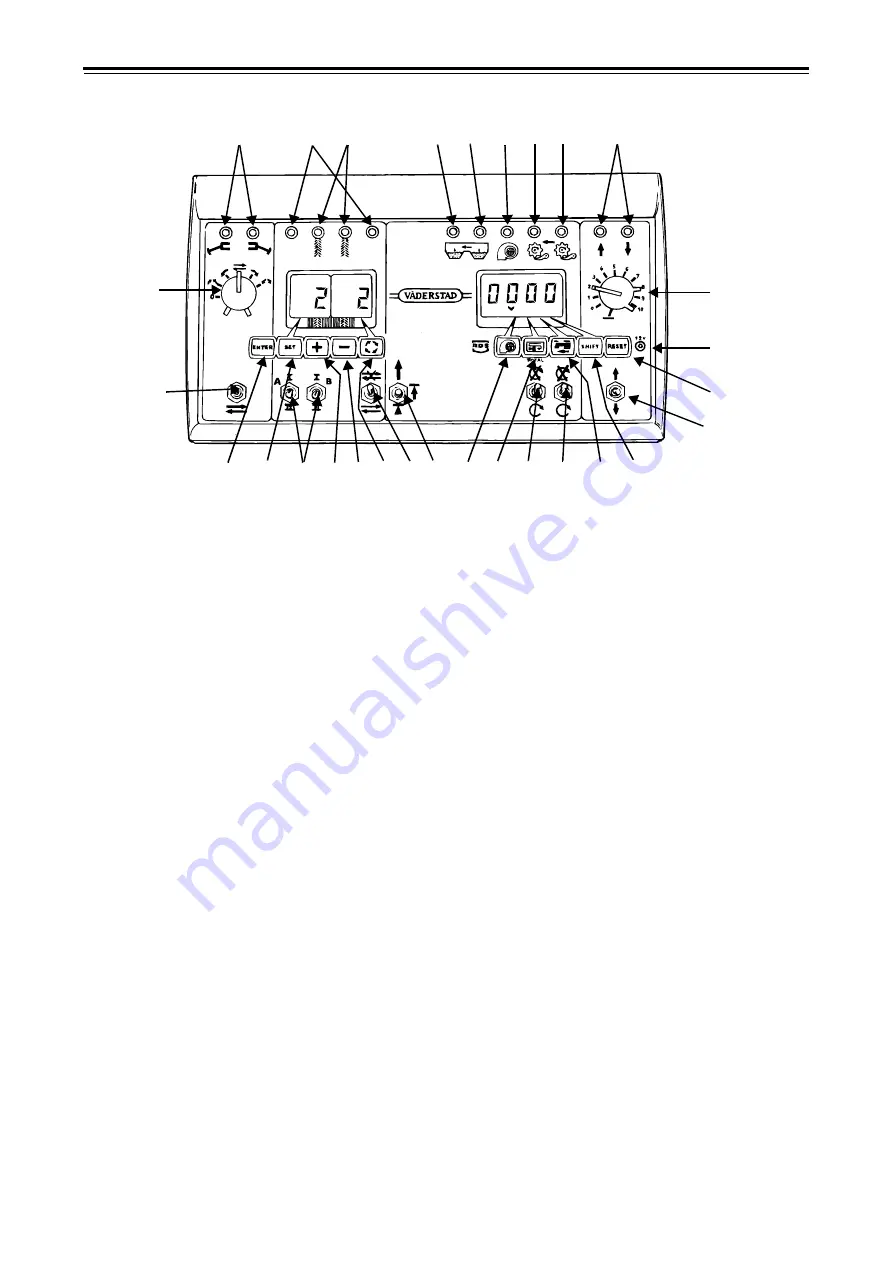
Instructions and settings
58
Ver.07/06/01 07/06/01
3.16.4 Settings and functions
Setting the bout markers
Figure 3.56
Set the bout marker function selector (2) to alternating for automatic changeover of the mar-
kers. Step the correct marker on before the first bout using the manual advance switch (1).
The lights (3) will only show power reaching the relevant hydraulic valve provided that the drill
is under Low lift height. The bout markers are activated when the hydraulic takeoff for lifting and
lowering is moved.
Obstructions
If there is an obstruction in front of a marker, Lift stop must be activated to allow the marker to be
moved without lifting the drill. This is done by putting switch 17 in the down position.
If there is an obstruction under the drill, Auto step (16) must be switched off and then 17 moved
to the up position (high-lift). Raise the drill with the hydraulic lever, drive over the obstruction
and lower the drill again. Start Autostep 16 and return 17 to its original position.
3
4
5
6A 6B
7 8A 8B
9
26
25
24
10
11
12 13 14 15 16 17 18 19 20A 20B 21 22
23
2
1
Содержание RAPID RD 300 F
Страница 1: ...Ver 1 3 07 06 01 900107 en Instructions Seed drill RAPID series RD 300 450 F No 10 026 11 999 ...
Страница 2: ...2 Ver 1 3 07 06 01 ...
Страница 6: ...6 Ver 1 3 07 06 01 ...
Страница 16: ...Assembly instructions 16 Ver 07 06 01 07 06 01 ...
Страница 23: ...RD 300 450 F Ver 1 3 07 06 01 23 ...
Страница 41: ...RD 300 450 F Ver 1 3 07 06 01 41 ...
Страница 47: ...RD 300 450 F Ver 1 3 07 06 01 47 ...
Страница 108: ...Appendices 108 Ver 07 06 01 07 06 01 7 4 Electrical diagram Figure 7 8 307335 ...