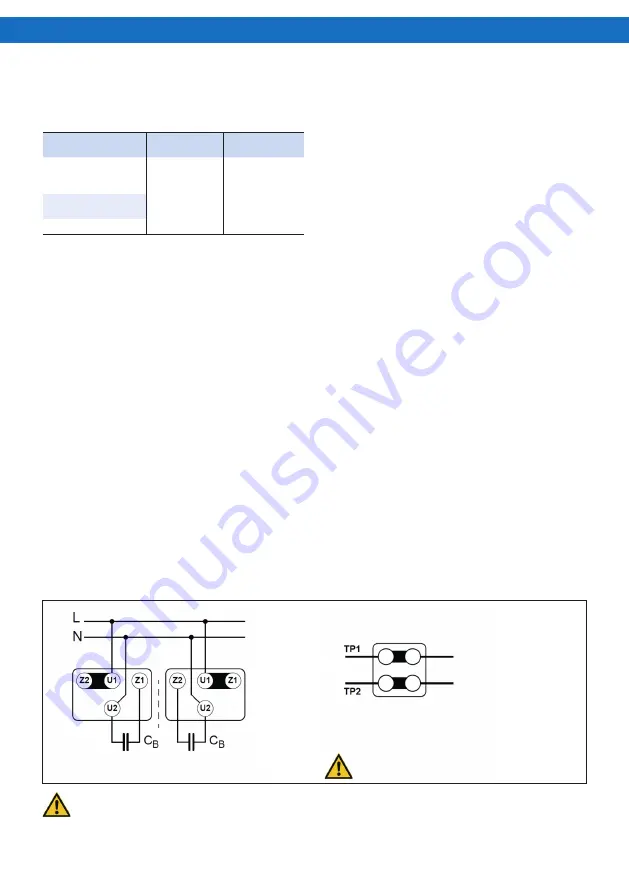
English
(translation)
4
10.2017
60205045
10. Bearings and lubrication
The roller bearings of the motors in standard confi gurati-
on are lubricated by the bearing manufacturer (or at the
factory) using roller bearing grease in accordance with
DIN 51825 as shown in the following table:
At full capacity, the lubricant quality permits running
the motor for approximately 10000 operating hours for
2-pole confi gurations and 20000 operating hours for
multi-pole confi gurations without replacing the roller
bearing lubricant, unless agreed otherwise. The speci-
fi ed number of operating hours only applies to operation
at nominal rotational speed.
11. Draining Condensate (optional)
At sites where condensation and the formation of
condensate inside the motor must be expected, the
accumulated condensate needs to be drained at regular
intervals using the condensate drainage opening at the
lowest point of the bearing shield; when done, the open-
ing must be closed again.
12. Cleaning
To ensure the effectiveness of the air cooling, all parts
of the motor need to be cleaned regularly. Usually,
cleaning with compressed air (water-free and oil free)
is suffi cient. In particular the ventilation openings and
spaces between the fi ns need to be kept clean. It is rec-
ommended to include the electric motors in the regular
inspections of the driven machine.
13. Motors with PTC resistors (TPM)
Continuity testing of the PTC resistor sensor circuit with
test lamp, magneto or similar is strictly prohibited, since
this would lead to the immediate destruction of the sen-
sor. If an additional measurement of the cold resistance
(at approx. 20°C) of the sensor circuit is necessary,
the measurement voltage may not exceed 2.5 V DC.
It is recommended that the measurement be carried
out using a Wheatstone bridge with a supply voltage of
4.5 V DC. The cold resistance of the sensor circuit may
not exceed 810 Ω. A measurement of hot resistance is
not required. For motors with thermal coil protection,
precautions need to be taken to ensure that after the
thermal coil protection has responded and after the mo-
tor has cooled down, an unintentional automatic restart
will not cause any danger.
14. Warranty, repair, spare parts
Our authorised repair shops are responsible for repairs
under warranty, unless expressly agreed otherwise.
They can also perform any other repair work that may
become necessary in a professional manner. For infor-
mation about how our customer service works, please
contact the factory. Proper maintenance as specifi ed in
the Maintenance section does not count as tampering
under the terms of the warranty. It therefore does not
release the factory from its agreed obligations under the
warranty.
15. Electromagnetic compatibility
The compliance of the motors as dependent compo-
nents with the EMC standards has been verifi ed. The
system operator is responsible for ensuring by means of
suitable measures that devices or entire systems meet
the relevant electromagnetic compatibility standards.
16. Terminal socket connections
(standard confi guration):
Connection of tripping unit:
done according to the connection diagram
of the tripping unit.
Do not apply voltages greater than 2.5 V!
Motor with PTC resistor:
(terminal socket connection as shown on the left)
Counter-clockwise
Clockwise
Check that all terminal connections are fi rmly seated before putting the machine into operation!
From
motor
Type series
Lubricating
grease
Lubricating
grease base
Squirrel-cage motors
IEC/DIN 56 – 132T and
Transnorm 56 – 100
Asonic GLY 32
or
Multemp SRL
Lithium soap
Motors with separate
fans
Brake motors
English
(translation)