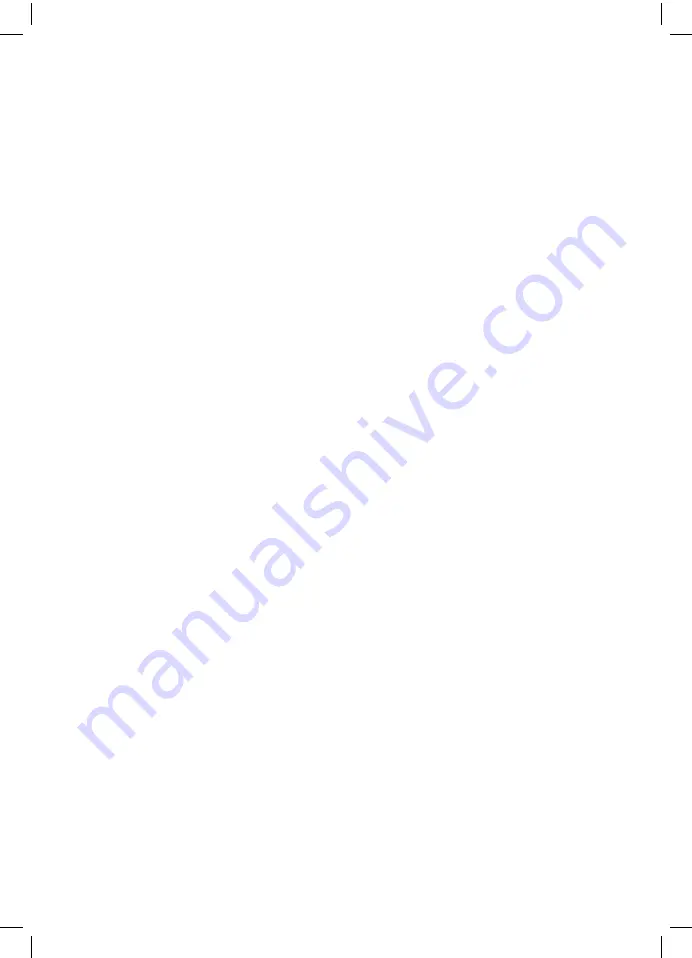
- 14 -
lower measurement than the height of the teeth.
CUTTING INCLINATION ADJUSTMENT
This is obtained by putting the guide panel on a
slope in relation to the blade.
Loosen the front handwheel (pos.2) and put
the guide panel on a slope to obtain the desired
cutting angle. Fix the handwheel(s) well after
making the adjustment.
With angles over 0°C, the cutting depth is less
than that indicated on the scale in pos.17.
USING THE GUIDE SET SQUARE (Fig.A and
Fig.D)
The guide set square (pos.11) is used for making
parallel cuts to the edge of the panel.
To adjust the distance of the cut from the edge
of the panel, loosen the handwheel (pos.12) and
slide the set square into the relevant guide; check
the cutting distance on the graduated scale. Fix
the handwheel well after the adjustment.
Should you need to carry out a parallel cut, at a
distance greater than the maximum one allowed
by the guide set square, use a strip of wood
fixed with clamps (not supplied) to be used as
a parallel cutting guide, see Fig.D.
MARKING THE CUTTING AREA (pos.22)
The two grooves on the guide panel indicate the
position of the blade in case of a perpendicular
cut with a 0° angle or on a 45° slope. It is re-
commended to check the correct alignment by
making a trial cut first.
PANEL BEING PROCESSED
The panel that you are going to cut must have
a compatible thickness with the circular saw.
Mark the cutting line with a ruler on the piece
and position it on trestles. Under the panel, in
correspondence with the cutting line, there must
not be any obstacles.
Important! For your safety it is important for
the panel to be fixed firmly, so that it doesn’t
fall once it has been cut, causing a risk for the
operator. Do not cut circular sections, old or
fragile wood, irregular wood, cracked wood,
wood with nails or screws, branches or trunks.
Always carefully inspect the piece.
PERFORMING THE CUT
Some types of panels could chip in the area
where the blade comes out: take care to perform
the cut resting the tool on the less important
part of the panel.
Carefully fix the piece to be cut, perform all the
adjustments to the tool and always connect up
the vacuum system pipe.
Plug the tool into the mains and grip it firmly
with both hands (Fig.C); rest the front part of the
guide panel on the edge of the panel (make sure
the mobile guard is closed) and start the tool.
Before starting to cut, wait a few seconds so that
the electrical tool reaches its full rotation speed.
Slowly move forwards while the mobile guard
(pos.10) moves automatically coming into
contact with the edge of the panel. Then main-
tain the right moving speed to ensure that there
is no reduction in the number of revolutions.
Excessive moving speeds can cause the blade
or the electrical tool to break.
At the end of the cut, release the switch and wait
for the blade to stop completely before extracting
it from the material or resting the tool.
Before resting the machine, always check that
the mobile guard has completely covered the
blade teeth.
CIRCULAR BLADE
IMPORTANT! The cutting part can cause se-
rious injuries – use protective gloves!
- Use good quality blades with the same cha-
racteristics as the circular saw based on its
technical data - your retailer will be able to help
you make the correct choice. Also observe
any instructions provided with the equipment.
- Do not use blades if you do not know where
they are from or without technical specifica-
tions. They must show the nominal dimen-
sions, the number of teeth, the maximum
number of revolutions and the arrow indicating
the rotation direction.
- The number of revolutions and the dimensions
are the basic elements for making your choice.
The number of revolutions must always be
higher or equal to that shown on the machine.
The dimensions must be equal to those shown
on the machine.
- Use blades which conform to the regulations
in force in the country of use.
- Do not use HSS (high speed steel) blades,
abrasive truncating discs or abrasive grinding
wheels.
- Always carry out a simple visual check: there
must be no deformations, breakages, damage
or rust.
Our company provides a complete series of