17 VERSALIFT VO 452 455 460 MHI DAILY VISUAL INSPECTION ...