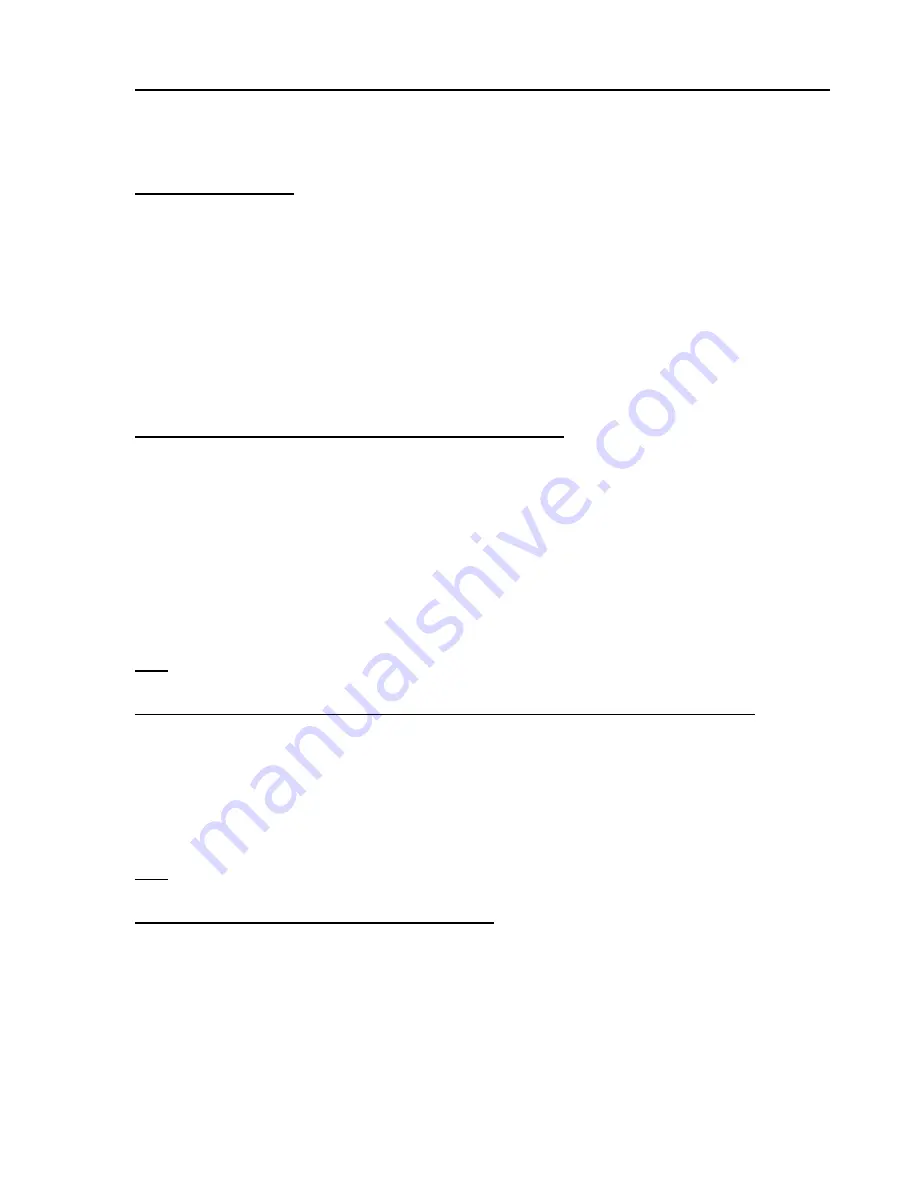
VANNER
Incorporated
OWNER’S MANUAL
Vanner High Voltage DC-
DC Converter OWNER’S MANUAL
24
Dual HBA's - General Description
Paralleling Two HBA's
Two versions of HBA's,
HBA400-28-CAN-DUAL
and
HBA500-28-CAN-DUAL
, have been developed to
load share when the outputs are connected in parallel. Two HBA400-28-CAN-DUAL HBA's connected in
parallel provide 500A of 28V charging current and two HBA500-28-CAN-DUAL HBA's connected in
parallel provide 600A of 28V charging current.
When connected in parallel, one unit is designated as the "Primary" (Master) unit and the other as
"Secondary" (Slave) by installing external jumpers in the circular I/O connector. To designate a unit as
the Primary, install a jumper between pins "M" and "N". To designate a unit as the Secondary, install a
jumper between pins "A" and "N". (See wiring diagram on next page.)
The two units communicate with each other via the vehicle CAN network with the Primary unit providing
voltage and control loop logic information for the Secondary unit. Any imbalances introduced to the
system, i.e. rapid load changes, are automatically compensated for to ensure equal load sharing.
System Response to Vann-Bus Dynamic Voltage Regulation
If the 28V batteries are in a discharged state, the output voltage of the Primary unit will increase to a
value prescribed by the battery monitoring software. Since its reference voltage will be higher than the
Secondary unit, it will provide the majority of the load. The Primary unit will request a higher output
voltage from the Secondary unit causing its output voltage to increase at a rate of 10mV/s. Once the
voltage differential between the two units is approximately
≤ 0.5V, the Secondary unit will begin to provide
more current. Once the voltage differential is approximately
≤ 0.1V, the units will load share evenly.
After the batteries reach a quiescent state, the output voltage of the Primary unit will reduce to a value
prescribed by the battery monitoring software. Since the reference voltage of the Secondary will be
higher, it will provide the majority of the current. The output voltage of the Secondary unit will begin to
reduce at a rate of 10mV/s. Once the voltage differential is approximately
≤ 0.1V, the units will load share
evenly.
Note
: The maximum and minimum output voltages of the HBA's can be set via Vanner's Dashboard
Interface Software.
System Response to a Failed Converter, Fault Condition or Loss of +24V Enable Signal
If either unit shuts down due to a failure, fault condition or loss of +24V enable signal, the operational unit
will remain on and provide current up to 250A or 300A. If the load is above 250A or 300A, the operational
unit will begin current limiting and gradually reduce the output voltage. Once the HBA output voltage
decreases to a value less than or equal to the battery voltage, the batteries will begin to assist in
supporting the load. If the load continues to increase and the output voltage drops to 20V, the current will
begin to fold back. If the output voltage is reduced to 16V, the HBA will turn off.
If certain fault conditions clear or the +24V enable signal is restored, the HBA will restart automatically.
Note
: Some fault conditions, once cleared, require cycling the ig24V enable signal before the HBA
will restart.
System Response to Loss of CAN Communication
If either unit loses CAN communication both will continue to run, however, their voltage and current loop
controls will function independently of each other. Once CAN communication is restored, voltage and
control loop controls will be maintained by the Primary unit.