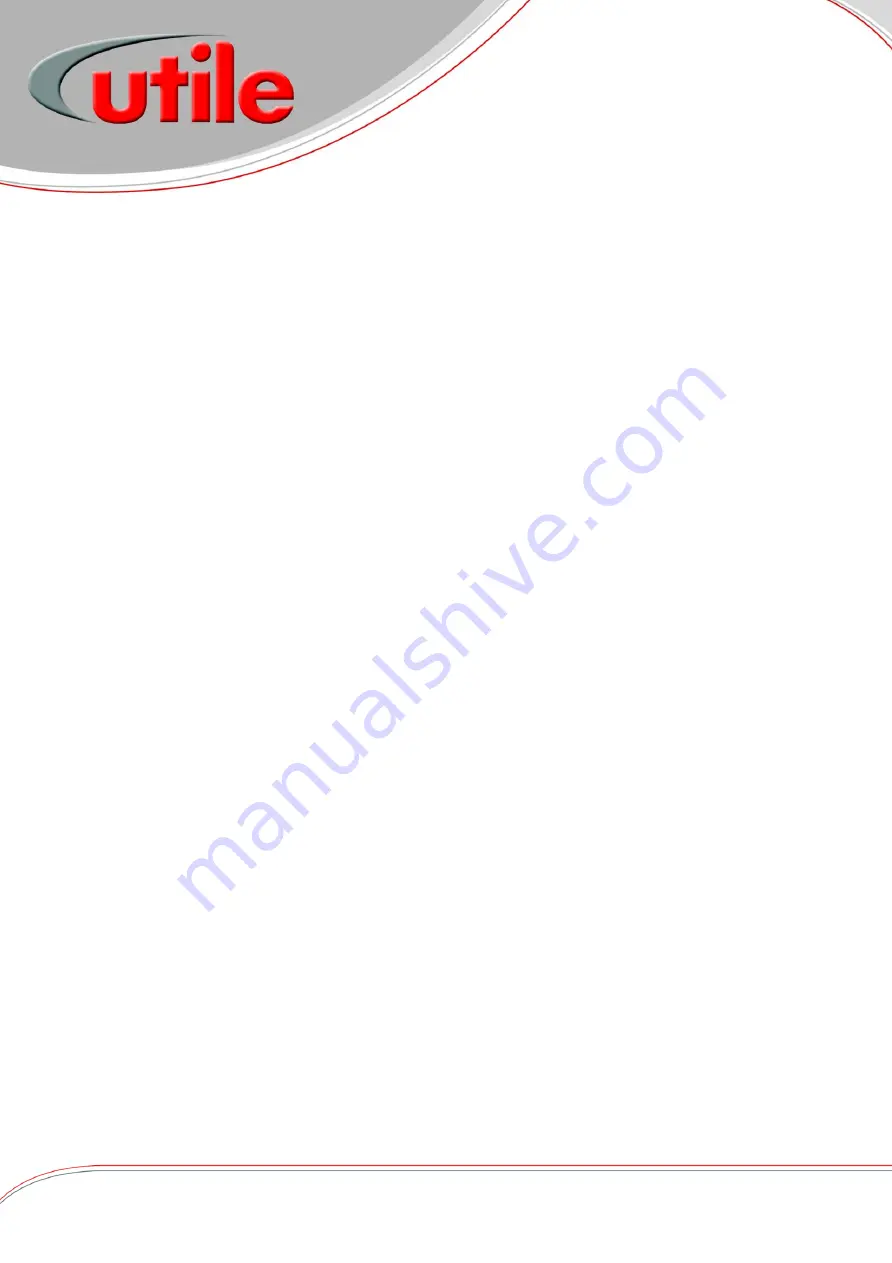
GAS COMPRESSORS / BOOSTERS
GAS & AIR MIXING SYSTEMS
AIR BLOWERS & VACUUM PUMPS
The Utile Engineering Co. Ltd.
Irthlingborough, Northamptonshire, NN9 5UG, ENGLAND
Telephone: + 44 (0) 1933 650216 Facsimile: + 44 (0) 1933 652738 Email: [email protected]
www.utileengineering.com
Feb-19
15
IC013 Rev2
Maintenance
Fully trained and competent staff must carry out any maintenance work. Utile Engineering offers contract maintenance services if
required contact our service department.
When carrying out any maintenance and inspections always follow the health and safety guidelines on page 4.
A regular correct maintenance plan is essential to good operational reliability and a long service life for your machine. As operating
conditions vary, no exact timings can be specified for wear checks, repairs and inspections, however the following plan can be used as
a guide until time scales to better suit the machines environment are found.
The machine, ancillaries and surrounding area should be kept as clean as possible.
Ensure all items are properly held and supported during all aspects of maintenance as not to pose a problem for health and safety.
Observe all lifting points and apply care when handling the equipment.
Ensure the electrical supply has been locked out and all machines and associated pipework have cooled down sufficiently before
touching and attempting any maintenance.
Typical tools required for maintenance include: -
Set of spanners
Pipe Wrenches
Circlip Pliers
Set of screwdrivers
Vernier Gauge / Micrometer
Two-leg Pulley drawer
Set of Allen Keys
Hammer / mallet
Feeler Gauges
Typical bolt tightening torques can be seen on page 6.
New gaskets must be fitted every time the machine is dismantled.
After maintenance the machine and equipment must be treated, as new and all pre-commissioning checks should be made. Install and
check all protective devices and controls properly after completion of work. All finished assemblies/pipework should then be pressure
tested to IGEM/UP/1. Ensure all cabling, unions and guards are correct, secure and in place. Dispose of any used oil and cleaning
solutions as prescribed by law.
Shaft Seals
These fitted on the shafts or sleeves prevent leakage of process fluid from contaminating the bearings. It is important to check the
seals at regular intervals for any signs of leakage. These must not be allowed to run dry, else premature failure will occur. They must
be of the same type and size as the original. Seals are recommended to be replaced after 15000 operating hours or 2 years whichever
is sooner.
Bearings
In all machines, one of the bearings will be fixed and the other shall be free. Where a ball and roller bearing are used the ball will be
the fixed bearing, and any axial movement will be permitted within the roller bearing. When 2 ball bearings are used, any axial
movement will be taken by the outer race sliding within the bearing housing. If 2 roller bearings are fitted then one of these will be
located.
These are packed for life with grease and do not require any maintenance prior to initial start-up.
These must not be allowed to run dry, else premature failure will occur and the machine may exceed the specified temperature limits.
The bearings have special internal clearances to allow for expansion and should be replaced with the same type and variant, or
machine failure may result.
When maintaining or replacing bearings, the working environment must be as clean as possible to prevent foreign particles from
getting into the bearing races and causing damage when running. Do not hammer them into position as this will damage the bearings
and cause premature failure these must be pressed into position. They must be of the same type and size as the original. Bearings are
recommended to be replaced after 15000 operating hours or 2 years whichever is sooner.
Bearing temperatures will vary with machine speed, pressure, power transmitted, vibration, ambient temperature and suitable
lubrication. It is not possible to accurately calculate bearing running temperatures and therefore bearing life. However, ensuring
vibration is within the recommended limits and keeping a record in the daily/weekly logbook the operator can show when things are
not operating as normal.
Maintenance