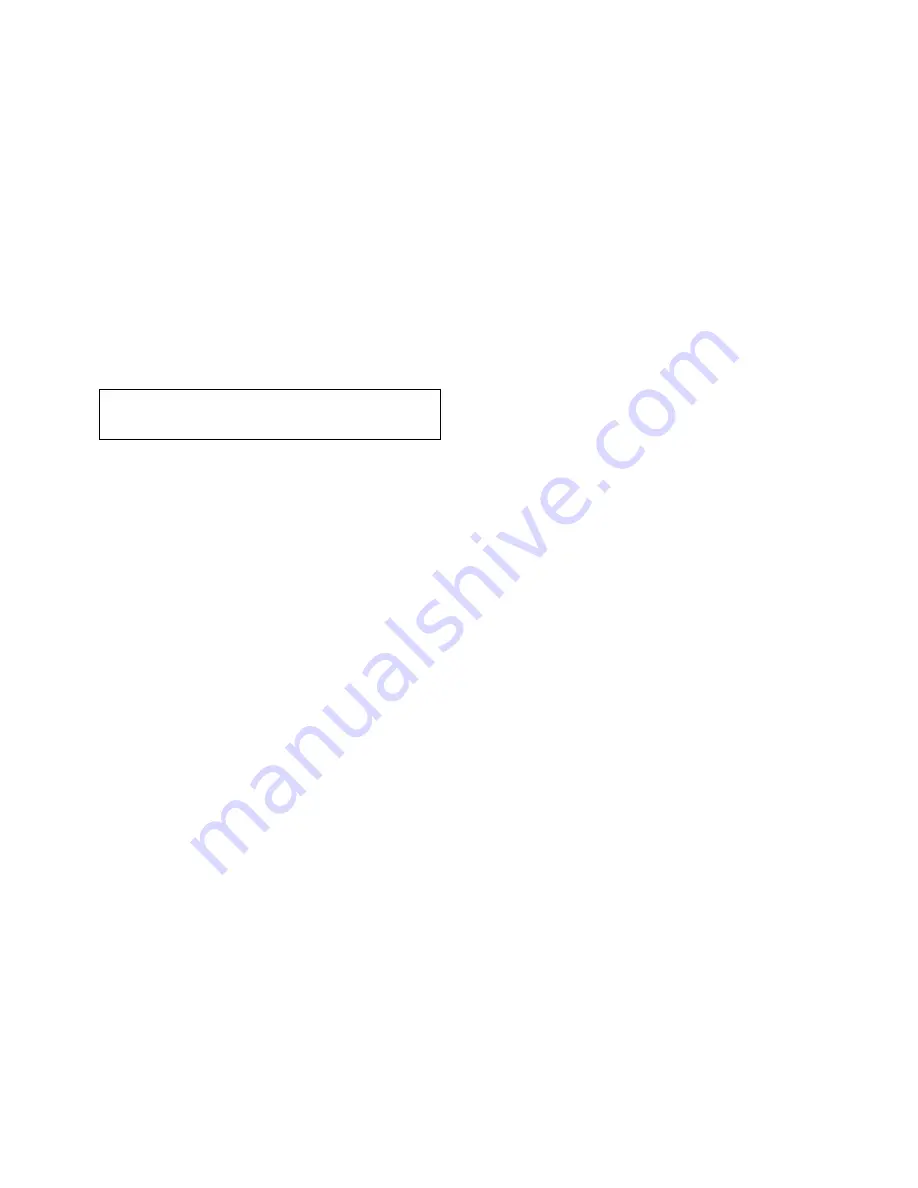
1
INSTALLATION, OPERATION and
MAINTENANCE
3
” and 4” Combination Air Valves with Surge Check
INTRODUCTION
This manual provides information to install, operate
and maintain GA Industries pilot-operated pressure
reducing valves to ensure a long service life. The
valve is ruggedly constructed to provide many
decades of dependable service with minimal
maintenance.
CAUTION
The valve is NOT recommended for use with toxic,
corrosive, or flammable fluids.
The Shop Order (SO) Number, Figure Number, size,
and pressure rating are stamped on a nameplate
attached to the valve. Please refer to the SO number
when ordering parts.
The Figure 983-D is suitable for use with finished
water, raw water and treated effluent that is free of
debris.
DESCRIPTION OF OPERATION
The Figure 983-D consists of a Figure 930-D flanged
air & vacuum valve, a Figure 905 air release valve
and a Figure F284-D surge check, factory assembled
and tested as a unit.
Refer to Page 2 for identification and location of the
individual valves that comprise the assembly.
The valve is open when void of water. Air is
discharged through the air vacuum valve
’s large
orifice as the system is filled with water. An excessive
air discharge rate closes the surge check to reduce
the discharge area, slowing the air & vacuum valve
closure to reduce slam and surge associated with a
sudden air valve closure. After the air & vacuum
valve is closed and the system is pressurized, any air
that collects in the valve is automatically vented
through the air release valve
’s small orifice. The air &
vacuum valve re-opens to admit air when the system
is drained, or a negative system pressure occurs.
RECEIVING AND STORAGE
Inspect the valve upon receipt for damage during
shipment. Carefully unload all valves to the ground
without dropping.
Valves should remain in a clean, dry, and weather
protected area until installed. After completion of
shop testing the valve is drained of the test water but
a small residual amount could remain so the valve
should be protected from freezing during storage.
INSTALLATION
Figure Number 983-D has an ANSI Class 125 flanged
pipeline connection. The standard valve has an NPT
threaded outlet that can be piped to a drain.
The valve must be installed in a vertical orientation for
it to properly function.
Prior to installation ensure all debris, packing material
or other foreign material has been removed from both
ports.
If installed outdoors, below ground in a vault or in an
unheated area, adequate freeze protection must be
provided.
Adequate isolating valves should be installed between
the valve and the pipeline or system to facilitate
maintenance. If a butterfly valve is used, be aware of
the required disc clearance shown in the O & M for
the Figure 284-D.
The valve should be installed with sufficient clearance
to permit maintenance and removal of internal
components.
The valve is not designed to support adjacent
equipment, piping loads should not be imposed on the
valve and large valves should be properly supported.
Flat-faced flanged valves should be mated with flat-
faced flanges and full-face gaskets. If ring gaskets
are used the bolt material shall be ASTM A307 Grade
B (or equivalent). Higher strength bolting should only
be used with full-face gaskets.
Lower heavy valves using slings or chains around the
valve body and/or the lifting eyes. DO NOT LIFT BY
THE EXTERNAL PIPING. Lubricate the bolts or
studs and insert around flange. Lightly tighten bolts
until gaps are eliminated. Torque bolts in an
alternating pattern in graduated steps. If leakage
occurs wait 24 hours and re-torque the bolts but do
not compress the gasket more than 50% or exceed
bolt maximum torque rating.
Содержание GA INDUSTRIES 905
Страница 2: ...Section 1...
Страница 6: ...Section 2...
Страница 11: ...Section 3...
Страница 16: ...Section 4...