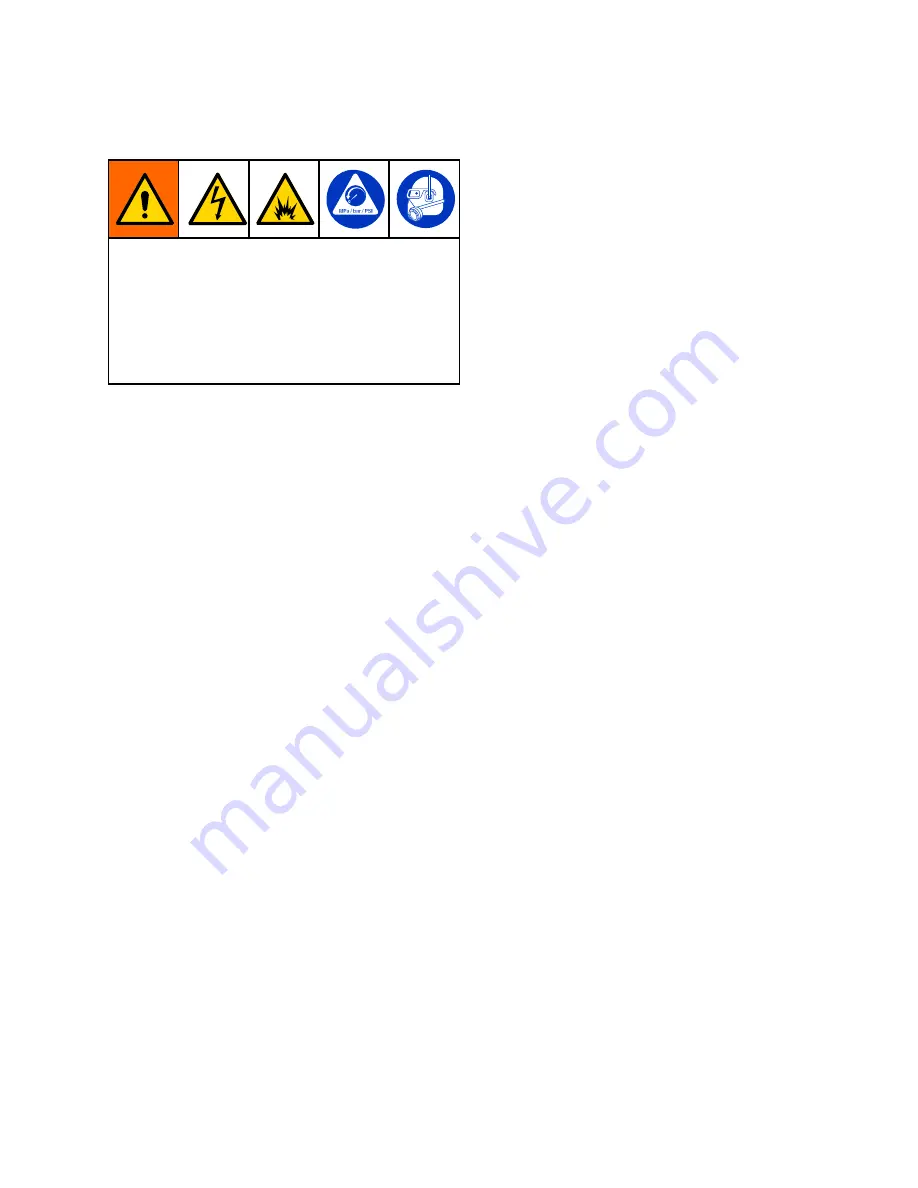
Installation
Installation
Installation
Installation of this equipment involves potentially
hazardous procedures. Only trained and qualified
personnel who have read and who understand
the information in this manual should install this
equipment.
• All electrical wiring must be done by a qualified
electrician and comply with all local codes and
regulations
General
General
General Information
Information
Information
Typical Installations are shown in
and
. They are
only a guide for selecting and installing system
components. Contact your Verder distributor for
assistance in planning a system to suit your needs.
Always use Genuine Verder Parts and accessories.
Be sure all accessories are adequately sized and
pressure rated to meet the system’s requirements.
Reference letters in the text, for example (A), refer to
the callouts in the figures.
Tighten
Tighten
Tighten Connections
Connections
Connections Before
Before
Before First
First
First Use
Use
Use
After you unpack the pump, and before you use it for
the first time, check and tighten all pump clamps and
fluid connections before operating the equipment.
Replace worn or damaged parts as necessary.
Tips
Tips
Tips to
to
to Reduce
Reduce
Reduce Cavitation
Cavitation
Cavitation
Cavitation in a double diaphragm pump is the
formation and collapse of bubbles in the pumped
liquid. Frequent or excessive cavitation can cause
serious damage, including pitting and early wear of
fluid chambers, balls, and seats. It may result in
reduced efficiency of the pump. Cavitation damage
and reduced efficiency both result in increased
operating costs.
Cavitation depends on the vapor pressure of the
pumped liquid, the system suction pressure, and the
velocity pressure. It can be reduced by changing any
of these factors.
1.
Reduce vapor pressure: Decrease the
temperature of the pumped liquid.
2.
Increase suction pressure:
a.
Lower the installed position of the pump
relative to the liquid level in the supply.
b.
Reduce the friction length of the suction
lines. Remember that fittings add friction
length to the lines. Reduce the number of
fittings to reduce the friction length.
c.
Increase the diameter of the suction lines.
d.
Ensure the inlet fluid pressure does not
exceed 25% of the outlet working pressure.
3.
Reduce liquid velocity: Slow the cyclic rate of
the pump.
Pumped liquid viscosity is also very important but
normally is controlled by factors that are process
dependent and cannot be changed to reduce
cavitation. Viscous liquids are more difficult to pump
and more prone to cavitation.
Verder recommends taking all of the above factors
into account in system design. To maintain pump
efficiency, supply only enough power to the pump to
achieve the required flow.
Verder distributors can supply site-specific
suggestions to improve pump performance and
reduce operating costs.
859.0769
11