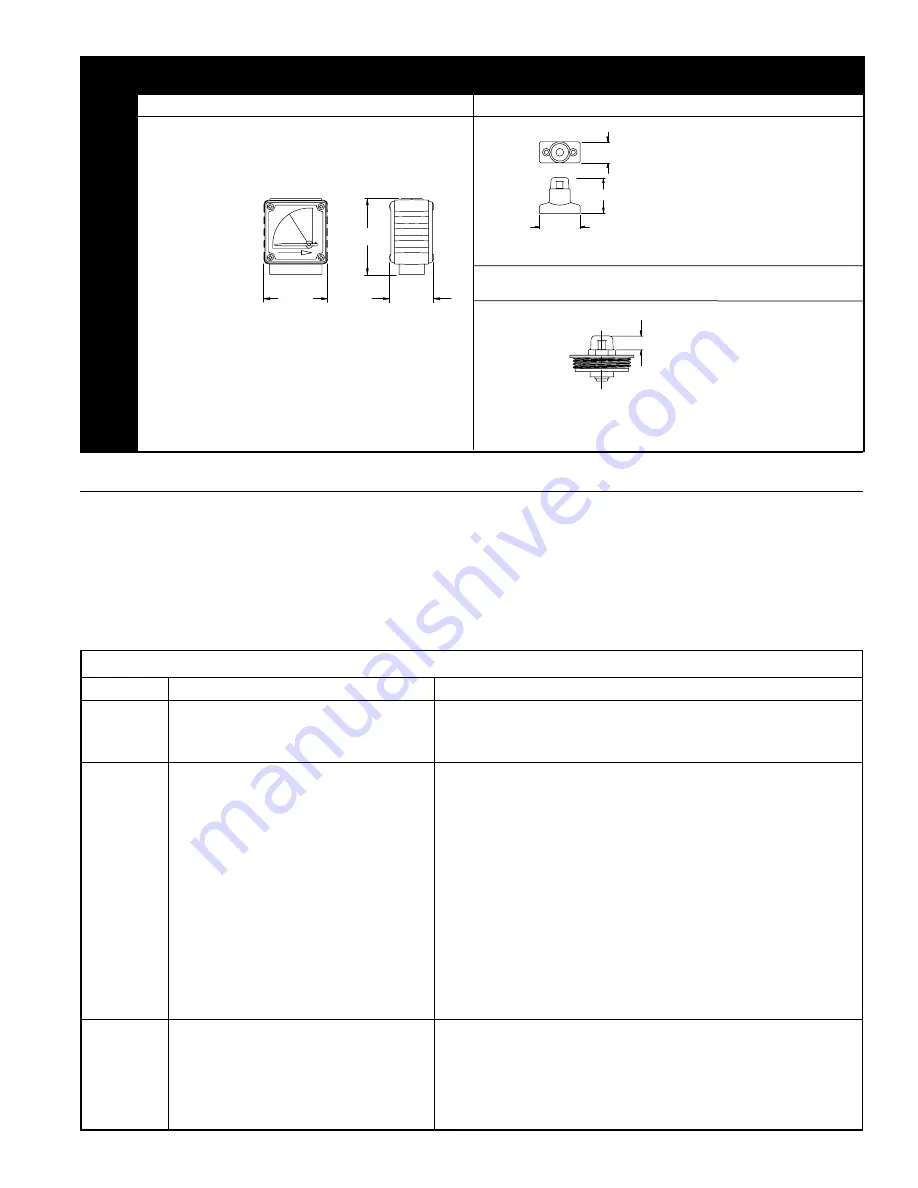
PAGE 7
2-1/8"
2-1/8"
3-3/8"
2-1/4"
2-5/8"
1-1/2"
1/2"
1"
1-11/16"
1-7/8"
DIFFERENTIAL
PRESSURE
INDICA
TOR KITS
PD-5 (P/N: 84-10001)
PD-6 (P/N: 84-10125)
KIT INCLUDES (1) PD-6, (2) SCREWS, (4) O-RINGS &
INSTRUCTION SHEET.
FITS ALL MODELS EXCEPT F200-15-1/4 THRU 25-1/2.
FITS ALL MODELS EXCEPT F200-15-1/4 THRU 25-1/2.
ACCESSORIES CONT'D
MAINTENANCE
Drain coalescing filters every shift.
Check differential pressures weekly on coalescing and
particulate filters (AA/RAA, A/RA, B/RB, and C/RC grades).
When the indicator is red on differential pressure indicator,
install clean elements. On adsorbing filters (grade RD), install
clean elements when hydrocarbon vapors are first detected
downstream or every six months, whichever comes first.
•
•
For correct replacement element model numbers, see label
on filter housing, the bottom endcap of the element, or page
5 of this instruction manual.
When changing out element, inspect housing o-ring for nicks
and/or cracks. If nicks and/or cracks are present, replace
o-ring.
•
•
PD-6A-C (P/N: 84-10126)
PD-6A-P (P/N: 84-10127)
FITS MODELS F200-15-1/4 THRU 25-1/2 ONLY.
PD-6A-C
FOR COALESCING
FILTERS
PD-6A-P
FOR PARTICULATE
FILTERS
KIT INCLUDES (1) PD-5, (2) SCREWS, (4) O-RINGS &
INSTRUCTION SHEET.
*DIMENSIONS EXTENDING ABOVE FILTER HOUSING.
KIT INCLUDES (1) PD-6A, (2) O-RINGS & INSTRUCTION SHEET.
*DIMENSIONS EXTENDING ABOVE FILTER HOUSING.
*
*
*
TROUBLE SHOOTING
CONDITION
POTENTIAL CAUSE
RECOMMENDATION
Initial pressure
drop too high
Filter undersized for flow rate.
Install larger filter.
Filter grade too fine.
Install coarser grade element.
Filter inlet smaller than pipe size.
Install larger filter.
Oil carryover
Oil present in system before installing filter.
Clean piping.
Excessive inlet oil >50ppm.
Check compressor and/or gas/oil separator if compressor is rotary vane or screw type.
Check lube rate if reciprocating compressor. Install coarse coalescer for prefiltration.
Filter installed backwards.
Check flow direction (See page 1).
Filter bowl not being drained.
Drain more frequently.
High differential pressure.
Check differential pressure indicator, replace element if necessary.
Defective seal.
Check o-ring in element.
Incorrect element grade.
Use finer grade.
By-pass valve leaking or open.
Close valve. Check seals on valve
Unfiltered gas entering from source down stream of
filter.
Relocate filter or install additional filter.
High operating temperatures.
Install, clean, replace or relocate aftercooler, or relocate filter.
Cooling by refrigerated dryer.
Install grade C filter downstream of dryer.
Short element
life
Excessive contamination.
Install coarse particulate filter immediately upstream of existing filter.
High compression temperatures causing varnish/
carbon formation.
Use compression lubricant with good temperature stability. Lower lube rates where pos-
sible. Use coarser grade filter element.
Oil/water emulsion overloading element.
Inspect moisture separator. Remove water with better separation.
High viscosity oil or freeze-up due to low ambient
temperature.
Raise ambient temperatures. Heat trace inlet piping and housing.