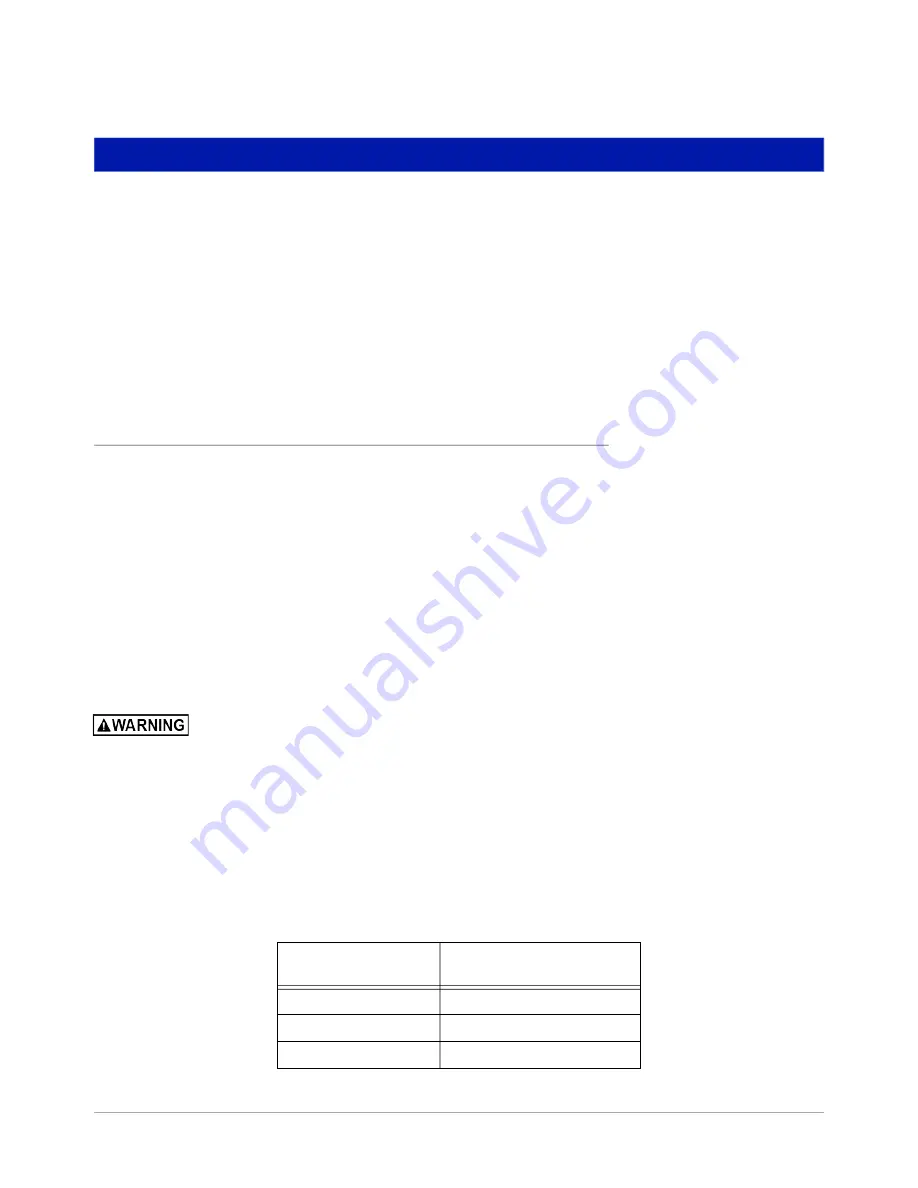
6
Installation
This pumping system requires the following elements:
1. Discharge Manifold Assembly - Installed below grade (NEC/Class I, Group D, Division I area)
2. Motor-Pump Unit Assembly - Installed below grade (NEC/Class I, Group D, Division I area)
3. Control Box/Magnetic Starter
An “all inclusive” name plate will be found attached to the Extracta Head and can be inspected by removing
the manhole cover directly over the pump.
An additional name plate will be found on the control box. It is important to give the model number and serial
number of this pump when corresponding with the factory for any reason.
INSTALLATION SAFETY NOTICES ATTENTION INSTALLER
• All submersible turbine pumps, manifolds and associated equipment shall be installed in accordance with the
manufacturer’s installation, operation and service manual supplied.
• All installations shall provide reliable electrical connection between the submersible turbine pumps, frame,
piping, manifold or junction box and the tank structure for the electrical protection and equipotential bonding.
• Repairing and adjusting of the electric motor is not allowed. Only change it completely assembled with
appropriate motor from the Manufacturer.
• Fasteners securing the discharge head shall be replaced only by identical fasteners.
READ THIS IMPORTANT SAFETY INFORMATION BEFORE BEGINNING WORK.
1. Units should be installed with manholes, or with discharge manifold casting above grade, to allow for ease in
servicing.
Line leak detection systems do not function if the submersible pump runs continuous
-
ly. Running a pump continuously will cause line leak detection systems to not function
which results in a hazard that can cause damage to property, environment, resulting in
serious injury or death.
2. Never wire a submersible pump to run continuously at less than minimum flow rate. The units are designed to
operate continuously at or above minimum flow rate, or with an intermittent duty cycle, not to exceed 20 on/off
cycles per hour. Should it be necessary to operate a unit continuously or when the demand is at a rate less
than required per the information below, a bypass pipe should be installed in the piping to allow for continual
product recirculation back into the storage tank. Regulation of the bypass flow back to the tank can be
accomplished by correct sizing of the bypass line or use of a gate valve. The recommended minimum bypass
per unit is shown in Table 1.
Table 1. Minimum Recommended ByPass Flow
60 Hz, 208-240, 575 Volt
Two Stage Units
50 Hz 380-415 Volt
Three Stage Units
P300J4-2HB = 20 GPM
P300J17-3HB = 20GPM
P500J4-2K = 25 GPM
P500J17-3K = 25 GPM
P500J6-2K = 25 GPM
Содержание Maxxum Big-Flo 6
Страница 16: ...Installation Wiring the Conduit Box 12 Figure 4 Three Wire Three Phase Motor Wiring Diagram...
Страница 43: ......