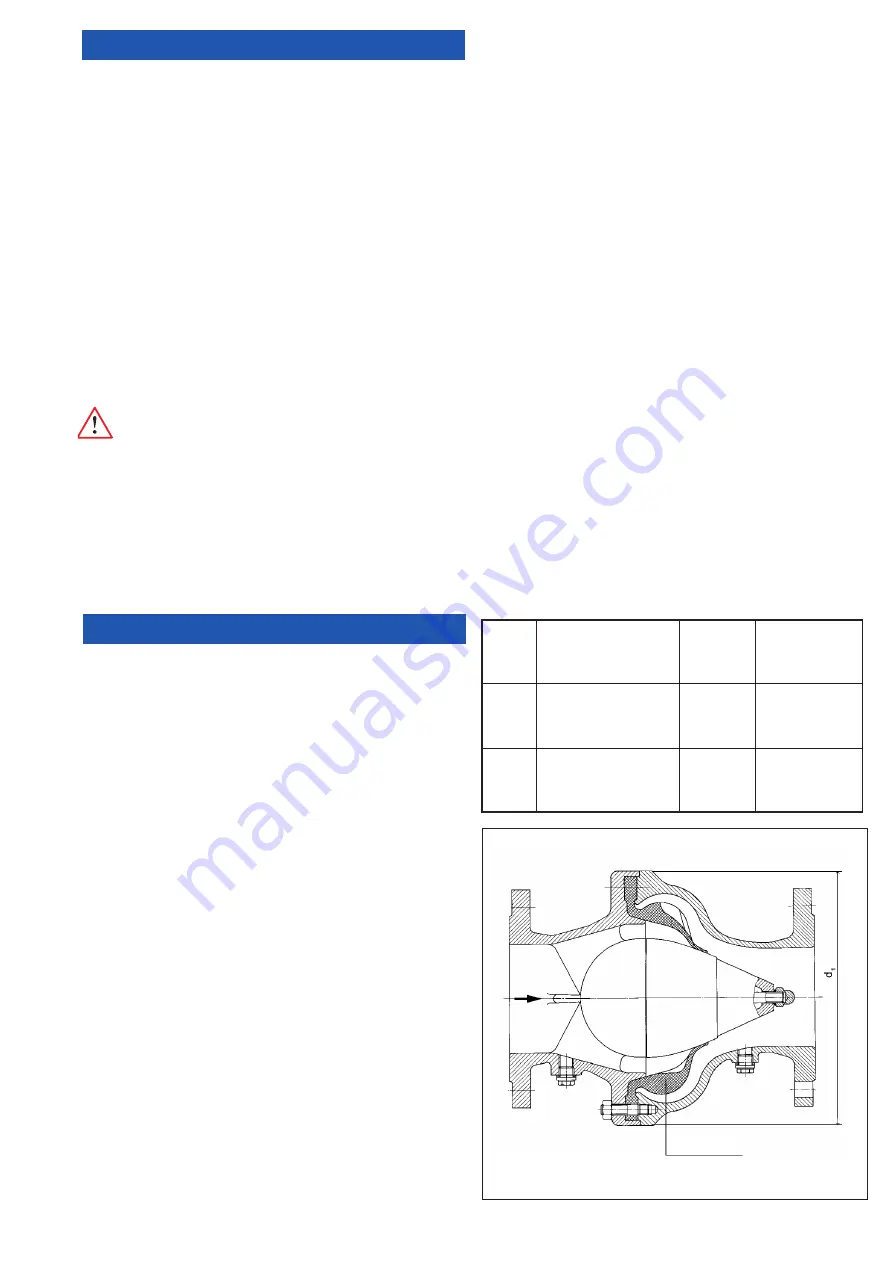
5.1 Visual inspection and preparation
Before putting the valve and the equipment into operation, per-
form a visual inspection of all functional parts. Check whether
all bolted connections have been properly fastened.
5.2 Function check and pressure test
Warning!! The pressure exerted on the closed valve must not
exceed its nominal pressure (see technical data sheet KAT
1543-A). When a pressure test is performed on the pipeline
during which the test pressure exceeds the permissible rated
pressure in the closing direction of the non-return valve, pres-
sure compensation must be ensured via a bypass.
Prior to any tests, newly installed pipeline systems should be
carefully purged to remove all foreign particles. If residues or
dirt particles are left in the pipeline, they may clog the installa-
tions during the purging procedure. This may impair the
function of the valve or even obstruct it completely.
When using detergents / disinfectants, make sure they do
not attack any of the valve materials.
5. Set-up and operation of the valve
6.1 General safety instructions
Prior to the performance of inspection and maintenance work
on the valve or its assemblies, shut-off the pressurised pipeline,
depressurise it and secure it against inadvertent activation.
Depending on the kind and dangerousness of the fluid convey-
ed, comply with all required safety regulations!
After completing the maintenance works and before resuming
operation, check all connections for proper fastening and
tightness. Perform the steps described for initial set-up as
described under Section 5 "Set-up and operation".
Statutory and local provisions as well as the safety and accident
prevention regulations must be observed and complied with at
all times.
Couplings and connections must never be disassembled when
they are under pressure.
Servicing, maintenance and inspection work as well as the
replacement of spare parts must only be done qualified staff.
The plant operator is responsible for determining the suitability
of the staff or for ensuring the relevant qualifications. In case the
operator's employees do not have the qualifications required,
they need to attend a training course. This training course can
e.g. be held by VAG Service employees.
In addition to this, the plant operator needs to ensure that all
employees have understood these Operation and Maintenance
Instructions as well as all further instructions referred to in them.
Protective equipment such as safety boots, safety helmets,
goggles, protective gloves etc. must be worn during all work
6. Maintenance and repair
requiring such protective equipment or for which such protec-
tive equipment is prescribed.
Improper or wrong use of the valve should be avoided. Prior to
the performance of any work on the valve and equipment it
must be ensured that the relevant pipeline section has been
depressurised and/or de-energised.
6.2 Inspection and operation intervals
The condition and function of the diaphragm should be
checked at least once per year (DVGW Instruction Sheet W
392).
In case of extreme operating conditions inspection should be
performed more frequently.
6.3 Maintenance work and replacement of
parts
For information about the spare parts and wearing parts nee-
ded, please refer to the spare parts list in Section "6.3.1
Design".
6.3.1 Design
Item
Designation
Material
d1 dimensions
in mm
1
Circular diaphragm
NBR
150, 175, 220,
292, 374, 446,
550,645, 720
1
Circular diaphragm
EPDM
150, 175, 220,
292, 374, 446,
550,645, 720
1