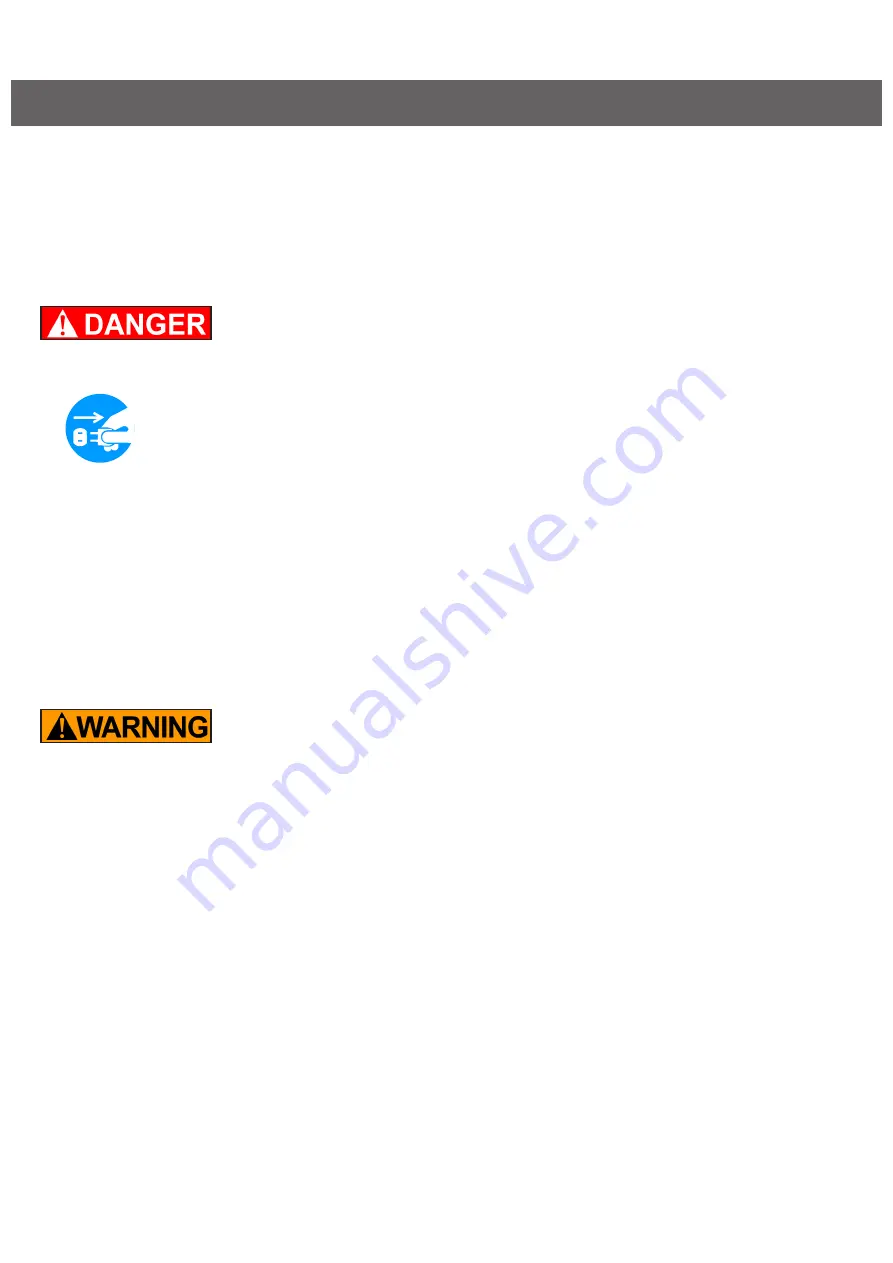
page 54 of 80
+
Please read section ”Replacing diaphragms and valves” com-
pletely before starting maintenance.
The pictures may show other versions of pumps. This does not change
the method of replacing diaphragms and valves.
➨
Never operate the pump if covers or other parts of
the pump are disassembled.
➨
Before starting maintenance,
disconnect the electri-
cal power cord
.
Wait five seconds
after isolating the
equipment from AC power to allow the capacitors to
discharge.
➨
Ensure that the pump cannot be operated accidentally.
➨
Note
: The pump might be contaminated with the pro-
cess chemicals that have been pumped during opera-
tion. Ensure that the pump is decontaminated before
maintenance.
➨
Avoid the release of pollutants.
+
Never operate a defective or damaged pump
.
+
Take adequate precautions to protect people from the
effects of dangerous substances that may have con
-
taminated the pump and may be released upon dis-
assembly. Ensure that the maintenance technician is
familiar with the safety procedures which relate to the
products processed by the pumping system.
Use appropriate protective clothing, safety goggles
and protective gloves.
+
Check every motor capacitor regularly by measuring
its capacity and estimating its service life. Replace old
capacitors early enough to prevent a failure. The ca-
pacitors must be replaced by a trained electrician.
+
Allow sufficient cooling of the pump before starting
maintenance. Drain condensate, if applicable.
+
Vent the pump and isolate it from the vacuum sys-
tem before you start maintenance.
Replacing diaphragms and valves
Содержание MD 4C NT
Страница 32: ...page 32 of 80 ME 4C NT 1 5 4 7 6 8 2 ME 2C NT 1 5 4 7 6 8 2 ...
Страница 34: ...page 34 of 80 ME 8C NT MD 4C NT 1 5 3 4 7 6 2 8 8 5 4 7 6 1 2 ...
Страница 57: ...page 57 of 80 Fittings and tubing of the different pump models ME 4C NT MZ 2C NT ME 8C NT MD 4C NT ...
Страница 73: ...page 73 of 80 Declarations and certificates ...
Страница 74: ...page 74 of 80 ...
Страница 78: ...page 78 of 80 ...
Страница 79: ...page 79 of 80 ...